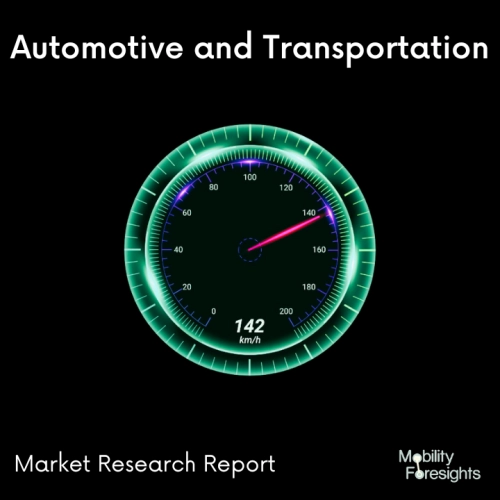
- Get in Touch with Us
Last Updated: Apr 25, 2025 | Study Period: 2023-2030
The automotive composite bonding adhesive a continuous bond line and a cohesive joining of surfaces, which increases the vehicle's durability and extends its lifespan while also maintaining the structural integrity of the substrates.
Fast handling strength can be achieved through the use of heat-accelerated curing technologies. A variety of materials are used to make composite adhesives. Film, foam, hot melt, paste, pellets, solvent-based, and water-based are all possible forms of these materials.
Contact, pressure-sensitive, thermosetting, hot melt, and reactive hot melt are all types of adhesives. When two surfaces are joined together, adhesive bonding typically results in a smooth bond.
By curing the bonding agent with heat and pressure, this method of joining makes use of glues, epoxies, or a variety of plastic agents.
As a result, processing times can be cut down by quickly moving bonded parts to the next stage of the assembly line.
Additionally, the adhesives' one-minute cycle time makes them ideal for mass production of automobiles. The application-specific open time can be changed. Large parts can be bonded with the long open time.
The Global automotive composite bonding adhesive market accounted for $XX Billion in 2022 and is anticipated to reach $XX Billion by 2030, registering a CAGR of XX% from 2023 to 2030.
This company offers a brand-new adhesive for bonding composites in automobiles. According to reports, BETAFORCE composite bonding adhesives are made to support hybrid constructions like lightweight solutions.
A variety of materials are used to make composite adhesives.The application-specific open time can be changed. Large parts can be bonded with the long open time.
One of the most promising ways to reduce weight without sacrificing safety or comfort is through the use of multi-material vehicles. According to reports, the proportion of carbon fiber composites in the material mix is currently increasing.
Structural adhesives are advantageous from a production standpoint because they can provide processing benefits in addition to weight reduction.
Pre-treatment-free carbon fiber joining, optimized open times, and balanced mechanical properties regarding optimal stiffness and driving properties are among the benefits of production.
Sl no | Topic |
1 | Market Segmentation |
2 | Scope of the report |
3 | Abbreviations |
4 | Research Methodology |
5 | Executive Summary |
6 | Introduction |
7 | Insights from Industry stakeholders |
8 | Cost breakdown of Product by sub-components and average profit margin |
9 | Disruptive innovation in the Industry |
10 | Technology trends in the Industry |
11 | Consumer trends in the industry |
12 | Recent Production Milestones |
13 | Component Manufacturing in US, EU and China |
14 | COVID-19 impact on overall market |
15 | COVID-19 impact on Production of components |
16 | COVID-19 impact on Point of sale |
17 | Market Segmentation, Dynamics and Forecast by Geography, 2023-2030 |
18 | Market Segmentation, Dynamics and Forecast by Product Type, 2023-2030 |
19 | Market Segmentation, Dynamics and Forecast by Application, 2023-2030 |
20 | Market Segmentation, Dynamics and Forecast by End use, 2023-2030 |
21 | Product installation rate by OEM, 2023 |
22 | Incline/Decline in Average B-2-B selling price in past 5 years |
23 | Competition from substitute products |
24 | Gross margin and average profitability of suppliers |
25 | New product development in past 12 months |
26 | M&A in past 12 months |
27 | Growth strategy of leading players |
28 | Market share of vendors, 2023 |
29 | Company Profiles |
30 | Unmet needs and opportunity for new suppliers |
31 | Conclusion |
32 | Appendix |