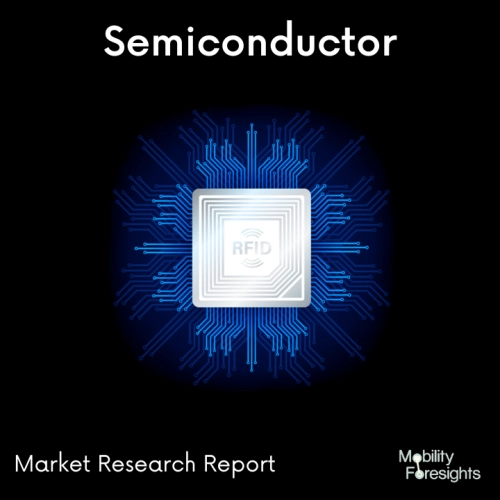
- Get in Touch with Us
Last Updated: Apr 27, 2025 | Study Period: 2024-2030
By Sequentially Alternating Between Self-Limiting Chemical Modification Steps That Only Affect The Top Atomic Layers Of The Wafer And Etching Steps That Only Remove The Chemically Modified Areas, Individual Atomic Layers Can Be Removed In The Emerging Semiconductor Manufacturing Technique Known As "Atomic Layer Etching."
The Most Common Instance Is The Alternation Of Etching Silicon With Argon Ions And Chlorine Reactions.
Although The Throughput Has Been A Problem With Commercial Usage Of This Technique, It Is A Better-Controlled Process Than Reactive Ion Etching.
Sophisticated Gas Handling Is Needed, And Removal Rates Of One Atomic Layer Per Second Are Roughly The State Of The Art.Atomic Layer Deposition Is The Analogous Procedure For Material Deposition (Ald).
Since Intel Uses Ald To Create High-Dielectric Layers And Finland Uses It To Create Thin Film Electroluminescent Devices, Ald Is Significantly More Developed.
The Global Atomic Layer Etching Market Accounted For $Xx Billion In 2021 And Is Anticipated To Reach $Xx Billion By 2030, Registering A Cagr Of Xx% From 2024 To 2030.
A Sophisticated Etch Method That Provides Great Depth Control On Shallow Features Is Called "Atomic Layer Etching" (Or "Ale"). Ale Is Necessary To Attain The Accuracy Needed For Peak Performance As Device Feature Sizes Get Smaller And Smaller.
Modern Sophisticated Microelectronic Device Manufacture Requires High Quality Pattern Transfer (Etching). There Is A Growing Need For Atomic-Scale Fidelity As Features Are Reduced To Sub-10nm Levels And Innovative Technologies Utilise Ultra-Thin 2d Materials.
Because Of This, Interest In A Method Called Atomic Layer Etching (Ale), Which Circumvents The Limits Of Traditional (Continuous) Etching At The Atomic Level, Is Developing.
Layers Of Material Are Removed Sequentially During The Cyclical Etching Technique Known As Plasma-Based Atomic Layer Etching, Which Uses Gas Dosing And Ion Bombardment.
Sl no | Topic |
1 | Market Segmentation |
2 | Scope of the report |
3 | Abbreviations |
4 | Research Methodology |
5 | Executive Summary |
6 | Introduction |
7 | Insights from Industry stakeholders |
8 | Cost breakdown of Product by sub-components and average profit margin |
9 | Disruptive innovation in the Industry |
10 | Technology trends in the Industry |
11 | Consumer trends in the industry |
12 | Recent Production Milestones |
13 | Component Manufacturing in US, EU and China |
14 | COVID-19 impact on overall market |
15 | COVID-19 impact on Production of components |
16 | COVID-19 impact on Point of sale |
17 | Market Segmentation, Dynamics and Forecast by Geography, 2024-2030 |
18 | Market Segmentation, Dynamics and Forecast by Product Type, 2024-2030 |
19 | Market Segmentation, Dynamics and Forecast by Application, 2024-2030 |
20 | Market Segmentation, Dynamics and Forecast by End use, 2024-2030 |
21 | Product installation rate by OEM, 2023 |
22 | Incline/Decline in Average B-2-B selling price in past 5 years |
23 | Competition from substitute products |
24 | Gross margin and average profitability of suppliers |
25 | New product development in past 12 months |
26 | M&A in past 12 months |
27 | Growth strategy of leading players |
28 | Market share of vendors, 2023 |
29 | Company Profiles |
30 | Unmet needs and opportunity for new suppliers |
31 | Conclusion |
32 | Appendix |