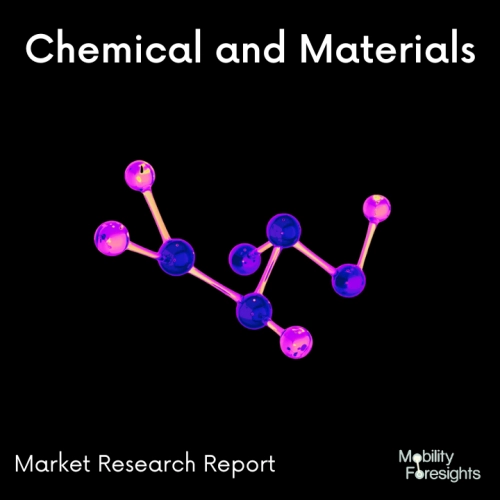
- Get in Touch with Us
Last Updated: Apr 25, 2025 | Study Period: 2024-2030
Semi-crystalline thermoplastic resins that can withstand heat include partially aromatic polyamides. They are partly automotive aromatic polyamide resins generated by condensation of aliphatic amides, such as caprolactam and hexametylene diamine, with terephthalic acid and/or isophthalic acid.
Polyphthalamide refers to resins in which terephthalic acid and/or isophthalic acid residues make up at least 55 molar percent of the repeat units (PPA).
The polymer's aromatic component minimises moisture absorption while raising the melting point, stiffness, thermal stability, and chemical resistance.
Because moisture absorption significantly impacts the mechanical and electrical properties of polyamides, the substantially reduced water absorption results in little dimensional changes, which in turn leads in much more stable qualities.
In many cases, automotive aromatic polyamides resins are more affordable than completely aromatic aramids, which are more expensive.
Automotive, aeronautical, electrical, and industrial parts that have to survive extended exposure to severe chemicals and/or high temperatures are common uses.
This comprises motor parts, fuel line connectors, coolant pumps, bushings, aircraft engine bearing pads, charge air coolers, resonators, engine cover parts, heat shields, fuel cutoff and water heater manifold valves, connectors, high voltage bushings, motor housings, and head light parts.
Global automotive aromatic polyamide resin market accounted for $XX Billion in 2022 and is anticipated to reach $XX Billion by 2030, registering a CAGR of XX% from 2024 to 2030.
With the recent introduction of two new items, Polyram has increased the variety of materials offered in its Polytron family of goods.
The first development focuses on low emission (LE) materials that are particularly well suited for usage in automobile sector elements created for the driver's environment.
The second advancement focuses on a substance in which the primary polymer is semi-aromatic Polyamide (PA9T).One of Polyram's three primary product families is Polytron.
Production is carried out in specialised settings and necessitates the use of specialised knowledge and methods.Continuously fed into a predetermined die, the glass fibres are implanted in the resin matrix.
These materials' output pellet lengths can be 12 mm or longer and are determined by the length of the glass fibres they include.
DuPont created the Kevlar brand of aromatic polyamide fiber, which is well-known and often used. Kevlar has many uses in a variety of industries thanks to its remarkable strength and distinctive characteristics.
While employed at the DuPont Experimental Station in the early 1960s, a chemist by the name of Stephanie Kwolek created the initial version of Kevlar.
Her objective was to create a fiber that was both robust and lightweight for use in car tires. She used a synthetic aromatic polyamide polymer to make a liquid crystalline solution for her studies. Kevlar was created by spinning this solution into fibers.
Long-chain aromatic polyamides, or "kevlar," are made up of alternating units of amide (-CONH-) and aromatic rings. The unique configuration of these chemical groups is what gives Kevlar its exceptional characteristics.
The fiber's exceptional tensile strength is a result of the many chains that make up its structure being kept together by potent intermolecular forces.
There are various processes in the Kevlar manufacturing process. The polymer is first created by reacting monomers in a suitable solvent, commonly p-phenylenediamine and terephthaloyl chloride. This produces a spinning dope, a liquid crystalline solution.
The liquid is then shaped into continuous threads by extruding the spinning dope through spinnerets, which are tiny pores.
A coagulation bath solidifies the fibers as they come out of the spinnerets. The fibers are stretched and heated after solidification to improve their mechanical qualities even more.
The extraordinary strength of Kevlar is one of its most noticeable characteristics. One of the strongest commercially available fibers, it is five times stronger than steel on a same weight basis.
Kevlar's tight molecular structure and potent intermolecular interactions are credited with contributing to its great tensile strength.
Kevlar is the perfect material for applications needing endurance and structural integrity because of its strength, which enables it to bear tremendous forces and resist deformation.
In addition to strength, Kevlar possesses additional beneficial qualities. It is extremely robust and suited for demanding applications because of its great resistance to impact, abrasion, and chemicals.
Kevlar is an appealing option for applications where weight reduction is essential because it is very lightweight and has a density that is substantially lower than that of metals.
Kevlar's high melting point also makes it possible for it to maintain structural integrity even at high temperatures.
Kevlar is widely used in many industries due to its excellent qualities. The use of Kevlar in ballistic protection, such as bulletproof vests and helmets, is one of its most well-known uses.
The fiber is a useful material for projectile protection because of its great strength and resistance to penetration.
Aerospace companies also use Kevlar in their products. It is used to build parts for aircraft and spacecraft in order to increase their strength while lowering their weight.
Wings, fuselage panels, and fairings are among the components made with kevlar-based composites, which enhance overall performance and fuel economy.
Another significant application of Kevlar is in the automotive sector. It is employed in the production of tires, belts, hoses, and other components that require high strength and resistance to wear.
Kevlar-reinforced tires, for example, exhibit enhanced durability and resistance to punctures, providing increased safety on the roads.
Beyond these industries, Kevlar finds use in numerous other applications. It is utilized in the construction sector for reinforcement in concrete structures, providing improved strength and resistance to cracking.
Kevlar-based ropes and cables are employed in maritime operations and heavy lifting due to their high strength-to-weight ratio.
Kevlar also finds applications in sports equipment, such as tennis racquets, bicycles, and canoes, where its strength and lightweight properties are advantageous.
Sl no | Topic |
1 | Market Segmentation |
2 | Scope of the report |
3 | Abbreviations |
4 | Research Methodology |
5 | Executive Summary |
6 | Introduction |
7 | Insights from Industry stakeholders |
8 | Cost breakdown of Product by sub-components and average profit margin |
9 | Disruptive innovation in the Industry |
10 | Technology trends in the Industry |
11 | Consumer trends in the industry |
12 | Recent Production Milestones |
13 | Component Manufacturing in US, EU and China |
14 | COVID-19 impact on overall market |
15 | COVID-19 impact on Production of components |
16 | COVID-19 impact on Point of sale |
17 | Market Segmentation, Dynamics and Forecast by Geography, 2023-2030 |
18 | Market Segmentation, Dynamics and Forecast by Product Type, 2023-2030 |
19 | Market Segmentation, Dynamics and Forecast by Application, 2023-2030 |
20 | Market Segmentation, Dynamics and Forecast by End use, 2023-2030 |
21 | Product installation rate by OEM, 2023 |
22 | Incline/Decline in Average B-2-B selling price in past 5 years |
23 | Competition from substitute products |
24 | Gross margin and average profitability of suppliers |
25 | New product development in past 12 months |
26 | M&A in past 12 months |
27 | Growth strategy of leading players |
28 | Market share of vendors, 2023 |
29 | Company Profiles |
30 | Unmet needs and opportunity for new suppliers |
31 | Conclusion |
32 | Appendix |