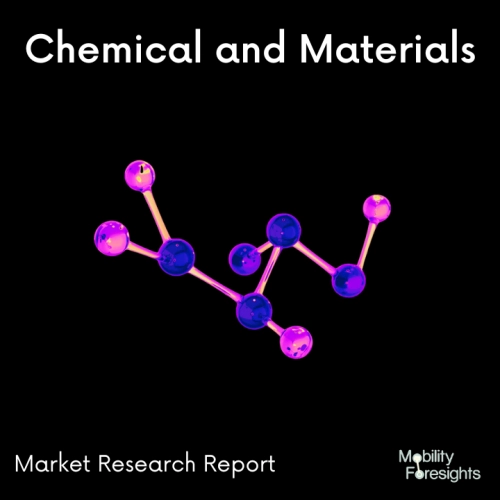
- Get in Touch with Us
Last Updated: Apr 25, 2025 | Study Period: 2024-2030
Statistics show that more than half of car seats are made of textile textiles, with leather only appearing on certain high-end vehicles.
Along with a wide range of colours and patterns, automobile seat fabric also needs to have superior physical qualities.
The earliest raw material for car seat fabric was polyamide fibre. The primary raw material for car seat fabric is polyester fibre.
The polyester fabric has a number of mechanical qualities, including good heat resistance, good dimensional stability, good handle, and comfort.
It also has good wear resistance, pilling resistance, ageing resistance, and other features. Fibre content, fabric width variation, square metre weight tolerance, weaves, fabric count, static dimensional change, breaking strength, wear resistance, anti pilling, air and moisture permeability, and other indicators are all used to describe the interior quality of automotive seat fabrics.
Automobile carpets, seating fabrics, side, roof, floor, and door panels, safety belts, tires, airbags, fuel filters, insulation materials, and other components are all made in major part from textile materials.
While most of these materials are derived from synthetic fibres, polyester (also known as polyethylene terephthalate [PET]) is the most common fibre used to make vehicle textiles.
This chapter discusses how polyester fibre is used in automotive applications in a variety of ways, including as a component of composite constructions and in knitted, woven, and nonwoven textile structures. It also covers the fibre's fundamental characteristics and performance characteristics.
The Global Automotive car seat Polyester Fibre market accountedfor $XX Billion in 2023 and is anticipated to reach $XX Billion by 2030, registering a CAGR of XX% from 2024 to 2030.
In the meantime, as manufacturers look for additional ways to lighten vehicles to cut emissions and improve fuel efficiency, as well as rising demand for increased comfort and improved safety, the amount of textiles used in new vehicles continues to rise.
By adopting textile and composite underbodies in place of metal ones, the use of textile materials has expanded from 20 kg in a mid-size automobile in 2000 to 35 kg (about 45 m2 in terms of surface area) today.
Later models used a variety of natural fibre materials, including flat woven wool, cotton broadcloth, and woven mohair pile textiles; natural leather as vehicles got more complex, imitating horse-drawn carriages with passenger and subsequently driver compartments.
Artificial intelligence, virtual and augmented reality, developments in fuel cells and batteries, the Internet of Things, sensors, and digital technologies are examples of disruptive technologies.
Car sharing in urban areas, end-of-life recycling, sustainability, and the necessity for lightweight materials due to increasingly strict carbon dioxide (CO2) emission standards for new vehicles are some major themes that will have an impact on the automotive industry.
Automotive textiles cover a wide range of items, including filters, tire cables, passive safety, and headliners in addition to upholstery, flooring, and headliners.
The majority of material is used for interior trim, including seat covers, carpets, headliners, and door panels. The remaining portion is utilised to reinforce tires, belts, hoses, seatbelts, and airbags, as well as for filters and insulation.
Sl no | Topic |
1 | Market Segmentation |
2 | Scope of the report |
3 | Abbreviations |
4 | Research Methodology |
5 | Executive Summary |
6 | Introduction |
7 | Insights from Industry stakeholders |
8 | Cost breakdown of Product by sub-components and average profit margin |
9 | Disruptive innovation in the Industry |
10 | Technology trends in the Industry |
11 | Consumer trends in the industry |
12 | Recent Production Milestones |
13 | Component Manufacturing in US, EU and China |
14 | COVID-19 impact on overall market |
15 | COVID-19 impact on Production of components |
16 | COVID-19 impact on Point of sale |
17 | Market Segmentation, Dynamics and Forecast by Geography, 2024-2030 |
18 | Market Segmentation, Dynamics and Forecast by Product Type, 2024-2030 |
19 | Market Segmentation, Dynamics and Forecast by Application, 2024-2030 |
20 | Market Segmentation, Dynamics and Forecast by End use, 2024-2030 |
21 | Product installation rate by OEM, 2023 |
22 | Incline/Decline in Average B-2-B selling price in past 5 years |
23 | Competition from substitute products |
24 | Gross margin and average profitability of suppliers |
25 | New product development in past 12 months |
26 | M&A in past 12 months |
27 | Growth strategy of leading players |
28 | Market share of vendors, 2023 |
29 | Company Profiles |
30 | Unmet needs and opportunity for new suppliers |
31 | Conclusion |
32 | Appendix |