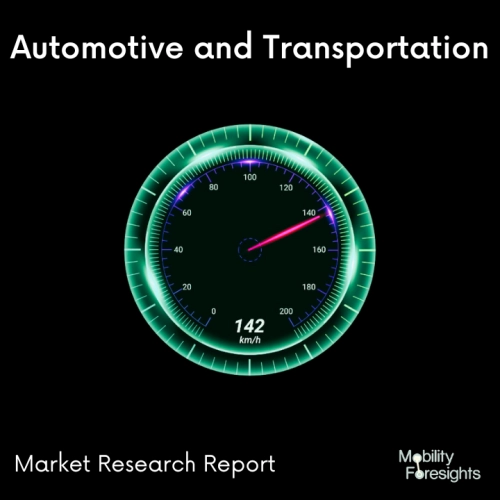
- Get in Touch with Us
Last Updated: Apr 25, 2025 | Study Period: 2024-2030
Before use, reactive hot melt adhesives are heated and applied while still molten. The adhesive physically hardens as it cools, increasing its initial green strength. The glue subsequently turns into an elastomer as a result of a chemical process that is started by water molecules from the substrate or the air.
Reactive hot melt adhesives offer a stronger bond with improved resistance to moisture, heat, and chemicals after complete crosslinking. The range of adhesion is substantially increased by the reactive groups in the adhesive also forming potent (covalent) chemical interactions with appropriate reactive partners on the surface of the substrate.
Reactive hot melt adhesive made of polyurethane and polyolefin is offered by Jowat in a variety of supply forms. Additionally, a new unfilled, high-performance PUR adhesive is also available in granulate form to meet the highest standards of quality and appearance.
Reactive hot melt adhesives are more necessary than ever because of their exceptional strength and adaptability. Polyurethane (PUR) hot melts and silane-modified polyolefin (POR) adhesives are both considered reactive hot melt gluers.
Many industries, including the automobile industry, electronics, and construction, use both reactive hot melt adhesive varieties. In this post, we'll concentrate on hot melt gluers for assembly and maintenance in the automotive sector.
Hot melts that react to moisture are often referred to as moisture-curing hot melts. This means that the hot melt glue reacts with moisture in the air and the substrate to attain its final cure. The two-stage curing profile of these adhesives separates the process into physical and chemical curing.
Even on surfaces that have been deemed "un-glueable," reactive hot melt adhesives are a high-quality car glue and may be used in a variety of applications. The automotive adhesives are quite light, which helps reduce the weight of the car. Additionally, they adhere to lightweight materials, which are essential in lighter automobiles.
As long as the proper hot melt dispenser is utilised, applying a hot melt gluer is also rather simple. Both of the two varieties polyurethane and silane-modified polyolefin-based systems have particular benefits of their own. PUR and PUR hot melt adhesives are a popular choice for many automotive adhesive applications due to their distinctive curing process.
The Global automotive Reactive Hot Melt Adhesives market accountedfor $XX Billion in 2021 and is anticipated to reach $XX Billion by 2030, registering a CAGR of XX% from 2024 to 2030.
A full variety of hot melt and reactive hot melt (RHM) products, including bonding and pressure-sensitive adhesive solutions, are available from H.B. Fuller. These products enable best-in-class process speeds and mileage.
Our products are 100% solids, so transportation expenses and energy use for solvent or water carriers that eventually evaporate and leave a considerably smaller percentage of solid adhesive are eliminated.
Additionally, your environmental goals will be supported by the fact that our hot melt adhesives normally emit no volatile organic compounds (VOCs) that need to be reported. Metals, plastics, glass, TPO, fabric, and leather are just a few of the materials that reactive hot melts adhere to very well.
They combine to create a strong, flexible bond that is resistant to chemicals, weather, and has a good moisture barrier and high-pressure sealing capacity.
Manufacturers are increasingly using Hot Melt Polyurethane Reactive (HMPUR) adhesive solutions instead of the more conventional Hot Melt Ethyl Vinyl Acetate (HMEVA) adhesive solutions because of their versatility and ability to bond to a variety of substrates.
The new generation product for edge banding applications is HMPUR adhesive solutions. It increases the endurance of completed woodworking goods and offers excellent bonding strength and sealing performance. It is also water resistant.
Due to their adaptability to different substrates, HMPUR adhesive solutions provide finished items with high-quality performance even in conditions with a lot of moisture. Because it improves workflow productivity and makes additional design options available, Bostik's HMPUR technology in the Supergrip 65 series is a great adhesive for the woodworking sector.
Sl no | Topic |
1 | Market Segmentation |
2 | Scope of the report |
3 | Abbreviations |
4 | Research Methodology |
5 | Executive Summary |
6 | Introduction |
7 | Insights from Industry stakeholders |
8 | Cost breakdown of Product by sub-components and average profit margin |
9 | Disruptive innovation in the Industry |
10 | Technology trends in the Industry |
11 | Consumer trends in the industry |
12 | Recent Production Milestones |
13 | Component Manufacturing in US, EU and China |
14 | COVID-19 impact on overall market |
15 | COVID-19 impact on Production of components |
16 | COVID-19 impact on Point of sale |
17 | Market Segmentation, Dynamics and Forecast by Geography, 2024-2030 |
18 | Market Segmentation, Dynamics and Forecast by Product Type, 2024-2030 |
19 | Market Segmentation, Dynamics and Forecast by Application, 2024-2030 |
20 | Market Segmentation, Dynamics and Forecast by End use, 2024-2030 |
21 | Product installation rate by OEM, 2023 |
22 | Incline/Decline in Average B-2-B selling price in past 5 years |
23 | Competition from substitute products |
24 | Gross margin and average profitability of suppliers |
25 | New product development in past 12 months |
26 | M&A in past 12 months |
27 | Growth strategy of leading players |
28 | Market share of vendors, 2023 |
29 | Company Profiles |
30 | Unmet needs and opportunity for new suppliers |
31 | Conclusion |
32 | Appendix |