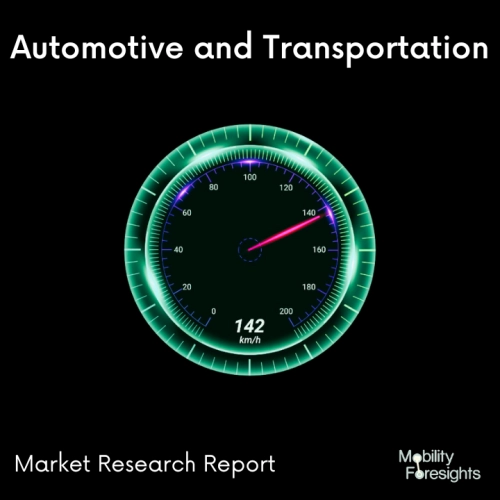
- Get in Touch with Us
Last Updated: Apr 25, 2025 | Study Period: 2023-2030
The "body in white" phase of automobile design is when the final car body shapes are established in anticipation of the purchase of the pricey production stamping die. Before integrating the suspension and engine, the car's shell structure was initially painted white. It is left white so that the consumer has a colour choice.
The welded sheet metal construction is still referred to by the same nomenclature today. The term "body-in-white" (BiW) refers to the sheet of a car's body after all of its parts, with the exception of any moving parts (such as hoods, fenders, etc.), trimmings (such as glass, seats, etc.), or chassis subassemblies, have been welded together.
The Global Automotive Body In White Laser Welding Machine market accounted for $XX Billion in 2022 and is anticipated to reach $XX Billion by 2030, registering a CAGR of XX% from 2023 to 2030.
With around 15% of all industrial processing lasers already placed in production, the usage of lasers in the automotive industry has grown significantly in recent years.
Despite the fact that lasers are mostly used for cutting applications, welding is using a sizable and increasing amount of lasers. Since then, body-in-white welding and customised blank manufacturing have seen explosive growth in welding applications, notably among steel manufacturers.
The use of laser welding of sheet assemblies in place of resistance spot welding is expanding, and one of the most popular uses is joining the roof to the side panel. [5,6] With periodic three layer thicknesses to be welded, this component typically consists of a two layer lap joint in zinc coated steel spanning lengths of 2.5 to 3 metres.
The presence of the zinc coating at the interface between the sheets, where the low evaporation temperature of the zinc (906°C), can cause issues with weld consistency due to the formation of blowholes and porosity, if the sheets are tightly clamped together, is one of the main challenges for laser welding of these types of joints.
Laser welding is additionally utilised to create partial penetration welds, such as the hem flanges that are frequently employed in doors, bonnets, boot lids, and other closures.
Although steel sheet has been the subject of the majority of the work, there have been other programmes on aluminium alloys. Due to the material's high reflectivity and thermal conductivity, low viscosity of liquid aluminium, propensity for cracking, and porosity in some alloys, laser welding of aluminium alloys is more challenging than laser welding of steel.
Sl no | Topic |
1 | Market Segmentation |
2 | Scope of the report |
3 | Abbreviations |
4 | Research Methodology |
5 | Executive Summary |
6 | Introduction |
7 | Insights from Industry stakeholders |
8 | Cost breakdown of Product by sub-components and average profit margin |
9 | Disruptive innovation in the Industry |
10 | Technology trends in the Industry |
11 | Consumer trends in the industry |
12 | Recent Production Milestones |
13 | Component Manufacturing in US, EU and China |
14 | COVID-19 impact on overall market |
15 | COVID-19 impact on Production of components |
16 | COVID-19 impact on Point of sale |
17 | Market Segmentation, Dynamics and Forecast by Geography, 2023-2030 |
18 | Market Segmentation, Dynamics and Forecast by Product Type, 2023-2030 |
19 | Market Segmentation, Dynamics and Forecast by Application, 2023-2030 |
20 | Market Segmentation, Dynamics and Forecast by End use, 2023-2030 |
21 | Product installation rate by OEM, 2023 |
22 | Incline/Decline in Average B-2-B selling price in past 5 years |
23 | Competition from substitute products |
24 | Gross margin and average profitability of suppliers |
25 | New product development in past 12 months |
26 | M&A in past 12 months |
27 | Growth strategy of leading players |
28 | Market share of vendors, 2023 |
29 | Company Profiles |
30 | Unmet needs and opportunity for new suppliers |
31 | Conclusion |
32 | Appendix |