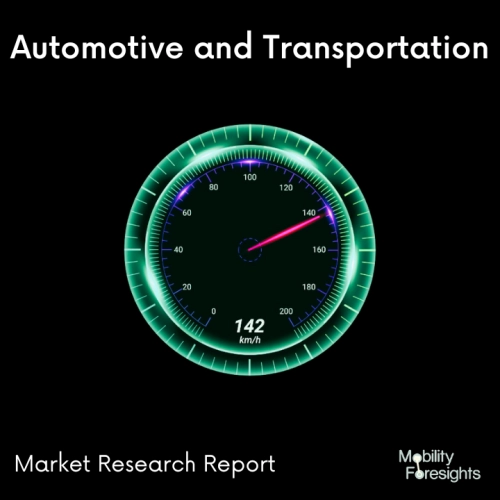
- Get in Touch with Us
Last Updated: Apr 26, 2025 | Study Period: 2023-2030
Key parts of a car's drivetrain system are manufactured using a method known as automotive driveline horizontal machining. With the use of specialized horizontal machining centers, driveline components are accurately shaped and formed using this machining technique, assuring their precision, strength, and longevity.
The gearbox, differential, axles and driveshafts are some of the parts that make up an automobile's driveline. These parts are essential for getting power from the engine to the wheels, which enables smooth movement and effective power delivery.
Production of these driveline components requires horizontal machining specific to automotive drivelines. Advanced cutting tools and computer numerical control (CNC) systems used in the machining centers allow for the high-precision machining of intricate forms and features.
The procedure starts with the loading of raw materials into the horizontal machining center, usually metal alloys like steel or aluminum. The driveline components' required shape and dimensions are created by the CNC system, which precisely directs the cutting tools as they remove material.
Numerous operations, including milling, drilling, turning, and threading, are carried out throughout the horizontal machining process. The components of the driveline are fitted, aligned, and functionally tested throughout these procedures. Additionally, to produce complicated features or enhance component performance, specialized machining methods like broaching may be used.
Horizontal machining for automotive drivelines has various benefits. First off, it enables high production rates, guaranteeing a steady supply of driveline parts for vehicle assembly lines. Second, because of the precision and accuracy attained throughout this machining process, components are produced that adhere to exacting performance and quality criteria.
Additionally, driveline horizontal machining makes it possible to produce durable yet lightweight components, reducing overall vehicle weight and increasing fuel economy. This is particularly crucial in the automobile sector, where there is a constant push for more environmentally friendly and sustainable cars.
The Global Automotive Driveline Horizontal Machining Market accounted for $XX Billion in 2022 and is anticipated to reach $XX Billion by 2030, registering a CAGR of XX% from 2023 to 2030.
The DMU 50 Eco Horizontal Machining Centre was introduced by DMG Mori. This system has several characteristics that increase productivity and efficiency, including a high-speed spindle and a broad work envelope. It is designed for high-volume manufacturing of driveline components.
The Horizontal Machining Centre VF-8SS was introduced by Haas Automation. This system has a number of features that promote accuracy and repeatability, such as a Haas toolroom grade spindle and a high-precision linear guideway system. It is suited for a range of applications, including the manufacturing of driveline components.
The Integrex i-700 Horizontal Machining Centre was introduced by Mazak. This system has several characteristics, such as a high-speed spindle and a high-rigidity machine bed, that enhance surface polish and dimensional accuracy. It is intended for the manufacturing of high-precision driveline components.