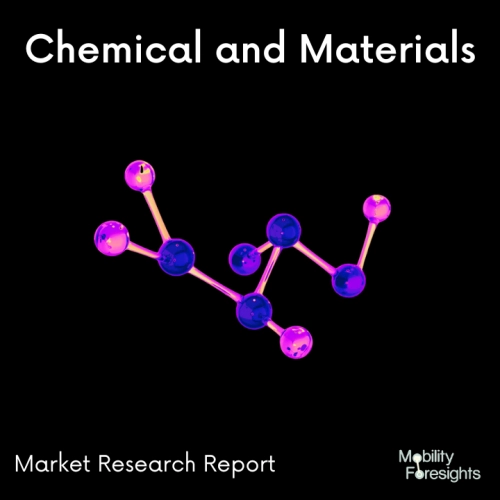
- Get in Touch with Us
Last Updated: Apr 25, 2025 | Study Period: 2024-2030
Automotive Super-Engineering Plastics (SEPs) is a group of high-performance plastic materials that offer superior mechanical, thermal, and chemical properties compared to conventional plastics.
These properties are beneficial in the automotive industry which requires lighter, stronger materials to reduce weight and costs. In addition, SEPs are able to sustain higher temperatures and resist abrasion better than conventional plastics.
Most automotive applications of SEPs involve components made from polymers such as polyphenylene sulfide (PPS), polyethersulfone (PES) and polyphthalamide (PPA). These high-performance plastics provide excellent stiffness, heat and chemical resistance, good strength, and excellent dimensional stability.
Some of the key advantages of these engineered plastics include the fact that they are lighter than traditional alternative materials like metals, they are non corrosive, offer superior fatigue resistance, and are easy to machine and mold.
SEPs are used in numerous components for cars, such as under-the-hood parts like fuel systems, transmission systems, and engine components.
They are also used in interior components like instrument panels, interior trim pieces, storage bins, and speaker grilles. Automotive SEPs also find use in parts of bodywork such as fenders, hoods, bumpers, grills and headlamps.
These plastics ease manufacturing costs by providing excellent dimensional stability and easy molding, and help to reduce assembly times.
The Global Automotive super engineering plastics market accounted for $XX Billion in 2023 and is anticipated to reach $XX Billion by 2030, registering a CAGR of XX% from 2024 to 2030.
Japanese engineering thermoplastics provider Polyplastics introduced a brand-new, high-performance engineering thermoplastic together with a cutting-edge sustainability programme.A cutting-edge material for metal replacement and applications needing the most heat resistance of any injection moldable resin without post-curing will be made available by Polyplastics: Sar Pek polyetherketone (PEK).
An improvement over polyetheretherketone (PEEK), Sar pek PEK is an engineering plastic with a high crystallisation rate and higher moulding efficiency that sits at the top of the crystalline super engineering plastic hierarchy, according to Polyplastics. It can also be used to replace metal in abrasive situations where other crystalline super-engineering polymers might break down due to its strength and tolerance to heat.
A new sustainability project has also been launched by Polyplastics' parent firm Daicel Corp. under the brand name Cafblo. For injection moulding and extrusion applications, the novel bioplastic is a non-edible biomass cellulose acetate resin.
This novel cellulose acetate resin is transparent, clear, and biodegradable in marine environments. Cafblo supposedly exhibits well-balanced mechanical and thermal properties comparable to acrylonitrile-
butadiene- styrene (ABS), in contrast to usual bioplastics like polylactic acid (PLA). But since Cafblo absorbs moisture, pre-drying is required before moulding. The ingredients of Cafblo are biodegradable plasticizers, cellulose acetate, and acetic acid. Polyplastics state that in seawater, these substances undergo biodegradation by microorganisms, ultimately yielding carbon dioxide and water.
Strong antibacterial activity of Cafblo resins has also been demonstrated against Escherichia coli and Staphylococcus aureus. The fused deposition modelling (FDM) method, which can print large-scale parts, is one of the many applications for which Cafblo is intended.
Comparatively speaking to other biodegradable resins, the bioplastic can be recycled several times with little loss of physical properties with frequent moulding. Although the Cafblo XDN grades are still being developed, Cafblo EC 210 is now available commercially. A new grade designed for 3D printing is also being developed; commercial grades are optimised for injection moulding.
Sl no | Topic |
1 | Market Segmentation |
2 | Scope of the report |
3 | Abbreviations |
4 | Research Methodology |
5 | Executive Summary |
6 | Introduction |
7 | Insights from Industry stakeholders |
8 | Cost breakdown of Product by sub-components and average profit margin |
9 | Disruptive innovation in the Industry |
10 | Technology trends in the Industry |
11 | Consumer trends in the industry |
12 | Recent Production Milestones |
13 | Component Manufacturing in US, EU and China |
14 | COVID-19 impact on overall market |
15 | COVID-19 impact on Production of components |
16 | COVID-19 impact on Point of sale |
17 | Market Segmentation, Dynamics and Forecast by Geography, 2023-2030 |
18 | Market Segmentation, Dynamics and Forecast by Product Type, 2023-2030 |
19 | Market Segmentation, Dynamics and Forecast by Application, 2023-2030 |
20 | Market Segmentation, Dynamics and Forecast by End use, 2023-2030 |
21 | Product installation rate by OEM, 2023 |
22 | Incline/Decline in Average B-2-B selling price in past 5 years |
23 | Competition from substitute products |
24 | Gross margin and average profitability of suppliers |
25 | New product development in past 12 months |
26 | M&A in past 12 months |
27 | Growth strategy of leading players |
28 | Market share of vendors, 2023 |
29 | Company Profiles |
30 | Unmet needs and opportunity for new suppliers |
31 | Conclusion |
32 | Appendix |