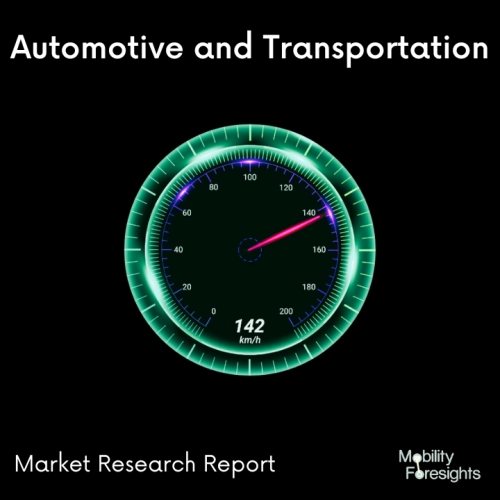
- Get in Touch with Us
Last Updated: Apr 25, 2025 | Study Period: 2023-2030
INTRODUCTION
The automotive industry has been making use of high voltage interconnects for decades to ensure safe and reliable power delivery to the various vehicle systems. High voltage interconnects are used in a wide range of applications, from charging systems to lighting and entertainment systems.
High voltage interconnects are designed to provide a safe and reliable connection between the power source and the devices that require it. They are also used to ensure that the power delivered to the device is not compromised by external electrical interference.
High voltage interconnects are designed to withstand the high voltage and current levels that are common in automotive applications. They are also designed to be able to handle the high temperatures, vibration, and other environmental factors that are present in automotive applications.
To ensure that the interconnects are reliable and safe, they are usually tested to meet stringent standards. This can include testing for insulation resistance, withstand voltage, and surge protection.
High voltage interconnects are typically made from copper and other metallic materials, and they often feature multiple layers of insulation to ensure the safety of the connection. Furthermore, they are designed to be able to tolerate high temperatures and vibration, as well as any other environmental factors that may be present.
High voltage interconnects are an essential component of any automotive application. They provide a reliable and safe connection between the power source and the device requiring it, ensuring that the power is delivered safely and efficiently.
GLOBAL AUTOMOTIVE HIGH VOLTAGE INTERCONNECT MARKET SIZE AND FORECAST
The Global Automotive High Voltage Interconnect market accounted for $XX Billion in 2022 and is anticipated to reach $XX Billion by 2030, registering a CAGR of XX% from 2023 to 2030.
High voltage wiring and components are indicated by the Electric Vehicle Orange color of ABB's Harnessflex EVO Connector Interfaces, which are new for the heavy-duty electric vehicle industry. With its Harnessflex EVO connection Interfaces, ABB Installation Products created a line of hinged high-voltage connection backshells for heavy-duty electric cars.
According to ABB, the trend toward lower-emission automobiles is reflected in contemporary engine designs that have a lot of electrical wiring and higher operating temperatures. For any electric car to function, the stability of the cable to the connector is essential. Particularly susceptible to high engine temperatures, strain, abrasion, vibration, infiltration, and corrosion is heavy-duty EV wire.
ABB's Harnessflex EVO Connector Interfaces for Electric Vehicles are orange in color to denote high-voltage wiring and components, provide cable-to-connector strain relief with superior mechanical performance, and stop debris intrusion. The tamper-proof, integrated clip system of the Harnessflex EVO Connector Interfaces adds an extra degree of security to high voltage systems and fortifies resilience to vibration and abrasion in EV applications.
With the Neue Klasse, the BMW Group is launching a new age of fully electric vehicle technology. The high-voltage batteries' range, charging time, durability, and carbon footprint are critical success factors in this situation. Up to 30% faster charging will be possible with the upcoming battery generation. The BMW Group is making significant investments in its production facilities and the sixth generation of high-voltage batteries to be ready for the significant shift.
Currently, the BMW Group produces high-voltage batteries and e-components for its current line of e-models at its plants in Shenzhen, China, and Dingolfing, Leipzig, and Regensburg, Germany. We will constantly adhere to the "local for local" approach and open new assembly sites for our sixth-generation high-voltage batteries in Debrecen, Hungary; San Luis PotosÃ, Mexico; and Woodruff, near Spartanburg, USA.
THIS REPORT WILL ANSWER FOLLOWING QUESTIONS
Sl no | Topic |
1 | Market Segmentation |
2 | Scope of the report |
3 | Abbreviations |
4 | Research Methodology |
5 | Executive Summary |
6 | Introduction |
7 | Insights from Industry stakeholders |
8 | Cost breakdown of Product by sub-components and average profit margin |
9 | Disruptive innovation in the Industry |
10 | Technology trends in the Industry |
11 | Consumer trends in the industry |
12 | Recent Production Milestones |
13 | Component Manufacturing in US, EU and China |
14 | COVID-19 impact on overall market |
15 | COVID-19 impact on Production of components |
16 | COVID-19 impact on Point of sale |
17 | Market Segmentation, Dynamics and Forecast by Geography, 2023-2030 |
18 | Market Segmentation, Dynamics and Forecast by Product Type, 2023-2030 |
19 | Market Segmentation, Dynamics and Forecast by Application, 2023-2030 |
20 | Market Segmentation, Dynamics and Forecast by End use, 2023-2030 |
21 | Product installation rate by OEM, 2023 |
22 | Incline/Decline in Average B-2-B selling price in past 5 years |
23 | Competition from substitute products |
24 | Gross margin and average profitability of suppliers |
25 | New product development in past 12 months |
26 | M&A in past 12 months |
27 | Growth strategy of leading players |
28 | Market share of vendors, 2023 |
29 | Company Profiles |
30 | Unmet needs and opportunity for new suppliers |
31 | Conclusion |
32 | Appendix |