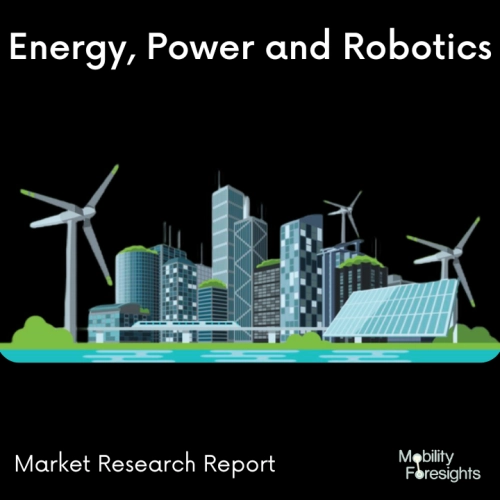
- Get in Touch with Us
Last Updated: Apr 25, 2025 | Study Period: 2024-2030
Heat shrink tubing, often known as electrical shrink tubing, is a critical protective and organizational component found in a wide range of electrical arrays.
In general, heat shrink tubing is a common component in most electrical installations because it protects electrical components from external factors such as moisture, dust, abrasion, and sharp objects that may otherwise harm cables and electrical components.
This type of deterioration eventually results in shorts and failures. It will also connect loose wires, connectors, joints, terminals, and splices to create more organized and manageable bundles.
A thermoplastic tube that shrinks when heated is known as heat shrink tubing. Heat shrink tubing shrinks radially to fit the forms of wire arrays and electrical components when wrapped around them, providing a protective covering.
Heat shrink tubing is created by first extruding a thermoplastic tube. The materials used in heat shrink tubing differ depending on their intended usage.
Following the extrusion of the required plastic, the material is heated and pressed to expand, increasing the diameter of the tube. Before being set, the inflated tube is allowed to cool to room temperature.
This expanded thermoplastic tube is then heated to a particular temperature before being wrapped around the wires or other components. The heat softens and reduces the tube back to its original extruded size, trapping the wires or other components beneath a protective plastic covering.
Electrical insulation, mechanical protection, environmental sealing, and strain relief are all benefits of heat shrink tubing.
Heat shrinkable tubing comes in single and dual wall types and is intended for use in a range of applications including back-end connector sealing, breakouts, and connector-to-cable transitions. It is an acceptable substitute for taping, molding, or potting.
Heat sleeves adapt to the size and form of the substrate beneath when heated, enabling for quick and easy installation.
Because of its high expansion ratio, most damaged cable jackets may be replaced without disconnecting connections.
Heat shrink tubing is available in a range of materials, colors, and diameters, as well as spools and chopped portions. Clear types feature a high light transmittance and enable for the study of covered components.
Heat shrink tubing materials can be used to protect and organize wires, connections, and other electrical components in both low-impact home and heavy-duty industrial applications.
Consolidated Electronic Wire and Cable offers a wide range of heat-shrink coated wires, cables, and components to meet the needs of virtually any application.
The Australia Heat Shrink Tubing Market accounted for $XX Billion in 2023 and is anticipated to reach $XX Billion by 2030, registering a CAGR of XX% from 2024 to 2030.
Raychem heat shrink technology was developed by TE Connectivity for energy purposes. They can assist in optimising the product for applications since heat shrink technology is based on specially designed thermoplastic polymer ingredients.
The goods are recognised for their excellent quality, dependability, and resistance to weathering processes such as pollution and contamination, UV-light, salt fog, and other severe situations.
The outstanding heat shrink products from TE are the foundation of a highly dependable cable accessory product line.
The heat shrink tapes, tubing, wraparound sleeves, splices and terminations will retain their shape memory off the shelf for decades and work robustly in the field following installation due to extensive process controls used during manufacture.
Red2Go owns the Radiform brand and shares the same Directorship of heat shrink production in Australia. Radiform manufactured and exported OEM heat shrink products for CABAC, Narva, and Channel (Telstra).
Radiform were industry pioneers, being the first in the world to create a full line of heat shrink tubing utilizing a reactive compounding technique rather than an electronic beam for polymer crosslinking.
Sl no | Topic |
1 | Market Segmentation |
2 | Scope of the report |
3 | Abbreviations |
4 | Research Methodology |
5 | Executive Summary |
6 | Introduction |
7 | Insights from Industry stakeholders |
8 | Cost breakdown of Product by sub-components and average profit margin |
9 | Disruptive innovation in the Industry |
10 | Technology trends in the Industry |
11 | Consumer trends in the industry |
12 | Recent Production Milestones |
13 | Component Manufacturing in US, EU and China |
14 | COVID-19 impact on overall market |
15 | COVID-19 impact on Production of components |
16 | COVID-19 impact on Point of sale |
17 | Market Segmentation, Dynamics and Forecast by Geography, 2024-2030 |
18 | Market Segmentation, Dynamics and Forecast by Product Type, 2024-2030 |
19 | Market Segmentation, Dynamics and Forecast by Application, 2024-2030 |
20 | Market Segmentation, Dynamics and Forecast by End use, 2024-2030 |
21 | Product installation rate by OEM, 2023 |
22 | Incline/Decline in Average B-2-B selling price in past 5 years |
23 | Competition from substitute products |
24 | Gross margin and average profitability of suppliers |
25 | New product development in past 12 months |
26 | M&A in past 12 months |
27 | Growth strategy of leading players |
28 | Market share of vendors, 2023 |
29 | Company Profiles |
30 | Unmet needs and opportunity for new suppliers |
31 | Conclusion |
32 | Appendix |