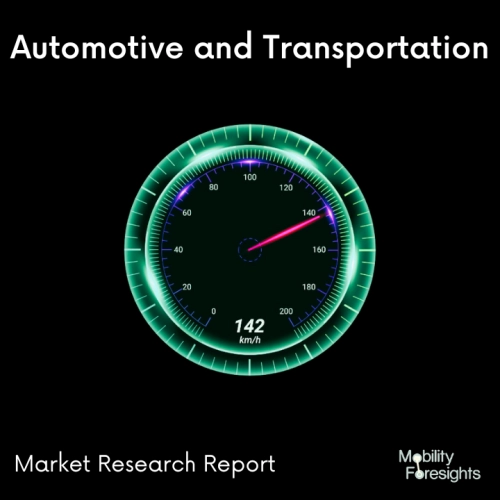
- Get in Touch with Us
Last Updated: Apr 25, 2025 | Study Period: 2023-2030
The reliability of ECUs can be increased by using automatic transfer molding using the transfer method, a tried-and-true approach for semiconductor packages.
Semiconductors have been sealed using the transfer approach for a very long time. When an ECU is placed on a mold and a melted thermosetting resin is poured inside of it, it can be covered and sealed with a resin to achieve reliability that is equal to that of semiconductor packages.
For this sealing process, the same tools and technology that are utilized for semiconductor packages can be used.
Additionally, enough information about resins used for sealing has been gathered through semiconductor packages. So, without doing a fresh, extensive evaluation, ECUs can be sealed with stable quality.
Compression molding may be employed instead of transfer molding if the ECU gains function, grows in size, and consumes a lot of resin.By carefully and gently lowering the ECU into the mold after injecting the liquid resin into the mold, the ECU can be properly molded using the compression method.
Additionally, the compression method works well when you don't want to put too much pressure or weight on sensitive ECU built-in parts.The compression technique was invented by TOWA, and we think that it will be helpful for packaging future ECUs that are more sophisticated.
The Global Automotive Transfer Mold ECU market accounted for $XX Billion in 2022 and is anticipated to reach $XX Billion by 2030, registering a CAGR of XX% from 2023 to 2030.
In resin automotive transfer molding (RTM), a fiber preform is placed in a closed mold and saturated with a liquid thermoset resin. The technique is adaptable and can create products with incorporated elements other than the fiber preform, such as foam cores or other materials.
Transfer molding with resin assisted by vacuum Vacuum assisted transfer molding (VARTM) pulls the resin in for full saturation by applying a partial vacuum to one side of a fiber mat. Lower plunger forces used by VARTM enable molding to be done with less expensive machinery.
The resin may be suitably able to flow and/or cure without heating if a vacuum is used. Thick fiber preforms and larger product geometries are made feasible by this temperature independence. VARTM is able to create components with reduced porosity than standard
Sl no | Topic |
1 | Market Segmentation |
2 | Scope of the report |
3 | Abbreviations |
4 | Research Methodology |
5 | Executive Summary |
6 | Introduction |
7 | Insights from Industry stakeholders |
8 | Cost breakdown of Product by sub-components and average profit margin |
9 | Disruptive innovation in the Industry |
10 | Technology trends in the Industry |
11 | Consumer trends in the industry |
12 | Recent Production Milestones |
13 | Component Manufacturing in US, EU and China |
14 | COVID-19 impact on overall market |
15 | COVID-19 impact on Production of components |
16 | COVID-19 impact on Point of sale |
17 | Market Segmentation, Dynamics and Forecast by Geography, 2023-2030 |
18 | Market Segmentation, Dynamics and Forecast by Product Type, 2023-2030 |
19 | Market Segmentation, Dynamics and Forecast by Application, 2023-2030 |
20 | Market Segmentation, Dynamics and Forecast by End use, 2023-2030 |
21 | Product installation rate by OEM, 2023 |
22 | Incline/Decline in Average B-2-B selling price in past 5 years |
23 | Competition from substitute products |
24 | Gross margin and average profitability of suppliers |
25 | New product development in past 12 months |
26 | M&A in past 12 months |
27 | Growth strategy of leading players |
28 | Market share of vendors, 2023 |
29 | Company Profiles |
30 | Unmet needs and opportunity for new suppliers |
31 | Conclusion |
32 | Appendix |