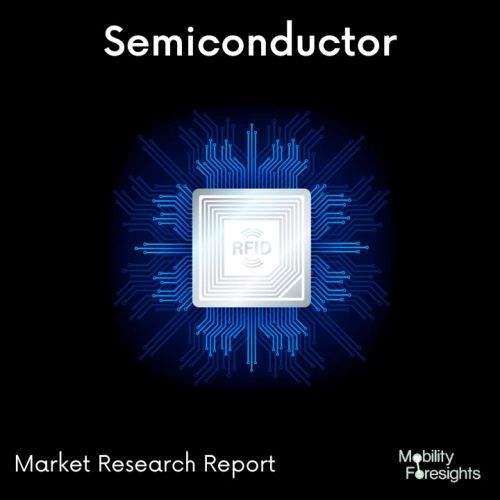
- Get in Touch with Us
Last Updated: Apr 25, 2025 | Study Period: 2024-2030
An electronic package called a flip chip ball grid array (FCBGA) is created by soldering the integrated circuit (IC) to the substrate. The Flip Chip Ball Grid Array is a low-cost, high-performance semiconductor packaging system that connects the die to the substrate using the controlled collapse chip connection technology, commonly known as flip chip.
A particular kind of ball grid array known as a flip chip BGA uses a controlled collapse chip connection, also known as a flip-chip. The solder bumps on the chip pads' tops are what make it function. On the wafer are integrated circuits at the beginning of the process. The chips have metallized pads with solder balls on each one.
The global automotive flip - chip ball grid array (FC - BGA) market accounted for $XX Billion in 2023 and is anticipated to reach $XX Billion by 2030, registering a CAGR of XX% from 2024 to 2030.
The demand for smaller electronic devices, improved electrical efficiency, and decreased power consumption are driving the usage of flip chips ball grid array in microelectronic devices. Because flip chips improve the performance of electrical machinery that runs at high frequencies, they are increasingly being used in microwave and ultrasonic operations.
The flip chip bga market occupies less space than its rivals, has a low inductance, and has superior system performance as a whole. These features account for flip chips' extensive application in electrical devices.
Furthermore, it is anticipated that throughout the forecast period, continuous R&D initiatives by leading global market players would provide the flip chip bga market new growth prospects.Because of its enhanced advantages, such as their compact size, strong design, higher efficiency, and capacity to support high-frequency applications at an affordable price, flip chips bga have also gradually replaced wire bonding packaging.
The packaging industry is currently using wire bonding more and more frequently. Due to their outstanding characteristics, such as increased I/O capacity, high thermal & electrical effectiveness, and substrate adaptability for diverse performance needs, flip chips are replacing wire bonded technology.
Toppan Printing Co., Ltd. announced intentions to add a new production line to its Niigata facility in order to grow its flip-chip ball grid array (FC-BGA) substrate business (Shibata City, Niigata Prefecture, Japan).
In order to fulfil the growing demand for these thinner substrates brought on by continued developments in semiconductor technology, the new line will enable a 2.5x increase in FC-BGA substrate production capacity.
Modern coreless FC-BGA substrates will be produced by the new line using cutting-edge materials co-developed with Toppan R&D Laboratories. The production line will be able to operate more quickly and effectively thanks to the removal of the core material and a fully rationalised in-line manufacturing process.
Flip-chip ball grid array trial production by Samsung Electronics is scheduled to start in Vietnam, and then commercial manufacturing will start at the company's facility in Thai Nguyen province. Flip-chip BGA is a mid-priced, high-performance semiconductor packaging system that connects the die to the substrate via controlled collapse chip connection technology, commonly known as flip chip.
The trend of placing more circuitry in ever-smaller component packages necessitates precision microelectronic design and assembly skills. A good example is the Micro-Flip Chip Ball Grid Array (Micro-FCBGA). This assembly method is quite difficult to carry out, yet it enables to meet the requirement for low size and weight packages with high-density interconnects.
High precision is necessary for ultra-fine pitch FCBGAs to ensure the dependability of the numerous interconnections. A method for the assembly of a customised Micro-FCBGA with 2100 connections and a pitch of 150m was created by Valtronic. The placement tolerance for a component with such a small size is 10 micrometres for maximum mechanical contact and few assembly flaws.
The Flip Chip (FC)-style, H-PBGA, the newest packaging innovation from Intel, is a member of this family. The Controlled Collapse Chip Connect die is housed in an Organic Land Grid Array (OLGA) substrate in the FC-style, H-PBGA component. The FC-style H-PBGA offers many, low-inductance connections from chip to package, as well as advantages in die size and cost, in addition to the usual benefits of PBGA packages.
The performance of HPBGA is on par with or greater than that of an additional on-chip metal layer since it enables numerous, low-inductance connections in the FCstyle. The FC technology also benefits die size by getting rid of the bond pad ring, improving power busing, and making greater use of the metal.
Since there is no cavity with the OLGA substrate, the package is smaller and thermal management is improved because the thermal solution may make direct contact with the die.
Sl no | Topic |
1 | Market Segmentation |
2 | Scope of the report |
3 | Abbreviations |
4 | Research Methodology |
5 | Executive Summary |
6 | Introduction |
7 | Insights from Industry stakeholders |
8 | Cost breakdown of Product by sub-components and average profit margin |
9 | Disruptive innovation in the Industry |
10 | Technology trends in the Industry |
11 | Consumer trends in the industry |
12 | Recent Production Milestones |
13 | Component Manufacturing in US, EU and China |
14 | COVID-19 impact on overall market |
15 | COVID-19 impact on Production of components |
16 | COVID-19 impact on Point of sale |
17 | Market Segmentation, Dynamics and Forecast by Geography, 2024-2030 |
18 | Market Segmentation, Dynamics and Forecast by Product Type, 2024-2030 |
19 | Market Segmentation, Dynamics and Forecast by Application, 2024-2030 |
20 | Market Segmentation, Dynamics and Forecast by End use, 2024-2030 |
21 | Product installation rate by OEM, 2023 |
22 | Incline/Decline in Average B-2-B selling price in past 5 years |
23 | Competition from substitute products |
24 | Gross margin and average profitability of suppliers |
25 | New product development in past 12 months |
26 | M&A in past 12 months |
27 | Growth strategy of leading players |
28 | Market share of vendors, 2023 |
29 | Company Profiles |
30 | Unmet needs and opportunity for new suppliers |
31 | Conclusion |
32 | Appendix |