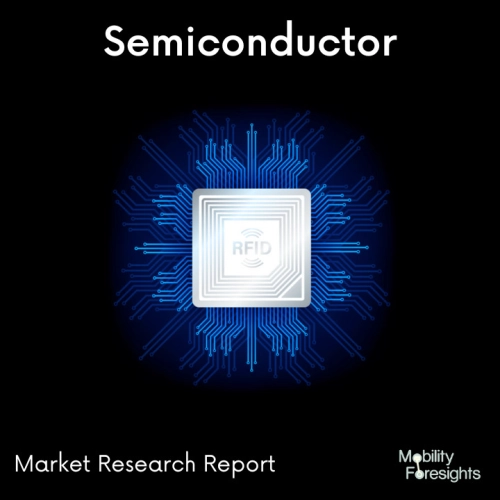
- Get in Touch with Us
Last Updated: Apr 25, 2025 | Study Period: 2023-2030
In the production of semiconductors, a mask aligner is a precision machine tool that transfers micro- and nanoscale designs onto a wafer or substrate. By placing the pattern (photomask) to be printed between a light source and the substrate to be patterned, the patterns (structure) are formed using a shadow transfer technique (wafer).
A photosensitive substance (photoresist) is initially applied to the substrate being patterned; this substance then responds to the light emitted from the shadow image. Then, employing particular chemicals, the resulting pattern is created.
The production of semiconductor devices, including transistors, sensors, and medical components, among others, is made possible by mask aligners.
An essential component of the photolithography procedure is a mask aligner, which works in tandem with a technique for evenly coating the substrate with a photoresist.
Both the coated substrate and the photomask holding the required pattern are properly aligned with the aid of a mask aligner before the coated substrate is exposed to light and the intended pattern is transferred to it.
The automated mask alignment system must be precision manufactured equipment in order to facilitate this complicated process and generate structures with features as small as 250nm. Due to the small size of these structures, the wavelength of the light employed also affects the final feature size.
If a mask aligner does not have a high-quality light source, it will not be able to controllably expose a substrate to light. Historically, this has been a broad-spectrum mercury bulb that emits light (see the figure under "Emission Spectrum of a Typical Mercury Lamp").
Mask aligner light sources are frequently referred to be UV light sources since the bulb also transmits in this region, even though two wavelengths (100-400nm) fall outside the precise UV spectrum.
GLOBAL AUTOMATED MASK ALIGNMENT SYSTEM MARKET SIZE AND FORECAST
The Global Automated Mask Alignment System market accounted for $XX Billion in 2022 and is anticipated to reach $XX Billion by 2030, registering a CAGR of XX% from 2023 to 2030.
The EVG620HBL Gen II is the second generation fully automated mask alignment system for volume manufacturing of high-brightness light-emitting diodes, according to EV Group (EVG), a leading provider of wafer-bonding and lithography equipment for the advanced semiconductor and packaging, compound semiconductors, MEMS, silicon-on-insulator (SOI), and emerging nanotechnology markets (HB-LEDs).
One year after the first-generation EVG620HBL was introduced, the Gen II offers a tool platform designed to meet the unique needs of HB-LED customers and the continuous desire for total cost-of-ownership reduction.
In comparison to competing products, the EVG620HBL Gen II optimizes tool footprint in the fab and produces 55 percent more wafers per square meter of the cleanroom.
Sl no | Topic |
1 | Market Segmentation |
2 | Scope of the report |
3 | Abbreviations |
4 | Research Methodology |
5 | Executive Summary |
6 | Introduction |
7 | Insights from Industry stakeholders |
8 | Cost breakdown of Product by sub-components and average profit margin |
9 | Disruptive innovation in the Industry |
10 | Technology trends in the Industry |
11 | Consumer trends in the industry |
12 | Recent Production Milestones |
13 | Component Manufacturing in US, EU and China |
14 | COVID-19 impact on overall market |
15 | COVID-19 impact on Production of components |
16 | COVID-19 impact on Point of sale |
17 | Market Segmentation, Dynamics and Forecast by Geography, 2023-2030 |
18 | Market Segmentation, Dynamics and Forecast by Product Type, 2023-2030 |
19 | Market Segmentation, Dynamics and Forecast by Application, 2023-2030 |
20 | Market Segmentation, Dynamics and Forecast by End use, 2023-2030 |
21 | Product installation rate by OEM, 2023 |
22 | Incline/Decline in Average B-2-B selling price in past 5 years |
23 | Competition from substitute products |
24 | Gross margin and average profitability of suppliers |
25 | New product development in past 12 months |
26 | M&A in past 12 months |
27 | Growth strategy of leading players |
28 | Market share of vendors, 2023 |
29 | Company Profiles |
30 | Unmet needs and opportunity for new suppliers |
31 | Conclusion |
32 | Appendix |