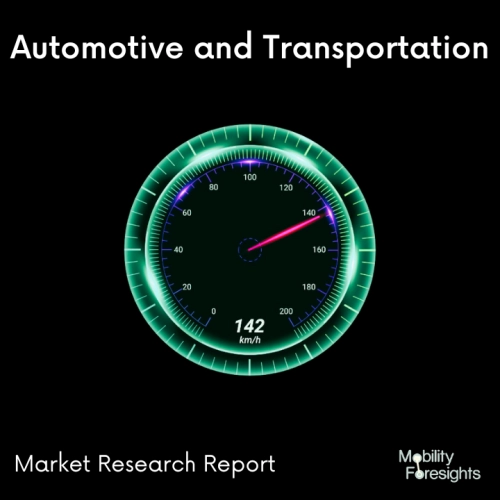
- Get in Touch with Us
Last Updated: Apr 25, 2025 | Study Period: 2024-2030
The drive shaft's principle of operation is to transfer engine torque from the gearbox or differential to the wheels, which is what it's called a torque converter. You'll also need it to adjust for any changes to the angle or length of the joints due to movement and deflection.
Outer fixed joint, inner constant velocity joint, and connecting shaft make up the front wheel drive shaft. There are also anti-lock system ring and torsion damper components.
It's a slip joint that allows the drive shaft to follow the wheel suspension's motions. It is necessary for the outboard joint at the front axle (leading axle) to transfer torque efficiently through a broad angle (up to 52 degrees).
Back axle outboard joints have a smaller angle. All the time the vehicle is in motion, constant velocity drive shafts are subjected to maximum tension. The joints and bellows must be able to resist temperatures between minus 40 and + 120 °C, as well as speeds of up to 2800 rpm, in addition to the high displacement angles and translational movement.
So that all engine rpms can deliver the needed torque. Constant velocity joints and driveshafts are essential parts of contemporary automobiles, which demand utmost safety from their components. Knocking noises are the most common symptoms of drive shaft issues, and they occur when driving around tight bends, accelerating, or when the suspension is compressed and extended, for example.
To know more about Automotive Driveshaft Market in US, read our report
The Global Automotive Driveshaft Market can be segmented into following categories for further analysis.
The global automotive drive shaft market is being driven by the global expansion of the automotive sector, particularly in developing economies such as China, India, and Brazil. Since the last decade, the automobile industry in Asia Pacific has grown at a rapid pace.
China and India's auto industry production has expanded dramatically, and they have achieved tremendous progress in terms of vehicle volume production, which pushes the global automotive drive shaft market.
The high focus of automakers on reducing vehicle weight in order to improve efficiency and lower emissions levels, as a result of the enactment of stringent emission laws in most countries, is boosting the development of new materials for drive shaft manufacturing, which is propelling the market for automotive drive shafts.
Because of the enormous number of premium and all-wheel-drive vehicles produced, Europe and North America are important markets for automobile drive axles. Due to their greater performance on snowy roads, countries in these two regions with extreme cold weather see a larger demand for four wheel drive automobiles.
Introducing the 2023 Nissan Z. With a legacy spanning more than 50 years and a fan base that spans the globe, the all-new Z is an accessible sports car for the current era.
Z Performance versions with manual transmissions have an innovative launch assist control technology that aids in giving smooth acceleration from a stopped position, a first for a rear-wheel drive Nissan car.
The launch control system is standard equipment on all models with automatic transmissions. A carbon-fiber composite drive shaft is also a characteristic of cars with manual transmissions, and 6MT Performance models now also have Synchro Rev Match.
A deal has been agreed to create a joint venture with a focus on e-axle solutions between Marelli, a top global supplier to the automotive industry, and PUNCH, a provider of driveline and powertrain solutions for research, integration, and manufacture.
Offering integrated systems for electric vehicles, both businesses pool their substantial knowledge in electric powertrains.
