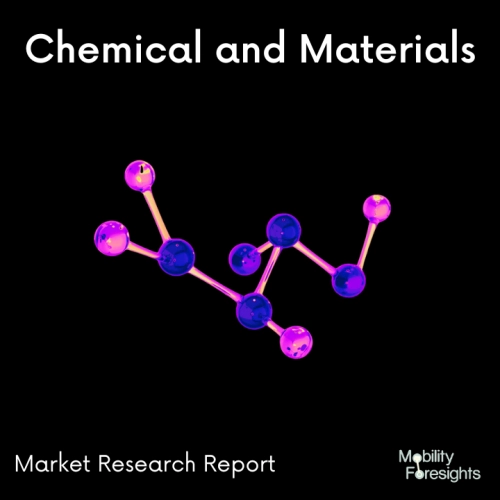
- Get in Touch with Us
Last Updated: Apr 25, 2025 | Study Period: 2024-2030
Engineering plastics, which include polycarbonate and PC resin, are plastics that are specifically created for improved strength, temperature resistance, and other mechanical qualities.
Plastic lenses for eyewear, medical devices, automobile parts, protective gear, greenhouses, digital discs (CDs, DVDs, and Blu-ray), and outdoor lighting fixtures are all frequently made of PC.
A strong, translucent plastic with exceptional rigidity, strength, and impact resistance is polycarbonate. Because of its optical clarity, polycarbonate is perfect for uses including machine guards, signage, architectural glazing, face shields, skylights, and POPS.
Polycarbonate's primary drawback is that it isn't scratch-resistant. For instance, a polycarbonate patio canopy would get scratched if a branch were to fall on it. The polycarbonate can be polished to solve this issue.
An amorphous glassy thermoplastic called polycarbonate is prone to cracking or crazing when put under pressure or in contact with chemicals.
1 Flexible polyvinyl chloride is frequently in touch with, or attached to, polycarbonate when it is moulded into medical devices (PVC).
Acrylic sheets will perform better than polycarbonate sheets if clarity and light transmittance are your main concerns. On the other hand, polycarbonate sheeting is a clear choice if you need strong impact resistance.
The Global Automotive grade polycarbonate resin market accounted for $XX Billion in 2023 and is anticipated to reach $XX Billion by 2030, registering a CAGR of XX% from 2024 to 2030.
The first batch of automotive-grade resins with mechanically recycled parts was introduced by Saudi Basic Industries Corporation (Sabic).
The TRUCIRCLE cycle solution and service portfolio includes these items. There are three varieties of PP compound, a talc-filled polypropylene with high fluidity and low emissions.
The automotive industry's sustainability strategy can be supported by the new Trucircle materials, which can boost the value of post-consumer goods and extend the life of plastic waste.
The first set of new products are these ones. Both the inside and outside of automobiles can be constructed with Sabic resin and mechanically recycled components.
Compound has excellent heat resistance, low emissions, and good stiffness. It is appropriate for internal and under-the-hood HVAC (heating, ventilation, and air conditioning) components as well as those that are not visible on the dashboard.
The internal life cycle assessment (LCA) reveals that the PP compound comprises recycled PP, which can lower the product's carbon footprint compared to the corresponding original PP compound.
Sl no | Topic |
1 | Market Segmentation |
2 | Scope of the report |
3 | Abbreviations |
4 | Research Methodology |
5 | Executive Summary |
6 | Introduction |
7 | Insights from Industry stakeholders |
8 | Cost breakdown of Product by sub-components and average profit margin |
9 | Disruptive innovation in the Industry |
10 | Technology trends in the Industry |
11 | Consumer trends in the industry |
12 | Recent Production Milestones |
13 | Component Manufacturing in US, EU and China |
14 | COVID-19 impact on overall market |
15 | COVID-19 impact on Production of components |
16 | COVID-19 impact on Point of sale |
17 | Market Segmentation, Dynamics and Forecast by Geography, 2024-2030 |
18 | Market Segmentation, Dynamics and Forecast by Product Type, 2024-2030 |
19 | Market Segmentation, Dynamics and Forecast by Application, 2024-2030 |
20 | Market Segmentation, Dynamics and Forecast by End use, 2024-2030 |
21 | Product installation rate by OEM, 2023 |
22 | Incline/Decline in Average B-2-B selling price in past 5 years |
23 | Competition from substitute products |
24 | Gross margin and average profitability of suppliers |
25 | New product development in past 12 months |
26 | M&A in past 12 months |
27 | Growth strategy of leading players |
28 | Market share of vendors, 2023 |
29 | Company Profiles |
30 | Unmet needs and opportunity for new suppliers |
31 | Conclusion |
32 | Appendix |