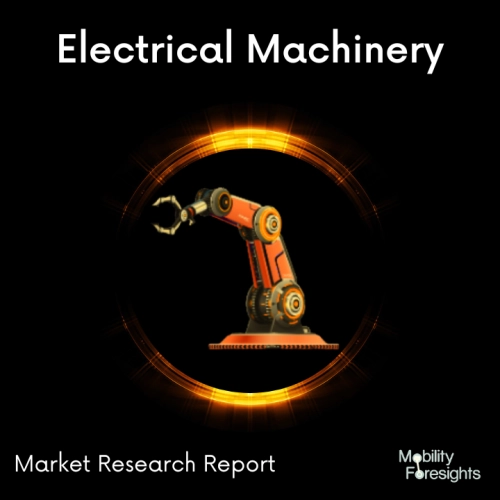
- Get in Touch with Us
Last Updated: Apr 25, 2025 | Study Period: 2024-2030
Electric press brake with automation. This modular system will enable you to set up your completely automated bending cell.
In order to deliver a comprehensive solution, designs and develops each component of the system, from the machine to its connection with the robot to the software that controls the manufacturing process.
Electric press brakes apply pressure using two servo motors that are synced together and transfer power via a specialised belt and pulley system.
Servo motors coil the belt to the main pulley and apply the bending force during the downward movement of the upper beam.
The springs on either side of the machine provide the mechanical return force for the machine. The upper beam is pushed to the programme TDC position by springs after the servo motors begin to decoil the belt after bending.
Global automatic electric press brake market accounted for $XX Billion in 2022 and is anticipated to reach $XX Billion by 2030, registering a CAGR of XX% from 2024 to 2030.
The BB306 new ball screw press brake from MC Machinery Systems was just unveiled at FABTECH 2019. With a more compact design, this fully electric press brake can fit into any space and create smaller pieces.
The new machines offer all the typical features that customers have grown to value and anticipate from MC Machinery, such as an integrated all-axis pulse handle, thickness detection, multi-axis rear gauge, front & back LED lighting, and the biggest, most user-friendly control on the market.
The BB306 also has 100% Mitsubishi electronics, motors, and servo drives with an AC Servo motor and ball screw drive mechanism for high speed productivity and repeatability, in addition to the new MOS control featured on the BB & BH series.
The machine's design, which incorporates a foldable front table, a 5-axis back gauge, and an operator-adjustable tilting controller, is intended to support workers ergonomically whether they are standing or sitting.
Integrated all-axis pulse handling, thickness detection, a multi-axis back gauge, and front and rear LED lighting are among the features.
For high speed productivity and reproducibility, an AC servo motor and ball screw drive mechanism are included.
It includes tilting, a five-axis back gauge, and a folding front table that supports users in either a standing or sitting posture.
Sl no | Topic |
1 | Market Segmentation |
2 | Scope of the report |
3 | Abbreviations |
4 | Research Methodology |
5 | Executive Summary |
6 | Introduction |
7 | Insights from Industry stakeholders |
8 | Cost breakdown of Product by sub-components and average profit margin |
9 | Disruptive innovation in the Industry |
10 | Technology trends in the Industry |
11 | Consumer trends in the industry |
12 | Recent Production Milestones |
13 | Component Manufacturing in US, EU and China |
14 | COVID-19 impact on overall market |
15 | COVID-19 impact on Production of components |
16 | COVID-19 impact on Point of sale |
17 | Market Segmentation, Dynamics and Forecast by Geography, 2024-2030 |
18 | Market Segmentation, Dynamics and Forecast by Product Type, 2024-2030 |
19 | Market Segmentation, Dynamics and Forecast by Application, 2024-2030 |
20 | Market Segmentation, Dynamics and Forecast by End use, 2024-2030 |
21 | Product installation rate by OEM, 2023 |
22 | Incline/Decline in Average B-2-B selling price in past 5 years |
23 | Competition from substitute products |
24 | Gross margin and average profitability of suppliers |
25 | New product development in past 12 months |
26 | M&A in past 12 months |
27 | Growth strategy of leading players |
28 | Market share of vendors, 2023 |
29 | Company Profiles |
30 | Unmet needs and opportunity for new suppliers |
31 | Conclusion |
32 | Appendix |