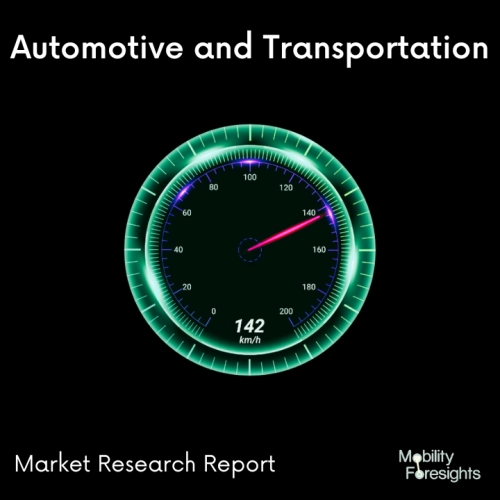
- Get in Touch with Us
Last Updated: Apr 25, 2025 | Study Period: 2024-2030
Whether gasoline or diesel the highest priority in an automobile must be to keep the fuel far from being ignited and fuel tanks play a crucial role in that.Many leading manufacturers are investing on developing the multi-layered high density polyethylene fuel tanks which results in low permeation to minimize fuel hydrocarbons. These fuel tanks are environmental friendly and meet the government requirements. But, growing demand for battery electric vehicles worldwide will restrain the growth.
The advent of plug-in hybrid vehicles has led to development of pressurized fuel tanks. The implementation of various plastic products such as polyethylene, ethylene vinyl alcohol has eliminated the steel tanks in hybrid vehicles. Manufacturers are implementing latest technology to meet the high standards such as internal venting systems and anti-slosh elements (to reduce the noise inside the tank).
The most common segment is 45-70 L segment where it is dominated by the passenger cars Sedan, Hatchback, MUVs, Premium and Luxury Vehicles. Europe and China markets are skewed in favour these segments.
In US owing to greater number of pick-up trucks which are close to even 120 L in case of AWD trucks, is dominated by 70+ L capacity tanks. India has the highest number of vehicles with sub 45 L tank capacity.To know more about Global Automotive Plastic Fuel Tank Market, read our report
A shift from metal (steel and aluminium) is witnessed in the recent past. The plasticâs ability to act as insulator to heat and less chance of igniting the fuel and more importantly they result in better fuel mileage due to the amount of overall weight of vehicle being reduced. These factors have made the plastic to be the leader in the segment.Polyethylene tanks are the highest gainers in the market. However, the plastic tanks are concentrated in the 2 wheelers and certain passenger cars. The aluminium and the steel remains the primary option for the trucks and buses. Steel tanks are the ideal option for diesel vehicles to meet the low evaporative emission standards.
The passenger cars across the world are dominated by 45-70 L segment. Among these the hatchback, sedans and even SUVs in many countries fall under this category. The commercial vehiclesâ range is broadly varied. The light commercial vehicles have an average capacity of 100-120 L. Among heavy commercial vehicles buses attract larger fuel tanks than trucks and in US buses with more than 900L are witnessed.
The US is the largest market for pick-up trucks which are also among the top selling light duty vehicles and the average fuel tank capacity of the pick-up trucks in US is 95 litres.The average fuel tank capacity of top selling cars other than pick-up trucks is 55 litres.
US commercial vehicle market is the largest in the world with ~2 Million units sold per annum. The average tank capacity of the heavy duty trucks in US is 350 litres. All these factors collectively have made US the leader in the fuel tank market by value.
The top selling cars have the capacity in the 45-55 range. The rise in EV vehicles sale in Europe in 2019 was close to ~40%, the highest in the world. Out of which ~65% were the BEVs. This will restrain the fuel tank market.
Chinese top selling cars all are on average having a capacity of 50L fuel tank. Exception being Haval H6 powerful SUV tank capacity going up to 70L.China accounts for almost 50 % of EVs in the global market. 81% of overall EVs sold in China last year are BEVs; this will limit the fuel tank growth in the region.
In India 5 of the top 10 selling cars in India is having sub 45 litres fuel tank capacity. India accounts for the highest amount of 2 wheelers in the world. The fuel tank is on average 5.5 litres for scooter and 12 litres for motorcycles.
Manufacturers are adopting fiber patch replacement technique in addition to the existing fiber reinforced plastics. This is expected to significantly increase the lightweight potential.
The introduction of hydrogen fuel cell powered buses in Europe will initiate the demand for hydrogen tanks for the commercial vehicles. The hydrogen fuel under high pressure requires modern technology and modern materials such as carbon fiber, nano materials to contain the hydrogen. This will boost the R&D in the fuel tank sector.
The global Automotive fuel tank market is estimated at $XX Billion in 2022 growing at --%CAGR till 2030
COVID-19 is forcing petrochemical executives to rethink the future of the industry. Slowing demand growth, growing surplus, and a shrinking value pool were already present before the pandemic and have only become more pronounced.
