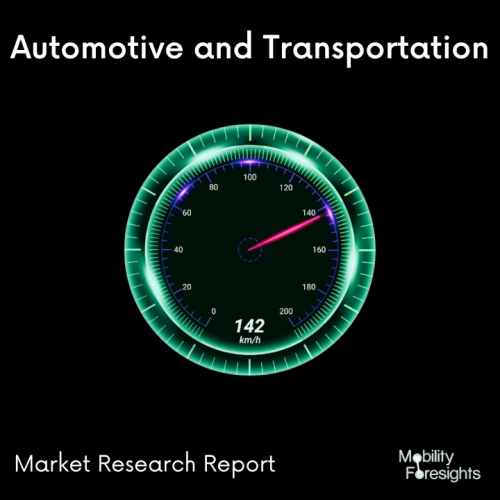
- Get in Touch with Us
Last Updated: Apr 25, 2025 | Study Period: 2023-2030
The inertial sensor includes internal processing of all recorded motions of the vehicle in addition to the angular rate and acceleration sensors. One control unit processes all of the data.
measurement of yaw rate, lateral, longitudinal, vertical, and other accelerations, as well as detection of inclination Almost every digital device and intelligent vehicle now include inertial sensors, which are a critical enabling technology in a wide range of applications.
Examples of applications using inertial sensor data include localization, navigation, and mapping. For collecting movement patterns outside of traditional laboratory contexts, wearable inertial sensors are also extensively utilised in health care and sporting applications.
The majority of the numerous new applications greatly benefit from hardware miniaturisation and developments in micro-electromechanical systems, which have produced sensor designs with much reduced size, weight, cost, and energy requirements.
The inertial measurement unit's (IMU) readings are acquired in the sensor's moving coordinate system, which makes temporal integration and direct interpretation more challenging.
As the recorded angular rates, accelerations, and magnetic field vectors rarely coincide with the actual motion states of interest, such as orientations, velocities, joint angles, or even more high-level parameters, three-dimensional strapdown integration is necessary.
A relevant coordinate system of the item of interest, to which the sensor is attached, is frequently not sufficiently well-aligned with the sensor's coordinate systems.
The Global automotive inertial sensor market accountedfor $XX Billion in 2022 and is anticipated to reach $XX Billion by 2030, registering a CAGR of XX% from 2023 to 2030.
The 6DoF inertial sensor series from Panasonic Industries provides critical inputs to a control system as well as precise information on the status and motion of a vehicle or piece of equipment. Future vehicles and machinery will be equipped with an increasing number of driving aids for comfort and safety.
For numerous purposes, including motion detection, location, sensor fusion, inclination detection, and many others, comprehensive sensing is essential. The "6in1 sensor," also known as the new high-quality and dependable 6-axis Gyro & Accelerometer 6DoF sensor series from Panasonic Industries, is offered in a wettable flank QFN package.
This home has an advantageous unique edge that makes a step. The solder makes a solid connection in the step's neck. High-quality soldering and error-free assembly are made possible as a result, which is crucial for car safety.
The P-1775 inertial measurement unit (IMU) with KVH's revolutionary PIC Inside TM photonic integrated chip (PIC) technology is now available, and the first deliveries have begun, according to a statement from KVH Industries. The technology has been developed and tested by KVH for more than three years, and it is now being included into current product lines.
The P-1775 IMU with PIC Within has been incorporated into a new generation rocket launch vehicle by one of the first clients. With its PIC Inside technology, KVH substitutes discrete fibre optic components with a single integrated planar optical chip, streamlining production while retaining or enhancing accuracy and performance.
The PIC technology will be incorporated into KVH's inertial sensor product line for usage in a variety of applications, including stabilisation, pointing, and navigation. Fibre optic gyros (FOGs) from KVH and solutions based on FOGs are especially well suited for the sizable and expanding autonomous market.
This market covers products for the land, the sea, and the air, including trucks, people movers, drones, and mining and construction machinery.
Sl no | Topic |
1 | Market Segmentation |
2 | Scope of the report |
3 | Abbreviations |
4 | Research Methodology |
5 | Executive Summary |
6 | Introduction |
7 | Insights from Industry stakeholders |
8 | Cost breakdown of Product by sub-components and average profit margin |
9 | Disruptive innovation in the Industry |
10 | Technology trends in the Industry |
11 | Consumer trends in the industry |
12 | Recent Production Milestones |
13 | Component Manufacturing in US, EU and China |
14 | COVID-19 impact on overall market |
15 | COVID-19 impact on Production of components |
16 | COVID-19 impact on Point of sale |
17 | Market Segmentation, Dynamics and Forecast by Geography, 2023-2030 |
18 | Market Segmentation, Dynamics and Forecast by Product Type, 2023-2030 |
19 | Market Segmentation, Dynamics and Forecast by Application, 2023-2030 |
20 | Market Segmentation, Dynamics and Forecast by End use, 2023-2030 |
21 | Product installation rate by OEM, 2023 |
22 | Incline/Decline in Average B-2-B selling price in past 5 years |
23 | Competition from substitute products |
24 | Gross margin and average profitability of suppliers |
25 | New product development in past 12 months |
26 | M&A in past 12 months |
27 | Growth strategy of leading players |
28 | Market share of vendors, 2023 |
29 | Company Profiles |
30 | Unmet needs and opportunity for new suppliers |
31 | Conclusion |
32 | Appendix |