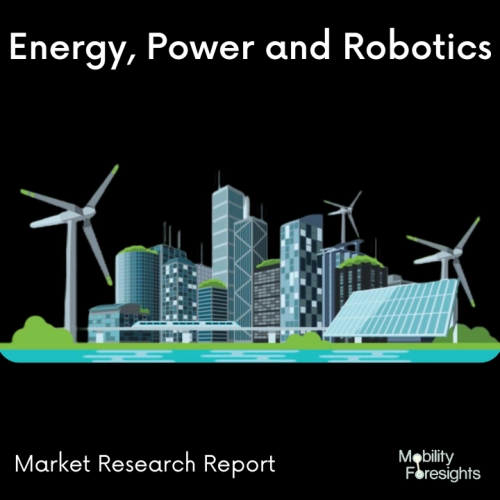
- Get in Touch with Us
Last Updated: Apr 25, 2025 | Study Period: 2023-2030
Automated guided vehicles (AGVs), also known as self-guided or autonomous guided vehicles, are material handling systems or load carriers that move about a warehouse, distribution centre, or manufacturing plant on their own without a driver or operator on board.
AGVs typically employ 2D LiDAR sensors, which are equipped with integrated Laser Guided Vehicle position calculation and are specially built for navigation.
S No | Company Name | Development |
---|---|---|
1 | Pepperl-fuchs | R2000 2-D LiDAR Sensor for Automated Guided Vehicles Safe Positioning. The AGV is equipped with a 2-D LiDAR sensor from the R2000 series, which uses contour navigation to establish the position of the vehicle. The AGV also has an RFID read/write head installed underneath it |
2 | Velodyne | At fulfillment and distribution operations, velodyne lidar solutions advance automation and safety. To enhance the logistical flow of goods, they can be applied to robotics, automated guided vehicles (AGV), and forklifts. With the development of real-time surround vision lidar sensors, |
3 | MAX | Automation's MAX AGV line may be customized to meet the company's demands. Customers can operate and configure AGV systems for upcoming expansion and modifications using the MAX AGV Warehouse Management System (WMS). |
Along with sensor technology,Pepperl+Fuchsalso provides a comprehensive safety concept with supporting documentation, which was created by experts in the field of machine and vehicle safety.
As soon as the read head is directly over an implanted RFID transponder in the floor, the location data is transmitted. Due to the sensor data's redundancy, it is possible to safely estimate the vehicle's position within the facility and turn off other safety measures.
A sensor that is already present on the AGV is used for positioning with the help of the R2000 position data, therefore there are no additional expenses for this sensor.
The 2-D LiDAR sensor's high angular resolution and extremely small light spot ensure maximum precision and, as a result, a precise position assessment.
Reliability is further increased by the use of the RFID technology and its durable transponders because dirt and debris have no impact on measurement outcomes. This all-inclusive solution is provided to the plant operator via a single source:
These safety mechanisms must be turned off in certain places, such as at transfer points, gates, or when entering small rack aisles, as otherwise they will put the AGV in a safe state.
VelodyneLidar ushered in a new era of autonomous technology. An industry pioneer in lidar, Velodyne is renowned for its extensive selection of ground-breaking lidar technology.
For a variety of industries, including robotics, industrial, intelligent infrastructure, autonomous cars, and advanced driver assistance systems (ADAS), Velodyne's ground-breaking sensor and software solutions offer flexibility, quality, and performance.
Velodyne works to advance safer mobility for everyone via ongoing innovation in order to transform lives and communities.
MAXmanufacturers and warehouses are constantly looking for ways to enhance production cycles, boost flexibility, and lower handling, storage, and retrieval costs. MAX is a cutting-edge, trustworthy AGV transport system that utilizes Microsoft technologies and runs in a contemporary client-server Windows environment.
It is simple to configure and offers potential for future extension and adjustments. It is now feasible for clients to alter the AGV track and functions on their own.
With a unique standalone Windows Management System that lets the (the client) edit control of the integrated AGV System, Robotic
AGV models can be tailored to fit the unique requirements and environments of the manufacturing facility, logistics center, warehouse automation, or healthcare operation using a variety of navigational technologies, such as laser guided vehicles (LGV), contour/range-sensing, magnetic and optical, interfacing, and load handling.
Transport, warehousing, load tracking buffering, order swapping, optimal dynamic route selection, location selection, charge control, prioritization, and deadlock prevention are all handled by the system.
The Global Automated guided vehicle(AGV) Lidar market accounted for $XX Billion in 2022 and is anticipated to reach $XX Billion by 2030, registering a CAGR of XX% from 2023 to 2030.
OutdoorScan3 laser scanner for AGVs is introduced by SICK. OutdoorScan3 is a brand-new safety laser scanner being released by SICK. The outdoorScan3 safety laser scanner, according to SICK, is the first one to be approved for use in outdoor applications under IEC 62998.
The outdoorScan3 makes it possible for automated guided vehicles (AGVs) to safely move through outside industrial settings. According to SICK, the outdoorScan3 operates trustworthily and safely in all weather. SICK claims that when exposed to sunlight with an illumination level of up to 40,000 lux, the outdoorScan3 may operate faultlessly.
According to SICK, the outdoorScan3 employs software to remove these ambient variables.As an illustration, rain up to a 10 mm/h precipitation intensity can be filtered away. The outdoorScan3 can detect every obstacle, even in dense fog, with a meteorological visual range of up to 50 m.
Future automation concepts will heavily rely on the AGV, which enables a flexible and effective material movement. These technologies, however, can only be employed in a workplace where there are safety laser scanners present and when there are both machines and humans working there together.
The outdoorScan3 will allow AGV systems to operate outside without any physical barriers and without needing to drastically slow down.
According to SICK, the outdoorScan3 will contribute to the potential for automating and improving the productivity of intralogistics production operations. On boarding bridges for passengers and for securing and guiding AGV systems, the outdoorScan3 is already in use.
Sl no | Topic |
1 | Market Segmentation |
2 | Scope of the report |
3 | Abbreviations |
4 | Research Methodology |
5 | Executive Summary |
6 | Introduction |
7 | Insights from Industry stakeholders |
8 | Cost breakdown of Product by sub-components and average profit margin |
9 | Disruptive innovation in the Industry |
10 | Technology trends in the Industry |
11 | Consumer trends in the industry |
12 | Recent Production Milestones |
13 | Component Manufacturing in US, EU and China |
14 | COVID-19 impact on overall market |
15 | COVID-19 impact on Production of components |
16 | COVID-19 impact on Point of sale |
17 | Market Segmentation, Dynamics and Forecast by Geography, 2023-2030 |
18 | Market Segmentation, Dynamics and Forecast by Product Type, 2023-2030 |
19 | Market Segmentation, Dynamics and Forecast by Application, 2023-2030 |
20 | Market Segmentation, Dynamics and Forecast by End use, 2023-2030 |
21 | Product installation rate by OEM, 2023 |
22 | Incline/Decline in Average B-2-B selling price in past 5 years |
23 | Competition from substitute products |
24 | Gross margin and average profitability of suppliers |
25 | New product development in past 12 months |
26 | M&A in past 12 months |
27 | Growth strategy of leading players |
28 | Market share of vendors, 2023 |
29 | Company Profiles |
30 | Unmet needs and opportunity for new suppliers |
31 | Conclusion |
32 | Appendix |