SI No | Timeline | Company | Developments |
1 | Dec 2020 | Dana | Spicer SPL Series driveshafts have been enhanced by Dana Incorporated for greater overall efficiency and performance. Dana's continued commitment to its core driveline technologies, which provide solutions for increasing customer application requirements, is reflected in these enhancements. |
2 | March 2021 | NTN | NTN announced that its rear half shafts (CVJ) has been adopted in the new âCadillac Escaladeâ of General Motorsâ full-size SUV |
4 | March 2022 | Doorman | Dorman is offering exclusive pre-balanced multi-piece drive shaft assemblies that pack into standard delivery boxes for convenient shipping too. |
SI No | Country/Company | Updates |
1 | Japan | Due to the high percentage of MUVs & vans among the top sellers, the driveshaft volume has been driven by these AWD vehicles in the country |
2 | China | The SUV sales in China is increasing gradually and also most driveshaft manufacturers started to produce higher efficiency and lightweight drive shafts to reduce the weight of the vehicle. As a result, the average price of driveshaft has witnessed an upward trend. |
2 | Europe | One major factor that will propel the driveshaft numbers in Europe is the continuous increase in sales of SUVs over the years. In the last 4 years, the SUV sales have risen from 33% annually in 2018 to 46% in 2021 |
3 | Globally | In the RWD segment, the 2-link & 3-link driveshafts are common nowadays where it replaces the one long propeller shafts. This is adopted to improve the torque efficiency of the overall driveline |
4 | General Motors | In 2019, GM was criticized for using aluminium driveshafts in a few models of Chevrolet, GMC & Cadillac of the 2015-2020 period. The use of these driveshafts led to vibrations & causing the vehicle to go off-road |
The drive shaft or propeller shaft in an automobile distributes the engine's power from the gearbox to the rear axle or front axle. When it comes to rear-wheel or all-wheel drive cars, the use of extruded aluminum drive shaft tubes with Cardan links has been particularly remarkable.This is because aluminum extrusion reduces inertia and vibration dampening. Electric car demand continues to grow in countries like China, the United States, and Norway.
In the next few years, automakers aim to introduce more electric car models. The majority of electric car models on the market today and in the future have all-wheel drive.
When broken, automotive drive shafts are expensive to replace. While the automotive drive shaft is a relatively ancient technology, modern solutions are nimbler and more cost-effective. All of these reasons are expected to limit the growth of the automotive drive shaft market in the future.
In the worldwide automotive drive shaft market, manufacturers strive to produce lightweight drive shafts while preserving performance and rigidity. The filament winding production technique is becoming increasingly popular among manufacturers for the fabrication of composite drive shafts. The future forecast for the automotive drive shaft market in Asia Pacific is good.
The automotive drive shaft market is being driven by nations such as India, China, Indonesia, and Thailand, where vehicle manufacturing is increasing to meet demand. Manufacturers have been obliged to lower vehicle weight in order to increase fuel efficiency as a result of environmental protection authority rules and corporate average fuel economy standards.
The automotive drive shaft market is expected to benefit from continuously rising investments in the automotive sector in North America and Europe, despite the downturn in car output.
SI No | Timeline | Company | Developments |
1 | H2-2020 | GKN Driveline | GKN Automotive sales got decreased by 19% compared to 2019 in 2020. However, the H2 sales in 2020 witnessed a 46% increase compared to H1 from $2.08B to $ 3.04B in H2-2020 |
2 | H1-2020 | Hyundai Wia | HYUNDAI-WIA announced that it will manage its dip in revenue by developing its technologies on machine tools and powertrain system productions. |
3 | H1-2020 | JTEKT | JTEKT net sales decreased from $1.94B to $1.29 B comparing H1 of 2019 and 2020 |
SI No | Timeline | Company/Country | Developments |
1 | April 2021 | Dana Incorporated | Dana Incorporated expanded their production of AWD axle systems to support Ford and Lincoln vehicles programs in Chongqing, China. Dana produced its Spicer Advantech Ultra axles with Spicer SmartConnect disconnecting all-wheel-drive systems for Ford Escape, Lincoln Nautilus and Lincoln Corsair. |
2 | May 2021 | NTN Corporation | NTN Corporation introduced its new Constant Variable Joint(CVJ) system for the rear sub axle, which is a Small and Lightweight CVJ and is used for FF-based 4WD vehicles. |
3 | Jan-2021 | Meritor Inc | Meritor Inc. introduced two new medium-duty drivelines to its Perm lube RPL driveline setup. |
4 | Feb-2020 | Dana | Dana Incorporated enhanced its Spicer SPL Series driveshafts for improved overall efficiency. The updates include maximum torque rating increase up to 7-15% for medium-duty SPL series which was available immediately and heavy-duty series will incorporate another evolution of an improved, seal design which was made available from late spring 2020 |
Although each company has a different design approach to the airless tire, most share the same basic concepts. Brake pads are used in disc brake systems and brake shoes are used in drum brake systems.
