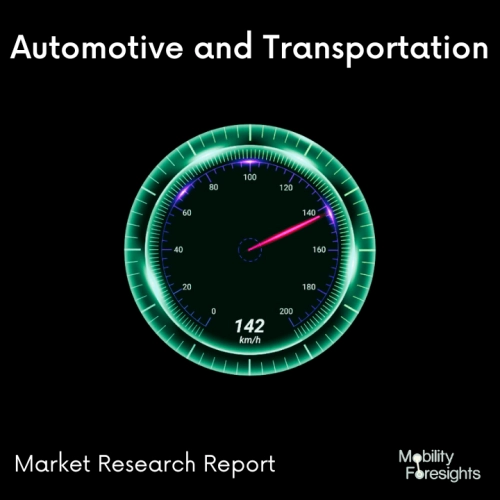
- Get in Touch with Us
Last Updated: Apr 25, 2025 | Study Period: 2024-2030
The Importance being given to the plastic integration within the Automotive Sector has increased alongside the usage of lighter metals due to increased consideration towards Environmental Decontamination and further Recycling procedures. This has made the industry cautious about the plastic end user potential with a possible integration being done into the automotive parts in various levels of requirements.
Polypropylene, PVC, ABS and Polyurethane make up for more than 80% of plastics used by the auto industry .Automotive Plastics Market has been increasingly replacing metal components for more than a decade now. There is a growing demand for thermoplastics, which can withstand high temperatures and a lot of abuse. They also allow multiple child parts to be integrated into one bigger module.
SI no | Timeline | Company | Developments |
1 | November-2021 | Viking Plastics | Injequaly Industria LTDA, a Brazil-based injection moulding company in Sao Paulo and the partner of Viking Plastics in Pennsylvania has expanded and is planning to add a new plant in Joinville. |
2 | October 2021 | Evonik | In order to strengthen Evonikâs global alkoxide business, Evonik is planning to open a new plant for the production of methylate in Southeast Asia. |
3 | October 2021 | Sabic | A new Polypropylene compounding line is set to open in Genk, Belgium. |
Continental structural plastics (CSP) supplied Ford Motor Company with the industryâs first composite, dual-wall-dash engine shroud for use in the 2020 Ford Explorer. This sheet moulded compound (SMC) advanced composite shroud significantly reduces the powertrain NVH experienced in the vehicle cabin.CSP VICTALL announced that China-based Jiangling motors corporation (JMC) will use advanced composites for the pickup boxes of its new Yuhu 3 and Yuhu 5 pickup trucks.
Governments across the globe have introduced regulations for vehicles that compel OEMs to promote and increase the use of lightweight plastic materials. Companies have developed some advanced plastics which help increase the fuel economy of a vehicle along with ensuring performance and safety. With a 10% reduction in the mass of the vehicle, the fuel economy can be reduced by 6-8%. The use of plastics reduces the consumption of fuel thereby promoting sustainability as less energy is consumed for acceleration due to less weight.
Teijin Limited announced that its Sereebo carbon fibre reinforced thermoplastic (CFRTP) has been selected by General Motors for use in select pickup box applications. This is the worldâs first use of CFRTP for structural parts in high volume production vehicles.The global shortage of Nylon 66, is an important risk in the Automotive plastics market.
The company Evonik announced the expansion of its product portfolio of polyamide 12 compounds for insulating electrical conductors with the new product VESTAMID LX9050 OR. Polyamide is developed as required by the automotive industry to be used in electric vehicles. The product is with halogen fire-free additives to achieve the highest possible fire resistance with flammability class V-0.
In 2020, 3.2Million units of Plug-in EVs were sold globally +40% YOY. The volume of electrified vehicles was ~5Million units. The growing penetration of electric propulsion in the past 5 years has made every auto supplier sit up and take notice and itâs not any different in case of automotive plastics suppliers.As the frontal design of an EV varies significantly as compared to an ICE vehicle due to different cooling requirements, the front grille could be aptly substituted by a plastic body with better air-cooling passages.
The flexibility offered by plastics primarily in terms of weight and costs could be an advantage to the suppliers as electric vehicles` demand grows further.Robust thermoplastics and other flame-retardant materials are especially preferred in EV applications due to their better thermal management properties.
SI no | Timeline | Company | Developments |
1 | November 2021 | Covestro | Covestro has launched a 37% bio-based, breathable, multi-purpose resin Decovery SP-8310 for exterior coating. |
2 | November 2021 | Vestamid | Vestamid has launched a long term thermoplastic material which is insensitive to corrosion, VESTAMID NRG 5901. It can hold up to 315 psi for oil and gas gathering. |
3 | September 2021 | Borealis | Uponor Infra and Borealis have partnered to make a gravity plastic pipe that will reduce CO2 by 70%, Ultra Rib 2 Blue pipe. |
4 | August 2021 | Borealis | The first chemically recycled polypropylene packed and ready to drink iced coffee cups has been created by Emmi, Greiner Packaging and Borealis. |
When considering the pre pandemic situation within the global scenario, the expansion in the production facilities and support requirements for plastic based manufacturing being integrated into the automotive sector.This expansion was seen in large numbers and volumes alongside possible price fluctuations in key raw materials like polypropylene, polyurethane, and acrylonitrile butadiene styrene may have adverse impact on the automotive plastics market.