Chemical-industry leaders and financial investors alike will need to update their perspectives and management agendas to focus on recovery scenarios, regionalized supply chains, and capital productivity.While COVID-19 is still restricting us from âbusiness as usualâ in many ways, the companies continue to make the best of the situation at hand.
Across their businesses, the companies established enterprise-wide pandemic response teams and implemented processes and procedures to enhance the safety of their facilities and protect the health and safety of their employees.
TI Fluid Systems (TIFS), a global leader in automotive fluid systems technology, announced the launch of a new generation of plastic fuel tanks capable of handling the high pressure needs of a hybrid electric vehicle (HEV).
Volkswagen China has began mass manufacture of its plastic gasoline tank for the Passat and Magotan Plug-in Hybrid Electric Vehicle (PHEV) models.This ground-breaking technology is the result of extensive design and collaboration, as well as rigorous testing and vehicle evaluations.
Conventional gasoline tanks function at atmospheric pressure; however, in certain full electric driving modes, the latest generation HEV cars are predicted to withstand cycle pressure up to 400 mbar. The technology release, according to TIFS, provides a light-weight plastic alternative for HEVs that solves the drawbacks of competing welded internal tank structure.
Materials: High-density polyethylene, steel, aluminum, and other materials can be used to make gasoline tanks for automobiles.Each material offers advantages and things to keep in mind. Compared to plastic tanks, which are lightweight, corrosion-resistant, and easy to mold into intricate shapes, steel and aluminum tanks offer strength and durability.
Depending on the material, different welding and joining processes may be used for fuel tanks. Resistance welding, laser welding, and adhesive bonding are typical techniques.These procedures guarantee the structural soundness of the tank and stop leaks.Multilayer Construction: Some fuel tanks, particularly plastic tanks, have a multilayer construction.
This entails the use of various layers with various qualities, such as barrier layers to stop fuel absorption, adhesive layers for bonding, and high-density polyethylene for structural strength.Fuel tanks use materials and design features to improve their crash resistance and reduce the possibility of fuel leaks in the event of a collision.To safeguard the tank from outside forces, this comprises strengthened tank walls, impact-absorbing constructions, and crumple zones.
Leak Detection Systems: To quickly detect fuel leaks, advanced fuel tanks may be equipped with leak detection systems.These systems employ sensors or pressure monitoring to find leaks or variations in fuel pressure, sending out alerts or cutting off the gasoline supply to stop future leaks.Fuel tanks use technology to reduce evaporative emissions, which reduces the release of fuel vapors into the atmosphereThis comprises equipment that collects and stores fuel vapors for later combustion in the engine, such as sealed fuel caps, charcoal canisters, and vapor recovery systems.
Fuel level sensing: Fuel tanks have built-in sensors that accurately measure the amount of fuel.These sensors measure the gasoline level using a variety of technologies, such as capacitive, ultrasonic, or resistive ways, enabling the driver to keep an eye on fuel usage.
Hydrocarbon Permeation Barrier: Fuel tanks may have hydrocarbon permeation barriers to reduce fuel vapor permeability.Usually made of specialized coatings or materials, these barriers prevent gasoline vapor from diffusing through the tank walls.Depending on the material of the tank, different manufacturing processes, such as blow molding, injection molding, or stamping, are used to make automotive gasoline tanks. These methods guarantee effective manufacturing and dependable quality.
The key factors anticipated to fuel market expansion in the next few years are an increase in the demand for lightweight automobiles for improved fuel economy, rising vehicle manufacturing, and fast urbanisation. The rising sales and demand for commercial vehicles as a result of the expansion of the e-commerce sector, which in turn has fueled expansion of the construction and logistics sectors, is one of the key reasons fueling the market's expansion.
The study's market may not expand as quickly, though, due to reasons including the increasing use and demand for electric vehicles as well as the rising cost of base metals like aluminium.The fact that a fuel tank holds and protects combustible fluid petrol makes it a vital automobile component. The fuel tank is a crucial component of the car that is integrated with the engine and pumps the gasoline as needed in the form of pressurised petrol.
The tank protects the flammable gas from coming into contact with the outside world and keeps the fire out of the way. The tank varies in size, design, and capacity depending on the type of vehicle and is composed of materials like plastic and metal. Since they are lightweight, plastic tanks are frequently used in automobiles. Therefore, increasing the manufacture of passenger automobiles is primarily to blame for the rise in demand for plastic storage tanks.
Automobile manufacturing companies are spending a lot of money researching and developing lightweight vehicles.The fuel consumption of cars is significantly reduced by their light weight. Additionally, a lighter vehicle contributes to a reduction in the amount of carbon dioxide that it emits.The need for automotive fuel tanks is increasing as a result of the automotive OEMs increasing their production volume to suit the growing demand for cars around the world.
The need for the use of lightweight materials in automobiles is being fueled by the strict natural limits put in place by the government to control the rising global pollution.In order to reduce fuel emissions and enhance vehicle performance, the automotive industry is attempting to create lightweight cars. Automobile manufacturers are spending a lot of money on research to come up with new ideas and create lightweight materials for making automobile parts to lighten up vehicles. Traditional metal tanks have been replaced by plastic tanks in the car industry recently.