Itâs called brake lining, the consumable part sliding on disc/drum surfaces attached to the pad/shoes backing plate. State-of-the-art brake pads are constituted nowadays by resin-bonded composite friction materials, these are specially formulated to give good friction and wear performance
There have been varied levels of formulations majorly on the lines of the research and development completely focused upon the material sciences section of operations. There has been usage of Thermoplastic seal guard with retention feature excludes contaminants for improved seal performance.
Handling heavy loads over the long haul has never been easier or more efficient due to the enhanced material design to offer even greater torque, durability, and savings which also offer 70 percent more power density. No other U-joint meets the needs of high-efficiency truck applications better than the SPL U-joint.
The most recent usage has been of the patented axial cup retention and optimized yoke geometry for 30 percent higher torque and significantly enhanced life cycle which is integrated with a hollow sliding for reduced weight and axial friction forces.
As inertial mass and weight are reduced, power transmission is enhanced. Because composite materials have better specific stiffness and specific strength than traditional metallic materials, substituting composite structures for conventional metallic structures provides a number of advantages.
Dana Expands Production of All-Wheel-Drive Axle Systems to Support Additional Ford, Lincoln Vehicle Programs in China. Dana Launched e-Axles for Class 7 and 8 Vehicles, Expanding Commercially Available Heavy-Duty e-Powertrain Offerings
The value of the global automotive driveshaft market in 2027 is estimated to be around $ XX billion and an increase in CAGR of about 5.1%
Mark Williams Enterprises, a manufacturer of driveline components, has created a line of exceptionally strong driveshaft assemblies that use CV joints in place of traditional U-joints. They are primarily designed for use in drag cars with limited suspension travel, such as dragsters, altered, and funny cars, and close-located transmissions.
This design has a number of significant benefits, the most significant of which is the CV joint's ability to safely operate at a much greater operating angle than a universal joint, which is crucial when using 4-link suspensions. Additionally, it is less vibrational.
The CV shaft package from M-W can be used with "shorty" Power glide transmissions that have output shafts with 27 or 32 splines. The tail housing, driveshaft, and pinion yoke make up the assembly.
With the introduction of its complete line of flexible drive shaft couplers, SKF Vehicle Aftermarket announced that it has increased the range of drive shaft couplers it offers.
Design and validation to OEM quality standards, German-made precision, long-lasting vulcanized rubber construction, absorption of angular, radial, and axial misalignment, as well as noise isolation due to disruption of the vibration path transmitted by the structure, are additional features and advantages of SKF flexible driveshaft couplers.
Constant-velocity (CV) driveshafts for EVs and other specialty vehicles have been introduced by Kalyani Mobility Drivelines (KMD), a producer of driveline components.
KMD's CV driveshafts are made of high-strength steel and built for a range between 7,000 and 16,000 Nm of torque at speeds up to 8,000 rpm for the best performance under high torque produced by EVs, military, specialty and motorsports vehicles.
The company claims that because their driveshafts don't require the identical angle alignment required by Cardan designs, they give design flexibility. In addition, they are made to function smoothly and last a long time even in the worst conditions encountered by military and speciality vehicles.
With the introduction of its complete line of flexible drive shaft couplers, SKF Vehicle Aftermarket said that it has increased the range of drive shaft couplers it offers. For flawless installation, less downtime, and a lower total cost of ownership, the entire line of flexible couplers for drive shafts is made to fit into the car properly.
Power is transferred from the gearbox to the front or rear axles by Trak Motive® Drive Shaft Assemblies. These shafts function at varying angles and speeds using either Constant Velocity joints or single or double Cardan joints. Rear-wheel drive, four-wheel drive, and all-wheel drive vehicles all include drive shaft assemblies.
To ensure trouble-free service life from vibration and noise, all units are 100% machine balanced. Premium forged, three-layer sealed u-joints last longer without maintenance and can withstand greater torque loads.