For instance, in July 2016, Dow polyurethanes EMEAI announced a price increase in polyurethane material due to significant raw material cost increase. Polyol prices increased to USD 104-110/ton.With plastic injection moulding playing a key role in helping create todayâs lightweight, fuel efficient vehicles, it is crucial that auto manufacturers partner with an injection moulder who has expertise in complex automotive parts and understands the latest industry regulations and standards.
The first mechanically recycled content automobile grades from Sabic are now accessible. New resins include:Xenoy T2NX2500UV resin is an unfilled, UV-stabilized combination of polycarbonate (PC) and polyethylene terephthalate (PET); Xenoy T2NX5230 resin is a mineral-filled PC/PET blend. Sabic T2E-3320EH PP compound is a high-flow, low-emission, talc-filled polypropylene (PP).
All three materials have recycled content and perform similarly to the previously used virgin resins, providing automotive clients with additional options that can aid in meeting their sustainability objectives. The new Trucircle materials enhance the automobile industry's sustainability ambitions by giving plastic trash an opportunity to live longer and by assisting in the improvement of post-consumer product value.
The first of many mechanically regenerated Sabic resins to be produced, these new compounds have the potential to be used in interior and exterior car applications. The grades are being introduced by Sabic to support numerous brand-new automotive applications.For interior and under-the-hood parts, as well as non-visible HVAC (heating, ventilation, and air conditioning) components under the instrument panel, Sabic T2E-3320EH PP compound offers rigidity, low emissions, and good heat resistance.
Mineral reinforcement makes up 16% of the Xenoy T2NX5230 resin from Sabic, while recovered PET makes up 29% of it. Its characteristics make it a suitable solution for painted body panels, trim, and other components, much like Xenoy T2NX2500UV resin.In comparison to Xenoy T2NX2500UV resin, the product's reinforcement offers stronger rigidity and a lower coefficient of linear thermal expansion (CLTE), making Xenoy T2NX5230 resin a viable choice for roof spoilers and exterior trim. High flow is provided by both Xenoy grades for increased throughput.
To know more about Automotive Plastic Market in North America, read our report
Plastic Omnium reached a deal to buy AMS-Osram's automotive-lighting business for 65 million euros ($72 million), a move aimed at supporting the French company's push into new market segments.Osram Licht used to be in the automobile lighting sector.
Automotive body modules and fuel systems are manufactured by Plastic Omnium. It was one of the bidders for Hella, a German auto parts manufacturer.Hella was later bought out by Faurecia, a French conglomerate, for 6.8 billion euros.
The automotive plastics market was estimated at $XX Billion in 2021, growing at â% CAGR till 2030.Plastics usage in tailgates has been growing at double digits in the past 5 years and with the rise in power tailgates(including hands-free), plastics will have further headway to grow in the auto industry.
Western Europe has a lower consumption of plastics per vehicle than the United States, due to a smaller average size of the car in the region. Plastics consumption (in kg per vehicle) is the lowest in China compared to the other regions. Chinaâs plastics consumption is expected to increase faster than in other regions as it grows from a lower base.
The COVID-19 pandemic has disrupted the automotive industry as well as the supply chain operations across the globe due to lockdowns and halt in manufacturing activities. Along with the initial supply line and manufacturing units, the markets across the globe have experienced plunged in demand. The automotive industry has been one of the most affected that creates uncertain supply timelines and recovery.
The pandemic has caused limited supply of raw materials, vehicle parts as well as electronic components and semiconductor chips which affect the production of vehicles and reduces the demand for components needed by the automotive industry.The industry has been facing drop-in registration and sales of new vehicles, decline in working capital and investments and halt in the production activities.The automotive plastic industry is dependent on the automotive industry for vehicle sales as a result of which the plastic industry has been negatively affected.
Saudi Basic Industries Corp. (SABIC) of Riyadh, Saudi Arabia, has introduced automotive resins with mechanically recycled content. The three new grades are intended to accommodate a wide range of new automotive applications. The first is Sabic's T2E-3320EH PP compound, which has great heat resistance, rigidity, and low emissions.
With a recycled component, it has a lower carbon footprint than a comparable virgin PP compound by up to 24%. The Sabic XENOY T2NX2500UV resin, which contains 21% recycled PET, has exceptional heat and impact resistance.The XENOY T2NX5230 resin, which contains 16 percent mineral reinforcement and 29 percent recycled PET, is the third new grade. It has more rigidity and a lower coefficient of linear thermal expansion thanks to its reinforcing.
