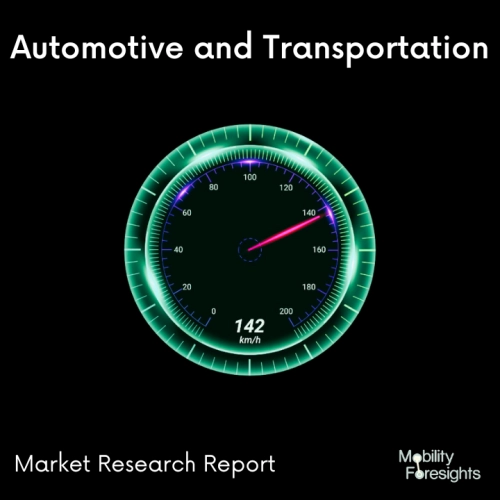
- Get in Touch with Us
Last Updated: Apr 25, 2025 | Study Period: 2023-2030
Seals and sealants provide a variety of unappreciated but critical roles. Seals and sealant materials, while unsightly, play an important function in all contemporary automobiles, keeping pollutants out and fluids in, and are employed in the great majority of systems and components.
Seals must withstand heat, vibration, dust, fluid, and chemical attack for years and tens of thousands of kilometers while being easy to apply during production and complying with health, safety, and environmental laws.The most common use in EVs is sealing a battery pack housing, followed by gasketing for power conversion devices such as inverters, motors, and other components of an electric powertrain.
All high-voltage connectors, as well as the primary battery box, module, and cell enclosures, as well as the lines and connectors in fuel cell systems, electrically powered accessories, and the thermal management system supporting the battery, motors, and charging system, must be sealed.
In high-speed applications, Low friction seals for eDrive units are suited to electric motor needs and combine robust sealing performance with specified bi-directional shaft movement. It has bi-directional shaft rotation, static oil, air tightness, and less friction. It offers the automated user strong sealing, long life, and low power consumption.
In addition to providing sufficient sealing capabilities for short-term crucial reverse shaft rotation, these seals provide decreased friction losses, increased durability, and can resist oil temperatures, allowing the system to consume less power.
New car models rely on efficient electric drive technologies to improve OEM sustainability plans while delivering comfort and a greater driving experience to their customers. The number of electric cars on our roadways grows year after year. OEMs' new models demand efficient electric drive systems to fulfill increasing CO2 standards while providing consumers with a comfortable driving experience, excellent performance, and a high degree of usability.
Meanwhile, industry trends suggest a growing demand for specialists that specialize in electric drive units (EDUs) and bring the necessary depth of expertise and experience to the table. Furthermore, highly adaptable and fast deployable system solutions are required to decrease overall development timeframes, allowing for the quicker realization of innovative electric vehicle ideas.
The Global Automotive E-drive Unit Seals Market accounted for $XX Billion in 2022 and is anticipated to reach $XX Billion by 2030, registering a CAGR of XX% from 2023 to 2030.
Frequently hear the terms e-mobility, electromobility, and electric automobiles. This technology has gained substantial traction in recent years and shows no signs of abating. eMobility encompasses not just automobiles, but also e-bikes, e-skateboards, e-scooters, and even electric passenger planes and helicopters.
The eMobility sector is extremely fast-paced, with new technologies and businesses continually emerging. It is one in which Original Equipment Manufacturers (OEMs) and system suppliers confront unique problems and ever-changing needs.
This distinguishes the industry in that clients do not yet have well defined requirements or established solutions. Turcon MC1 and Turcon MC2 are the first electrically conductive Polytetrafluoroethylene (PTFE)-based materials for use in spring-loaded and elastomer-energized seals.
They allow us to ensure critical features like insulation, thermal and electrical conductivity, and electromagnetic shielding. These Turcon materials are an ideal answer for electrical systems, addressing the new and specific sealing issues they provide. The compounds must be able to endure the high temperatures present in the e-Motor as well as the battery fluids.
Fluid compatibility is especially difficult since the media used in the e-Motor differs from that used in petrol and diesel engines, which have well-established and tested sealing systems. There is an additional challenge: the chemical mix of a fully charged battery differs from that of an empty one.
Trelleborg Sealing Solutions has created customer-specific battery cover seals for the battery. Because the battery is tailored to the geometry of the vehicle, each battery housing and sealing solution is unique. The covers, which are made of Ethylene Propylene Diene Rubber (EPDM) and metal bushings, not only protect the batteries from moisture but also give resistance to high-pressure water.
At the virtual Vienna Motor Symposium, Freudenberg Sealing Technologies will unveil a new generation of electrically conductive seals. The seals are intended to protect bearings against electrically-induced corrosion and to reduce electromagnetic interference.
Inverter power semiconductors are frequently located right above the motor. Silicon carbide semiconductors switch large currents up, causing small voltage changes in the process. These overshoots have a frequency of one or two megahertz, which is within the range of medium-wave radios.
Freudenberg hopes to avoid both of these effects with a new generation of conductive seals marketed as eCONevo. The business put the fundamental premise into serial manufacturing, and the seals are utilized in a popular European EV. With eCONevo, a very thin, conductive nonwoven material is applied to the radial shaft seal ring, allowing direct electrical contact between the rotor shaft and motor housing.
The creation of a novel material mix currently allows the use of a nonwoven material with an AC resistance of roughly one ohm. As a result, the material's electrical conductivity is strong enough not only to resist electro-corrosion but also to emit electromagnetic waves.
Sl no | Topic |
1 | Market Segmentation |
2 | Scope of the report |
3 | Abbreviations |
4 | Research Methodology |
5 | Executive Summary |
6 | Introduction |
7 | Insights from Industry stakeholders |
8 | Cost breakdown of Product by sub-components and average profit margin |
9 | Disruptive innovation in the Industry |
10 | Technology trends in the Industry |
11 | Consumer trends in the industry |
12 | Recent Production Milestones |
13 | Component Manufacturing in US, EU and China |
14 | COVID-19 impact on overall market |
15 | COVID-19 impact on Production of components |
16 | COVID-19 impact on Point of sale |
17 | Market Segmentation, Dynamics and Forecast by Geography, 2023-2030 |
18 | Market Segmentation, Dynamics and Forecast by Product Type, 2023-2030 |
19 | Market Segmentation, Dynamics and Forecast by Application, 2023-2030 |
20 | Market Segmentation, Dynamics and Forecast by End use, 2023-2030 |
21 | Product installation rate by OEM, 2023 |
22 | Incline/Decline in Average B-2-B selling price in past 5 years |
23 | Competition from substitute products |
24 | Gross margin and average profitability of suppliers |
25 | New product development in past 12 months |
26 | M&A in past 12 months |
27 | Growth strategy of leading players |
28 | Market share of vendors, 2023 |
29 | Company Profiles |
30 | Unmet needs and opportunity for new suppliers |
31 | Conclusion |
32 | Appendix |