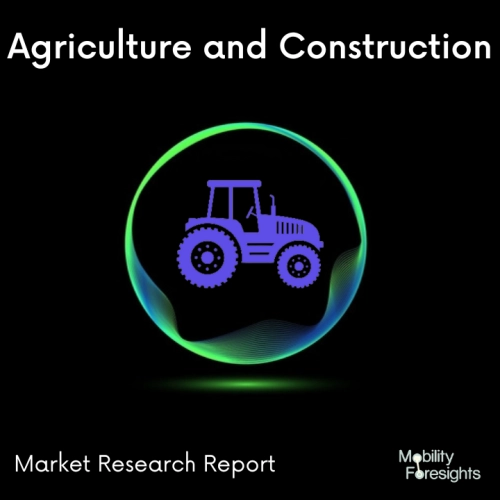
- Get in Touch with Us
Last Updated: Apr 25, 2025 | Study Period: 2023-2030
An Auger Boring Machine (ABM) is a machine used for tunneling and boring through a variety of soils and rocks. They are used to create underground tunnels, culverts, and other structures. Auger boring machines use a rotating auger to cut through the material.
The auger is mounted on a carriage which is moved along the tunnel axis by a hydraulic power unit. The power unit provides the pressure to rotate the auger and push the material out of the tunnel. ABMs are used in a variety of applications, including excavation of roads, bridges, and other structures. The tunnels created by ABMs can be up to 12 feet in diameter.
ABMs are generally used in soils that are too hard or too soft for traditional tunneling methods. They are also used in areas with limited access or space, such as beneath buildings and highways.
ABMs are usually powered by diesel engines and feature an automated guidance system to ensure accuracy and safety while boring. This automated system can be used to monitor the tunnel walls, the soil type, and the pressure of the auger.
Auger boring machines are typically used for projects that require a tunnel of a large diameter. They are also well-suited for projects that require a curved or angled tunnel. The machines can be customized to meet the specific needs of the project.
ABMs are a popular choice for construction projects due to their efficiency, accuracy, and cost-effectiveness. They are a cost-effective alternative to traditional tunneling methods and offer a safer and more efficient way to create tunnels.
The Global Auger Boring Machine market accounted for $XX Billion in 2022 and is anticipated to reach $XX Billion by 2030, registering a CAGR of XX% from 2023 to 2030.
McLaughlin introduced a new line of auger boring machines together with an electronic pitch indicator accessory and a steerable rock system. With five models in its lineup that vary in size and horsepower, McLaughlin was created to assist contractors in carrying out big diameter bores effectively in a range of ground conditions
Additionally, the company offers the On-Target Steering System (OTS) and Steerable Rock System (SRS). Although auger drilling is one of the more traditional trenchless installation techniques, it believes it has a place in the market alongside other technologies.
For the installation of casings with diameters ranging from 4 to 24 inches (10.2 to 61 cm), the new McLaughlin McL 24C auger boring machine offers remarkable thrust and torque.
The McL 24C is outfitted with a quiet and clean operating 24.6 horsepower (18.3 kW) Caterpillar 3-cylinder Tier 4 diesel engine. It can generate 98,000 pounds (44,452.1 kg) of forward force and 6,339 foot-pounds (8594.5 joules) of auger torque. Additionally, to lessen spinback and the possibility of machine rollovers, it has a patented hydraulic clutch called Operator Presence Control (OPC).
The track system and operator controls of the McL 24C auger boring machine have been modified. Rectangular steel tube, robust vertical rails, and thoughtful cross member placement are used in the tracks to offer stability and a smooth surface when pulling augers.
The newest machine in the McLaughlin lineup is the potent new WH 175 auger boring machine. With a diameter range of 16 to 42 inches (40.6 to 106.7 cm), the WH 175 auger boring machine can install casings with quiet, clean, and smooth operation. It is driven by a Volvo turbocharged diesel engine with 175 horsepower (130.5 kW), which can provide thrust up to 600,000 pounds (272,155.4 kg) and auger torque up to 85,000 foot-pounds (115,244.5 joules).
Operators can operate the auger boring machine on the project from any location thanks to the remote control feature of the McLaughlin WH 175 equipment. Moreover, it has the McLaughlin Rabbit Travel function, which shortens cycle times when adding augers or casing.
Sl no | Topic |
1 | Market Segmentation |
2 | Scope of the report |
3 | Abbreviations |
4 | Research Methodology |
5 | Executive Summary |
6 | Introduction |
7 | Insights from Industry stakeholders |
8 | Cost breakdown of Product by sub-components and average profit margin |
9 | Disruptive innovation in the Industry |
10 | Technology trends in the Industry |
11 | Consumer trends in the industry |
12 | Recent Production Milestones |
13 | Component Manufacturing in US, EU and China |
14 | COVID-19 impact on overall market |
15 | COVID-19 impact on Production of components |
16 | COVID-19 impact on Point of sale |
17 | Market Segmentation, Dynamics and Forecast by Geography, 2023-2030 |
18 | Market Segmentation, Dynamics and Forecast by Product Type, 2023-2030 |
19 | Market Segmentation, Dynamics and Forecast by Application, 2023-2030 |
20 | Market Segmentation, Dynamics and Forecast by End use, 2023-2030 |
21 | Product installation rate by OEM, 2023 |
22 | Incline/Decline in Average B-2-B selling price in past 5 years |
23 | Competition from substitute products |
24 | Gross margin and average profitability of suppliers |
25 | New product development in past 12 months |
26 | M&A in past 12 months |
27 | Growth strategy of leading players |
28 | Market share of vendors, 2023 |
29 | Company Profiles |
30 | Unmet needs and opportunity for new suppliers |
31 | Conclusion |
32 | Appendix |