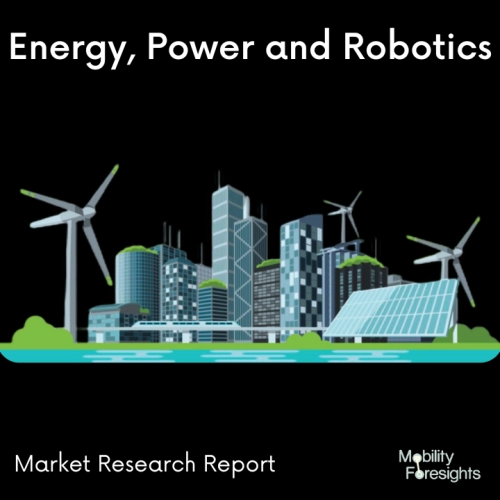
- Get in Touch with Us
Last Updated: Apr 25, 2025 | Study Period: 2023-2030
Collision avoidance is available for AMRs and AGVs alike. Their safety system will, at the very least, detect any obstruction and safely slow down or stop the robot before an accident takes place.
However, the capabilities of AGVs often end here. On the other hand, AMRs have the ability to avoid obstacles. The robot can reroute and carry out its duty like a human would, in addition to being able to avoid crashes.
Obstacle avoidance is essential in a dynamic warehouse setting. AGVs must be monitored more regularly if they just have basic collision avoidance.
Any obstruction will require a person to move it, such as trashed packaging or another vehicle. These frequent interruptions take up workers' time and frequently waste labour resources that may be employed in other ways. This degree of contact largely defeats the original intent of integrating warehouse robots.
AMRs are far more capable of achieving total autonomy. They can solve issues on their own and consistently bring value because they don't impede other workflows.
All mobile robots possess what are known as safety fields, or speed-restricted zones, in addition to the capacity to recognise an obstruction and prevent collision.
Robots are designed to slow down or halt in these places and wait a predetermined amount of time before continuing their work. During the mapping phase, AGV vendors programme these locations into the robots.
The Global Automated guided vehicle(AGV) obstacle avoidance system market accounted for $XX Billion in 2022 and is anticipated to reach $XX Billion by 2030, registering a CAGR of XX% from 2023 to 2030.
Assysta System Solutions Material-moving automated guided vehicles (AGVs) typically follow a two-way street. More particular, they operate along well-known paths close to workers in single or multiple opposing-direction lanes.
AGV manufacturers were surveyed, and numerous said that this is the best setup for secure AGV operation. However, when an AGV stops for an obstruction in its route, it sequentially halts the flow of subsequent AGVs until the obstruction is cleared by an AGV supervisor.
Obstacle detection and avoidance (ODA) is a concept that is well-known among mobile robot researchers but less well-known among AGV researchers. In our study, we came across two films of AGV manufacturers showcasing how their vehicles can identify and avoid obstacles.
These involve a floor cleaning vehicle and a unit load vehicle. Additional investigation turned out another manufacturer of floor cleaning robots that offered a comparable capability.
Sl no | Topic |
1 | Market Segmentation |
2 | Scope of the report |
3 | Abbreviations |
4 | Research Methodology |
5 | Executive Summary |
6 | Introduction |
7 | Insights from Industry stakeholders |
8 | Cost breakdown of Product by sub-components and average profit margin |
9 | Disruptive innovation in the Industry |
10 | Technology trends in the Industry |
11 | Consumer trends in the industry |
12 | Recent Production Milestones |
13 | Component Manufacturing in US, EU and China |
14 | COVID-19 impact on overall market |
15 | COVID-19 impact on Production of components |
16 | COVID-19 impact on Point of sale |
17 | Market Segmentation, Dynamics and Forecast by Geography, 2023-2030 |
18 | Market Segmentation, Dynamics and Forecast by Product Type, 2023-2030 |
19 | Market Segmentation, Dynamics and Forecast by Application, 2023-2030 |
20 | Market Segmentation, Dynamics and Forecast by End use, 2023-2030 |
21 | Product installation rate by OEM, 2023 |
22 | Incline/Decline in Average B-2-B selling price in past 5 years |
23 | Competition from substitute products |
24 | Gross margin and average profitability of suppliers |
25 | New product development in past 12 months |
26 | M&A in past 12 months |
27 | Growth strategy of leading players |
28 | Market share of vendors, 2023 |
29 | Company Profiles |
30 | Unmet needs and opportunity for new suppliers |
31 | Conclusion |
32 | Appendix |