The premium lithium grease used in U-Joint cups offers improved lubrication and resistance to high temperatures. A premium, long-lasting coating guards against early corrosion on the shaft. Compared to neoprene boots, TPE (thermoplastic elastomers) dust boots offer higher resistance to deformation, debris, oils, heat cycling, and ozone
Dorman introduced 700+ new products, including new drive shaft and control arm coverage. With the addition of 61 new component numbers to the more than 3,000 already in existence, Dorman is also increasing the coverage of its extensive line of drive shafts, which are used in millions of light- and heavy-duty vehicles operating in North America.
Dorman front and rear drive shafts are the best option to reduce the complexity of repairs because they are completely constructed, pre-balanced, and ready to install with brand-new (not remanufactured) yokes, tubes, constant velocity (CV) joints, and serviceable universal joints.
These direct replacement drive shafts are produced at Dorman's U.S. facilities for quick drop-shipping and are covered by a limited lifetime warranty. With the addition of a new part number (819-875) to suit more Chevrolet Silverado and GMC Sierra pickup trucks, Dorman is continuing to broaden its aftermarket selection of replacement flexible stainless steel fuel lines.
Because OF gasoline lines that have already been performed might be challenging to reroute under the car, replacing a corroded fuel line is frequently a time-consuming and uncertain task. Innovative fuel lines from Dorman are made of braided stainless steel and are created for the full length of the original line that is specific to the vehicle, helping to reduce installation time and frustration.
With the addition of 90 new part numbers to its existing 7,000+ control arm solutions, Dorman, one of the pioneering companies to introduce replacement control arms to the aftermarket, has maintained its position as a market leader this month.
NSK Ltd. developed the first non-contact torque sensor in the world for drive shafts in automotive. The CASE (Connected, Autonomous, Shared & Services, Electric) acronym stands for Connected, Autonomous, Shared and Services, and this new technology can increase fuel economy (lower power consumption), improve ride comfort and safety, and open up a world of new possibilities.
By monitoring the slight twisting that the drive shaft naturally experiences as the motor rotates it, the sensor measures magnetic fields to detect torque.
Conventional torque sensors have been either too expensive or sophisticated for widespread usage, but NSK's new technology enables a simple structure in a small sensor that is perfect for mass production and wide acceptance by cars.
The automobile of the near future is anticipated to maximize safety and comfort while minimising its negative effects on the environment.In order to effectively use advanced control techniques, this will necessitate that vehicles be fitted with a variety of sensors that can properly determine the status of the vehicle.
A first for the industry, NSK's non-contact drive shaft torque sensor. In order to transfer the power from the engine or motor to the wheels, a crucial part is the drive shaft. Invaluable data can be obtained from measuring torque at the drive shaft, which can be used to boost fuel efficiency, enhance comfort and safety, lessen the impact on the environment, and even spot anomalies or vehicle problems.
Driveline systems and solutions are GKN Automotive's area of expertise as a leading global provider of automotive technology. GKN Automotive provides a variety of cutting-edge driveline components, such as hollow drive shafts, with a strong emphasis on innovation.
Modern car drivetrains rely heavily on hollow drive shafts as a vital link between the engine and the wheels. The hollow drive shafts from GKN Automotive are made to provide a number of advantages, including lighter weight, better fuel economy, higher performance, and increased durability.
The hollow drive shafts from GKN Automotive are lightweight, which is one of their main advantages. GKN Automotive is able to create hollow shafts that are much lighter than conventional solid shafts by utilizing cutting-edge materials and cutting-edge production processes.
This weight loss has a good effect on the vehicle's overall weight, enhancing fuel economy and lowering pollutants. Hollow drive shafts with outstanding strength and stiffness characteristics can be made by GKN Automotive using lightweight materials like high-strength steel and aluminum.
These shafts are capable of managing the engine's torque and rotational forces, resulting in dependable power transmission to the wheels. The hollow drive shafts made by GKN Automotive go through a series of testing and validation procedures to guarantee that they satisfy the strict performance standards of contemporary automobiles.
The hollow drive shafts made by GKN Automotive help improve the handling and dynamics of the car.These shafts' reduced weight and rotational inertia provide better acceleration, braking, and maneuverability. This may result in a more enjoyable driving experience, better responsiveness from the car, and better performance all around.