Due to a variety of inherent benefits that plastic fuel tanks have over metal fuel tanks, they have become the preferred option among vehicle production businesses and are becoming well-known in the industry. High-Density Polyethylene (HDPE) is a material that is often used to make these tanks.The plastic tanks' flexibility allows for customization in accordance with OEM requirements. The automobile industry is putting more of an emphasis on making lightweight vehicles because they are necessary in the modern world. Most passenger automobiles and light commercial vehicles come equipped with plastic fuel tanks.
The market for traveller cars has developed as a result of increasing urbanisation, growing standards of living, and strong consumer demand. Young people are more likely to favour lightweight, high-performance, and low-emission vehicles. Thus, it is projected that the market will grow more quickly in the near future as a result of the various advantages of having plastic fuel tanks in automobiles.
S No | Company Name | Development |
---|---|---|
1 | Inergy Automotive | Automotive parts supplier Inergy Automotive Systems, a subsidiary of Plastic Omnium which produces automotive fuel tanks and systems, has officially launched its new fuel tank. |
2 | TI Automotive | TI Automotive, the global supplier of automotive fluid systems, opened its newest fuel tank systems production facility The new Guangzhou facility is representative of the growth within the plastic fuel tank segment of the automotive industry. |
Inergy Automotive Systems Aircraft typically use three types of fuel tanks: integral, rigid removable, and bladder. Integral tanks are areas inside the aircraft structure that have been sealed to allow fuel storage.
TI Automotive global automakers look to reduce weight and improve emissions, plastic fuel tanks play a major role TI Automotive has developed some of the most advanced blow-molding production technology in the industry and have been producing award-winning products that improve packaging and component placement, while reducing emissions and weight.â
Europe accounts for the major fuel tank manufacturers such as Plastic Omnium (France), Kautex Textron (Germany), Serbatoi (Italy) and TI Fluid (UK). Some of the other fuel tank manufacturers are Yapp Automotive Systems (China), Fuel Total Systems (Japan), Magna Inc (Canada) and Yachiyo (Japan). Indiaâs largest tank manufacturer is Dali & Samir Engg Pvt Ltd which has a well-established presence in the commercial vehicles segment.Although Fuel cell is still an unproven technology in terms of mass scale commercialization, it has been increasingly seen as a practical alternative to costly high capacity BEVs.
The obvious benefit being less than 10 minutes refill time. Some of the companies that produce hydrogen fuel tanks are Plastic Omnium and Cevotec (Germany).Kautex TEXTRON revenues for the year were $11.7 billion. It recorded a segment profit of $751 million with a profit margin of 6.4%, the manufacturing businesses generated $833 million of net cash from operating activities of the continuing operations.
Plastic Omnium generated economic revenue of â¬2,157 million in the first quarter, up 4.8% at constant exchange rates.Growth was driven by Plastic Omnium Modules, the group Outperformed by 4 points in Europe and 22 points in Asia excluding China there was a strong growth in China (+79%) and as a result the revenue rose 12.5% at constant exchange rates.
Due to demand for the company's product and services in the last quarter of 2020, YappAutomotive Parts Co Ltd revenues increased 17% to RMB1.98B and its net income increased by 45% to RMB114.8M. Financial results of Unipres Corporation showed decreases in both income and profit due to the effects of reduced production among their customers caused by the global pandemic. The company posted 234.5 billion Yen of net sales, -11.3 billion of operating income, -9.1 billion of ordinary income, and -17.6 billion in net income attributable to the company.
Sl no | Topic |
1 | Market Segmentation |
2 | Scope of the report |
3 | Abbreviations |
4 | Research Methodology |
5 | Executive Summary |
6 | Introduction |
7 | Insights from Industry stakeholders |
8 | Cost breakdown of Product by sub-components and average profit margin |
9 | Disruptive innovation in the Industry |
10 | Technology trends in the Industry |
11 | Consumer trends in the industry |
12 | Recent Production Milestones |
13 | Component Manufacturing in US, EU and China |
14 | COVID-19 impact on overall market |
15 | COVID-19 impact on Production of components |
16 | COVID-19 impact on Point of sale |
17 | Market Segmentation, Dynamics and Forecast by Geography, 2024-2030 |
18 | Market Segmentation, Dynamics and Forecast by Product Type, 2024-2030 |
19 | Market Segmentation, Dynamics and Forecast by Application, 2024-2030 |
20 | Market Segmentation, Dynamics and Forecast by End use, 2024-2030 |
21 | Product installation rate by OEM, 2023 |
22 | Incline/Decline in Average B-2-B selling price in past 5 years |
23 | Competition from substitute products |
24 | Gross margin and average profitability of suppliers |
25 | New product development in past 12 months |
26 | M&A in past 12 months |
27 | Growth strategy of leading players |
28 | Market share of vendors, 2023 |
29 | Company Profiles |
30 | Unmet needs and opportunity for new suppliers |
31 | Conclusion |
32 | Appendix |