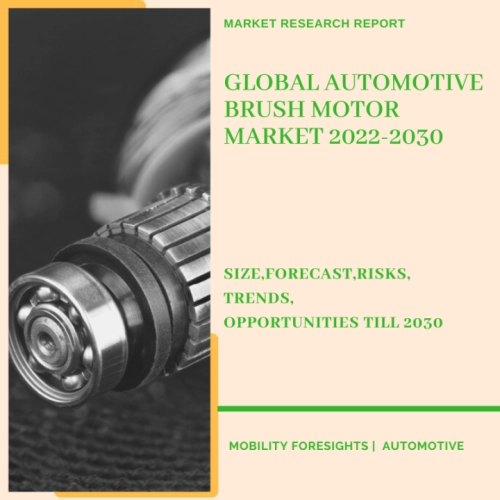
- Get in Touch with Us
Last Updated: Apr 25, 2025 | Study Period: 2022-2030
In brushed DC motors, the stator has magnets that are encircled by coiled coils in the rotor. The commutator is attached to a coil's two ends. For as long as the brushes and commutator are in contact, direct current electric power will flow via the brushes and coil. The commutator in turn links to electrodes called brushes.
But when the coil turns, it comes to a point where the brushes and commutator are no longer in touch, cutting off the coil's current flow. Despite this, the coil keeps spinning due to its momentum. This restores the current, which is now flowing through a separate coil, by bringing the brushes and commutator back into contact.
The Global automotive Brush Motor market accounted for $XX Billion in 2021 and is anticipated to reach $XX Billion by 2030, registering a CAGR of XX% from 2022 to 2030.
"TB9057FG," a brushed motor pre-driver upgraded to achieve functional safety and for use in electric power steering systems, was introduced by Toshiba Corporation.
A pre-driver circuit, a motor current detection circuit, a motor direction detection circuit, and various failure detection circuits are integrated into the new integrated circuit (IC), while redundant functions for the motor current detection circuit, power supply PIN, and GND PIN are created to ensure higher functional safety.
Toshiba will also give clients documentation to enable safety analysis and design. Toshiba has also performed a variety of functional safety evaluations to simulate possible system failures.More and more vehicle technologies that are crucial for safety, like EPS, must comply with ASIL-D standards.
A strong motor platform for vehicle electric power steering was just introduced by Johnson Electric. Through cutting-edge brush motor technology, this EPS series motor platform offers the highest steering power and lowest cogging torque in the industry. In comparison to current brush motor technology, it provides 20% more steering power and 10% less cogging torque.
To increase fuel efficiency, the motor weight has been lowered by 10%. The EPS series brush motor platform from Johnson Electric uses cutting-edge design elements to produce the highest steering power available in the market while maintaining low cogging torque that is equivalent to brushless EPS motor technology.
STMicroelectronics has expanded its line of tiny, low-voltage, energy-efficient drivers for battery-operated portable and wearable applications with the STSPIN250 single-chip 2.6A driver for brushed DC motors.
Small 2.6A Brushed DC Motor Driver for Portable IoT Devices is Released by STMicroelectronics.
To conserve space in portable equipment, the driver incorporates a full power-MOSFET bridge and fixed off-time PWM current controller. The power stage's low on-resistance (200m total, high-side + low-side) and best-in-class, low-current sleep mode (below 80nA) extend battery life and lower equipment-case temperatures.
Design professionals can specify a power source as small as a single Li-ion cell thanks to its supply-voltage range of 10V to 1.8V.
Sl no | Topic |
1 | Market Segmentation |
2 | Scope of the report |
3 | Abbreviations |
4 | Research Methodology |
5 | Executive Summary |
6 | Introduction |
7 | Insights from Industry stakeholders |
8 | Cost breakdown of Product by sub-components and average profit margin |
9 | Disruptive innovation in the Industry |
10 | Technology trends in the Industry |
11 | Consumer trends in the industry |
12 | Recent Production Milestones |
13 | Component Manufacturing in US, EU and China |
14 | COVID-19 impact on overall market |
15 | COVID-19 impact on Production of components |
16 | COVID-19 impact on Point of sale |
17 | Market Segmentation, Dynamics and Forecast by Geography, 2022-2030 |
18 | Market Segmentation, Dynamics and Forecast by Product Type, 2022-2030 |
19 | Market Segmentation, Dynamics and Forecast by Application, 2022-2030 |
20 | Market Segmentation, Dynamics and Forecast by End use, 2022-2030 |
21 | Product installation rate by OEM, 2022 |
22 | Incline/Decline in Average B-2-B selling price in past 5 years |
23 | Competition from substitute products |
24 | Gross margin and average profitability of suppliers |
25 | New product development in past 12 months |
26 | M&A in past 12 months |
27 | Growth strategy of leading players |
28 | Market share of vendors, 2022 |
29 | Company Profiles |
30 | Unmet needs and opportunity for new suppliers |
31 | Conclusion |
32 | Appendix |