The hollow drive shafts from GKN Automotive must also be durable. Drive shafts that can resist the rigors of varied driving scenarios are made by the company using cutting-edge engineering methods and materials.
The drive shaft's lifespan is extended and the risk of failure is decreased thanks to the hollow design's ability to manage stress and load optimally. GKN Automotive's hollow drive shafts are designed to specifically satisfy the needs of various vehicle platforms and drivetrain layouts.
GKN Automotive provides specialized solutions to guarantee optimum performance and compatibility whether it's a front-wheel drive, rear-wheel drive, or all-wheel drive vehicle.Additionally, GKN Automotive concentrates on cutting-edge manufacturing techniques to create hollow drive shafts of the highest caliber.
Tight tolerances and consistent product quality are achieved by using precision machining, forging, and assembly procedures in their cutting-edge production facilities. The company's devotion to strict industry standards and certifications demonstrates its dedication to quality.
GKN Automotive prioritizes research and development above and beyond their core competencies in design and manufacture. To push the limits of driveline technology, they continually invest in innovation and technological breakthroughs.
Due to their dedication, they are able to remain at the forefront of the automotive sector and offer innovative solutions, such as hollow drive shafts, to satisfy the changing demands of both customers and car manufacturers.
Leading automakers across the world have recognized and trusted GKN Automotive's hollow drive shafts. Drive shafts from GKN automobile have been incorporated into a variety of cars across several market categories as a consequence of their agreements with significant automobile manufacturers.
Hollow drive shafts are made by renowned driveline component manufacturer GKN Automotive. Their hollow drive shafts provide lightweight design, increased durability, improved performance, and increased fuel efficiency.
The cooperation between Panasonic Jaguar Racing and GKN vehicle, the world's top supplier of electric driveline and all-wheel drive vehicle technologies and systems, is still going strong.
GKN Automotive driveshafts have been used on several of Jaguar's performance vehicles in motorsport, including the Le Mans-winning C-Type and the company's XJ220 supercar.
GKN Automotive's most recent motorsport collaboration is with Formula E, but it already boasts an impressive track record of producing championship-winning and speed-record breaking race cars.
The brand-new Volvo XC90 SUV's driveline partner is GKN Driveline, a leading provider of automotive driveline systems and components worldwide. As a development partner, GKN Driveline collaborated with Volvo Cars on the new XC90's front-wheel drive and all-wheel drive (AWD) drivelines.
More and more automakers are working with GKN to create driveline strategies that unite fun driving with unmatched efficiency.
No other supplier is in a position to provide full front wheel drive and all-wheel drive systems in the manner that GKN is able to do with the system developed for the brand-new Volvo XC90, which highlights GKN's evolving role within the industry.
SI No | Timeline | Company | Developments |
1 | 2022 March | Dana | Dana's total revenue figures for 2021. $8.9 billion, up $1.8 billion, with $197 million in net income attributable to Dana, a $228 million increase. |
2 | June 2021 | Dorman | Dorman Products, Inc. signed a definitive agreement to acquire Dayton Parts, a leading independent heavy-duty undercarriage aftermarket component supplier for $338 million.
|
4 | Sept 2021 | DSS Inc | DSS, Inc. Expands Services Capabilities Through Acquisition of SBG Technology Solutions, Inc.
|
SI No | Timeline | Company | Updates |
1 | Dec 2021 | GKN Driveline | GKN Automotive invested EUR 3.5 million to set up an advanced research center in the UK to enhance the electrified vehicleâs technology in the country to meet the zero-emission commitment. |
2 | Nov 2021 | Comer Industries | Comer Industries acquired German-based IFA Kardin to expand their driveshaft portfolio and to offer a range of prop shafts and related components for the agriculture, construction and special-vehicle market |
3 | August 2021 | Meritor Inc | Meritor Inc was selected to provide electric drivetrain sub-systems like Blue Horizon 14Xe electric drive axles for Helion's Hyper truck ERX electrified powertrain for Class 8 trucks. |
4 | March 2021 | Nexteer Automotive | Nexteer Automotive has decided to expand its portfolio with Half shaft Technologies to meet the demands of Electric Vehicles (EVs). The Driveline Technologies include Axle Half Shaft, Tubular Shaft, Trunnion Trypot, Shudder less Trypot and about three joints. |
5 | March 2017 | Dana Incorporated | Dana Incorporated acquired the axle housing and driveline shaft manufacturing operations of the U.S. Manufacturing Corporation (USM) for $100 million |
6 | January 2017 | Dana Incorporated | DANA Incorporated entered into a multi-year sales agreement with Navistar International Corporation for $200 million in order to make driveline components for on-highway, bus and vocational vehicles |
There are a variety of ways in which drive shafts can be utilized in different vehicles, including front-wheel drive, four-wheel drive, and the previously stated front-engine, rear-wheel drive combinations.