SI no | Timeline | Company | Sales |
1 | Q3-2021 | Nolato | At the end of Q3 2021, the sales had increased to SEK 3,033 million and the operating profit rose up to SEK 339 million. |
2 | Q2-2021 | Borealis | The half year net sales of Borealis is about â¬4 million and in 2020 it was only â¬2.9 million. |
3 | Q3-2021 | SABIC | The revenue at the end of September 2021 is $11.6 million and in 2020 it was about $7 million. |
4 | Q3-2021 | BASF | The net sales at the end of Q3 is â¬19.6 million and at the end of the first three quarters the net sales were about â¬58.8 million. |
5 | Q3-2021 | Evonik Industries | The third quarter sales of Evonik Industries rose to â¬3.8 billion and in 2020 the sales was â¬2.9 billion. |
6 | Q3-2021 | Covestro Group | The company reported â¬4.3 billion for sales at the end of third quarter and in Q3 2020 the sales were â¬2.7 billion. |
7 | Q3-2021 | Plastic Omnium | The economic revenue at the end of third quarter is about â¬1.79 billion and in 2020 it was â¬2.09 billion with a drop of 14.4%. |
In H2- 2019, despite sales slowdown, many auto plastics and interior suppliers expanded their presence. For example, Yanfeng Automotive interiors strengthened its presence in Serbia (eastern Europe),French automotive supplier Novares Group inaugurated an expansion project at its Arouca manufacturing facility in northern Portugal, to specifically manufacture parts for PSA Group.Tigerpoly Manufacturing, inc. planned to expand its operation in metro Columbus, Ohio. Vuteq USA Inc. planned to invest $60 million to open Injection molding facility in Huntsville, Alabama, to serve the Mazda Toyota Manufacturing USA Inc auto assembly plant.
Borealis has entered into North America by inauguration of its new PP compounding plant in Taylorsville, North Carolina. The move is considered a hallmark in the companyâs global expansion efforts.BASF SE announced the inauguration of a new research and development center in Shanghai, China which will also constitute a special automotive application center for the research and developmental activities specially for the automotive sector.
The center is set to develop innovative products for the automotive industry from various exterior and interior applications.The company DuPont announced the acquisition agreement with Laird Performance Materials based in China for $2.3 billion. The company is the leader in thermal management and high-performance electromagnetic shielding along with an offering of performance components as well as solutions to manage the heat protection devices for smart and autonomous vehicles from electromagnetic shielding.
Borealis Group announced an agreement with Dutch PPE Solutions to provide them with renewable PP from the companyâs Bornewables range of circular polyolefins to reduce the climate impact of the company. The company has come in a strategic partnership with TOPAS Advanced Polymers who are the leading producers of cyclic olefin copolymers for the development of a new class of engineering materials for capacitor film applications to bridge the gap between high-end plastics and polymers.
Covestro has announced partnership with Nexeo Plastics to develop 3D printing solutions. 3D at Nexeo plastics will offer global distribution of the additional Covestro filaments as well as Somos resin for SLA and digital light processing and liquid crystal display for 3D printing. Evonik Industries AG announced the first green hybrid bond with a nominal volume of EUR 500 million. The company is extending its corporate venture capital activities in China with investments into GRC SinoGreen Fund V and Richland VC Fund III. The funding will focus on development of advanced materials, high-end manufacturing equipment, digital transformation and green technologies.
The company released the half-yearly financial statement for the year 2021 with sales worth EUR 3,636 million which was a significant increase from the sales recorded in the year 2020 worth EUR 2,827 million.
Sl no | Topic |
1 | Market Segmentation |
2 | Scope of the report |
3 | Abbreviations |
4 | Research Methodology |
5 | Executive Summary |
6 | Introduction |
7 | Insights from Industry stakeholders |
8 | Cost breakdown of Product by sub-components and average profit margin |
9 | Disruptive innovation in the Industry |
10 | Technology trends in the Industry |
11 | Consumer trends in the industry |
12 | Recent Production Milestones |
13 | Component Manufacturing in US, EU and China |
14 | COVID-19 impact on overall market |
15 | COVID-19 impact on Production of components |
16 | COVID-19 impact on Point of sale |
17 | Market Segmentation, Dynamics and Forecast by Geography, 2024-2030 |
18 | Market Segmentation, Dynamics and Forecast by Product Type, 2024-2030 |
19 | Market Segmentation, Dynamics and Forecast by Application, 2024-2030 |
20 | Market Segmentation, Dynamics and Forecast by End use, 2024-2030 |
21 | Product installation rate by OEM, 2023 |
22 | Incline/Decline in Average B-2-B selling price in past 5 years |
23 | Competition from substitute products |
24 | Gross margin and average profitability of suppliers |
25 | New product development in past 12 months |
26 | M&A in past 12 months |
27 | Growth strategy of leading players |
28 | Market share of vendors, 2023 |
29 | Company Profiles |
30 | Unmet needs and opportunity for new suppliers |
31 | Conclusion |
32 | Appendix |