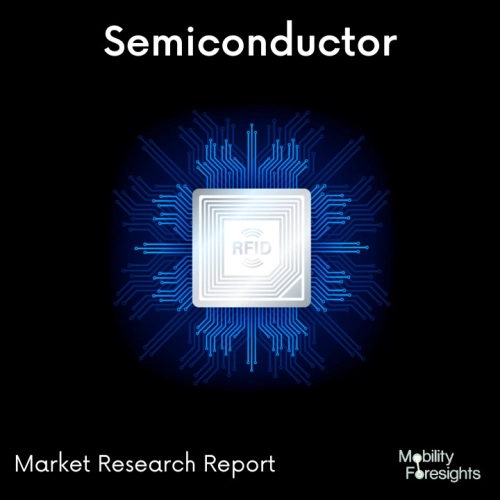
- Get in Touch with Us
Last Updated: Apr 25, 2025 | Study Period: 2023-2030
There is no direct tool-to-workpiece contact when using a laser to groove; the operation relies on thermal energy. It transfers thermal energy to the wafer using a concentrated high-intensity laser, which is then absorbed by the uppermost ILD metal layers with low thermal conductivity.
The solids from these molten and vaporised molten metal layers can subsequently be removed by applying directional air pressure flow. By combining conventional blade dicing and laser grooving techniques to separate individual chips from the silicon wafer, manufacturers may now enhance die separation quality thanks to advancements in laser grooving.
The Global Automatic Laser Grooving Machine market accounted for $XX Billion in 2022 and is anticipated to reach $XX Billion by 2030, registering a CAGR of XX% from 2023 to 2030.
Clemex has developed a brand-new technique for automating the measurement of the separation between the laser groove and the edge of the die. Therefore, laser grooving has emerged as the top option for producers aiming to enhance wafer dicing quality.
But there are also problems with this method as well. To ensure that it grooves along the proper location on the wafer, the sophisticated laser system must be precisely positioned and adjusted over the wafer.
The groove itself must meet the manufacturer's tolerance and shape requirements with exceptional precision. A die cut that was made poorly and was therefore unusable due to a groove that did not conform to this tolerance must be thrown away.An operator using a microscope must spend a considerable amount of time examining the grooves' tolerances in order to prepare them for dicing.
In order to manually move around the wafer and visually evaluate the tolerance, chip manufacturers currently use human operators. There hasn't been an alternative up until now, despite the fact that it takes an absurdly long time and is prone to human error.
Manufacturers can now automate their examination of laser grooving placement on a silicon wafer thanks to the procedure detailed here, which makes use of the outstanding suite of capabilities provided by the Vision PE system.
Sl no | Topic |
1 | Market Segmentation |
2 | Scope of the report |
3 | Abbreviations |
4 | Research Methodology |
5 | Executive Summary |
6 | Introduction |
7 | Insights from Industry stakeholders |
8 | Cost breakdown of Product by sub-components and average profit margin |
9 | Disruptive innovation in the Industry |
10 | Technology trends in the Industry |
11 | Consumer trends in the industry |
12 | Recent Production Milestones |
13 | Component Manufacturing in US, EU and China |
14 | COVID-19 impact on overall market |
15 | COVID-19 impact on Production of components |
16 | COVID-19 impact on Point of sale |
17 | Market Segmentation, Dynamics and Forecast by Geography, 2023-2030 |
18 | Market Segmentation, Dynamics and Forecast by Product Type, 2023-2030 |
19 | Market Segmentation, Dynamics and Forecast by Application, 2023-2030 |
20 | Market Segmentation, Dynamics and Forecast by End use, 2023-2030 |
21 | Product installation rate by OEM, 2023 |
22 | Incline/Decline in Average B-2-B selling price in past 5 years |
23 | Competition from substitute products |
24 | Gross margin and average profitability of suppliers |
25 | New product development in past 12 months |
26 | M&A in past 12 months |
27 | Growth strategy of leading players |
28 | Market share of vendors, 2023 |
29 | Company Profiles |
30 | Unmet needs and opportunity for new suppliers |
31 | Conclusion |
32 | Appendix |