Other vehicles, such as motorbikes, locomotives, and ships, also utilize drive shafts. Due to the fact that various components must be in different places in the vehicle, the drive shaft is largely utilized to transfer torque between components separated by a distance.
Due to the fact that the transmission and rear axle are on different sides of the car, a front-engine rear-wheel drive vehicle must have a lengthy drive shaft connecting them.
Munich-based family office AEQUITA, agreed to acquire IFA Groupâs drive shaft and joint specialist from Halbesleben and AEQUITA will strengthen the growth and innovation of IFA Group to expand its market position.
Hyundai WIA Corporation has been involved in development of various shafts and joints required for the shaft operations within the automotive processes. It has introduced variations of Solid Shaft Friction Welding Hollow Shafts and Monoblock Hollow Shafts which are based to have varied levels of performance requirements.
They have dynamic damper and torsional strength as required to have better and optimized NVH Performances within the vehicle of operations.
Dana Corporation has been part of the production of driveshafts for commercial and passenger class vehicles. Engine down speeding calls for faster axle ratios, which require a stronger, more durable driveshaft to handle the added input torque.
Dana Incorporation held a market share of XX% as the estimated revenue is $2.1 Billion in driveshaft segment by developing driveshafts for light vehicles, commercial vehicles and off-highway vehicles
In 2021, GKN Automotive has invested $ 4 billion in the Advanced Research Centre is being partly supported through the Melrose Skills Fund to develop next generation e-drive systems powering future electrified vehicles and to increase their engineering capability & strengthen research and development in the UK.
GKN Automotive joined with Tata Technologies, to establish an advanced global e-mobility software engineering center in Bangalore, India. The co aims to innovate GKN Automotiveâs advanced electric drive technologies for future electrified vehicles on a global level.
SPL 350 main driveshaft and mating SPL 250 inter-axle shaft are specifically designed to handle the greatest amount of torque for severe-duty vocational applications as well as low-emission, high-efficiency trucks. It is also Capable of meeting future fast axle ratio requirements.
Sl no | Topic |
1 | Market Segmentation |
2 | Scope of the report |
3 | Abbreviations |
4 | Research Methodology |
5 | Executive Summary |
6 | Introduction |
7 | Insights from Industry stakeholders |
8 | Cost breakdown of Product by sub-components and average profit margin |
9 | Disruptive innovation in the Industry |
10 | Technology trends in the Industry |
11 | Consumer trends in the industry |
12 | Recent Production Milestones |
13 | Component Manufacturing in US, EU and China |
14 | COVID-19 impact on overall market |
15 | COVID-19 impact on Production of components |
16 | COVID-19 impact on Point of sale |
17 | Market Segmentation, Dynamics and Forecast by Geography, 2024-2030 |
18 | Market Segmentation, Dynamics and Forecast by Product Type, 2024-2030 |
19 | Market Segmentation, Dynamics and Forecast by Application, 2024-2030 |
20 | Market Segmentation, Dynamics and Forecast by End use, 2024-2030 |
21 | Product installation rate by OEM, 2023 |
22 | Incline/Decline in Average B-2-B selling price in past 5 years |
23 | Competition from substitute products |
24 | Gross margin and average profitability of suppliers |
25 | New product development in past 12 months |
26 | M&A in past 12 months |
27 | Growth strategy of leading players |
28 | Market share of vendors, 2023 |
29 | Company Profiles |
30 | Unmet needs and opportunity for new suppliers |
31 | Conclusion |
32 | Appendix |