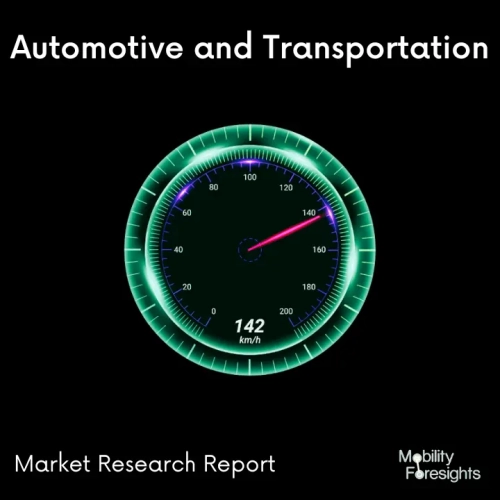
- Get in Touch with Us
Last Updated: Apr 27, 2025 | Study Period: 2024-2030
To detect an object's acceleration, tilt, and vibration, inertial sensors convert inertial force into quantifiable electrical impulses. Utilizing single-crystal silicon sensor components, inertial sensors may now be created thanks to micromachining technology.
All of the key system design criteria, such as cheap cost, high performance, high precision, and tiny form factor, are met by these micron-sized sensors.
Using a sensor unit as small as a few micrometers in size, the inertial sensors may detect the tiniest change in position, orientation, and acceleration of an object many meters long. These sensors work on the same principles as macroscopic inertial sensors.
The two main categories of inertial sensors are accelerometers, which detect linear acceleration in one or more axes, and gyroscopes, which measure angular motion.
The Global automotive inertial sensors market accounted for $XX Billion in 2023 and is anticipated to reach $XX Billion by 2030, registering a CAGR of XX% from 2024 to 2030.
Honeywell is developing the next generation of inertial sensor technology with funding from the U.S. Defense Advanced Research Projects Agency (DARPA), and it will eventually be used in both commercial and defense navigation applications. According to tests conducted by Honeywell labs, the new sensors are more accurate than Honeywell's HG1930 inertial measurement unit (IMU), a tactical-grade product with more than 150,000 units currently in use.
The P-1775 inertial measurement unit (IMU) with KVH's new PIC Inside photonic integrated chip (PIC) technology is now available, and the first orders have begun to arrive, according to a KVH Industries, Inc. announcement.
The technology has been developed and tested by KVH for more than three years, and it is now being incorporated into current product lines. The P-1775 IMU with PIC Inside has been incorporated into a new generation rocket launch vehicle by one of the first customers.
The PIC Inside product uses modular designs for simple integration and has exceptional repeatability unit-to-unit. It is intended to deliver 20 times more accuracy than less expensive MEMS inertial measurement units.
KVH presented the science underlying the technology to an audience of engineers at a leading inertial sensor conference, outlining the extensive development, testing, and advantages of the new technology. The company also announced that it had delivered its first product prototypes containing PIC technology to leading automotive customers.
To execute previously discrete sensor data collecting directly within the ESC electronics module, TRW Automotive Holdings Corp has introduced its first Electronic Stability Control system (ESC) with an integrated inertial measurement unit (IMU) on the Lancia Delta.
Traditionally, stand-alone IMUs have been used to introduce ESC systems. As a practical solution to decrease the number of modules in the vehicle while maintaining the performance of the ESC, TRW will now produce an ESC with integrated IMU.
The cost, weight, and complexity of the wiring harness for the ESC system are all decreased by TRW by directly integrating the IMU into the ESC. For automakers who want to offer both ABS and ESC braking systems throughout a model range, the integrated architecture offers an easy scaling solution.
The first MEMS 6-axis inertial sensor (IMU), the MIC6100AL, has been released by MEMSIC, the top provider of MEMS technology solutions worldwide. The product incorporates a 3-axis gyroscope and a 3-axis accelerometer, enabling sensitive sensing for motion-sensing interactive systems like game controllers and smart remote controls.
MEMSIC has a capable algorithm team that can support users with algorithms that can handle the demands of complex application scenarios. By sensing the displacement and motion changes of the physical world, MEMSIC's reliable and frequently produced products give people a more intelligent, dependable, and safe technological experience.
These products are widely used in automotive, industrial, medical, wearable, smart home, and consumer electronics applications.
A new open-source inertial measurement unit sensor from sensor manufacturer ACEINNA has been released for use in autonomous off-road, construction, and agricultural vehicle applications. The OpenIMU300RI, as it is known, will assist in a GPS's direction determination and track motion on consumer electronics.
A robust, sealed, open-source, nine-degree-of-freedom inertial measurement unit is the OpenIMU300RI (IMU). MEMS-based open-source, inertial sensing systems from ACEINNA provide precise positioning solutions that enable simple-to-use, centimeter-accurate navigation systems for cutting-edge autonomous driving technology.
To maintain its successful history of MEMS inertial sensor technology, Angst+Pfister, a Murata partner, enters into a relationship with the Finnish software company Nordic Inertial (NI). The sensors can be chosen and compared using the embedded 32-bit processor by the requirements (static, dynamic).
Following the announcement of their collaboration to commercialize inertial sensors based on Qualtré, Inc.'s game-changing Bulk Acoustic Wave Technology, Alps Electric took action to deepen their relationship with Qualtré by making a strategic investment in the firm.
The alliance combines Qualtré's experience in MEMS sensor research with Alps Electric's strong manufacturing capabilities and global sales skills. The two businesses have been working together continuously for several years, and leaders from both organizations are confident that their collaboration will offer clients cutting-edge products and first-rate customer service.
A prominent developer of MEMS sensor platforms, InvenSense, Inc., recently announced a partnership with Panasonic Corporation to create new, high-performance MEMS-based inertial sensors for automobile safety.
The innovative, industry-leading 6-axis (3-axis accelerometer + 3-axis gyroscope) safety inertial sensor enables system downsizing for safety applications like rollover detection and electronic stability control. The new safety inertial sensor, which is now sampling, fulfills the most stringent performance requirements for low-bias drift, low-sensitivity drift, and high-vibration resilience.
Sl no | Topic |
1 | Market Segmentation |
2 | Scope of the report |
3 | Abbreviations |
4 | Research Methodology |
5 | Executive Summary |
6 | Introduction |
7 | Insights from Industry stakeholders |
8 | Cost breakdown of Product by sub-components and average profit margin |
9 | Disruptive Innovation in the Industry |
10 | Technology Trends in the Industry |
11 | Consumer trends in the industry |
12 | Recent Production Milestones |
13 | Component Manufacturing in the US, EU and China |
14 | COVID-19 impact on overall market |
15 | COVID-19 impact on Production of components |
16 | COVID-19 impact on the point of sale |
17 | Market Segmentation, Dynamics and Forecast by Geography, 2024-2030 |
18 | Market Segmentation, Dynamics and Forecast by Product Type, 2024-2030 |
19 | Market Segmentation, Dynamics and Forecast by Application, 2024-2030 |
20 | Market Segmentation, Dynamics and Forecast by End Use, 2024-2030 |
21 | Product installation rate by OEM, 2023 |
22 | Incline/Decline in Average B-2-B selling price in the past 5 years |
23 | Competition from substitute products |
24 | Gross margin and average profitability of suppliers |
25 | New product development in the past 12 months |
26 | M&A in the past 12 months |
27 | Growth strategy of leading players |
28 | Market share of vendors, 2023 |
29 | Company Profiles |
30 | Unmet needs and opportunities for new suppliers |
31 | Conclusion |
32 | Appendix |