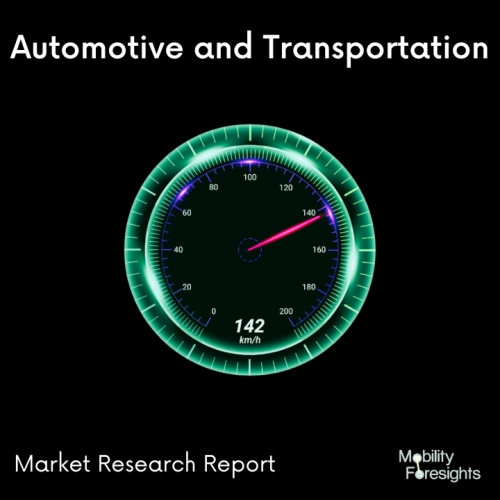
- Get in Touch with Us
Last Updated: Apr 25, 2025 | Study Period: 2024-2030
Automotive windshield bonding adhesives are materials used to attach a windshield or other safety glass elements to a vehicle. The bonding material is a specialized type of automotive adhesive and must meet stringent strength, safety, and environmental standards.
Automotive windshield adhesives are critical in automotive safety because they provide a secure bond to keep the windshield and other safety glass elements in place during accidents and other types of impacts.
Automotive windshield adhesives are usually a two-part epoxy that is mixed and then applied to the windshield or glass to be bonded. The adhesive can then be hardened or cured with ultraviolet light or heat in order to ensure a strong, secure bond.
Automotive windshield adhesives must meet a variety of safety standards, including standards for strength, water-resistance, and thermal and weathering resistance. They must also meet environmental standards, such as low-VOC and low-emission requirements.
In addition, automotive windshield adhesives must be approved for use in a particular type of vehicle by the vehicle manufacturer.
The use of automotive windshield adhesives is becoming increasingly popular due to its strength and reliability. It is also becoming popular as an alternative to the traditional mechanical bonding methods, such as between panel bonded and surface bonded methods.
By using adhesive instead of mechanical bonds, automotive manufacturers are able to reduce manufacturing costs while ensuring a reliable product.
The Global Automotive windshield bonding adhesives market accounted for $XX Billion in 2023 and is anticipated to reach $XX Billion by 2030, registering a CAGR of XX% from 2024 to 2030.
For EV battery systems, Henkel introduces a new injectable thermally conductive adhesive. Henkel Adhesive Technologies, a leader in automotive adhesives, sealants, thermal materials, and functional coatings worldwide, is committed to assisting OEMs and battery manufacturers in resolving issues so that the shift to zero-emission mobility can proceed more quickly.
Henkel has therefore expanded its wide range of EV battery system solutions with an injectable thermally conductive adhesive, a first for the industry. In the battery system, the new adhesive Loctite TLB 9300 APSi offers thermal conductivity in addition to structural bonding. The innovative product has already been embraced by one of the biggest producers of EV batteries worldwide.
Having a moderate viscosity, a high thermal conductivity of 3 W/mK, and self-leveling properties, Loctite TLB 9300 APSi is a two-component polyurethane thermally conductive adhesive that is ideal for bonding battery cells to cooling systems or modules.
It offers a special combination of strong bonding performance and good electrical insulation to a range of substrates in addition to its heat management capabilities. Since it cures at room temperature without requiring extra energy, this solvent-free solution helps customers meet their sustainability goals by lowering emissions and resource consumption and guaranteeing safer working conditions.
The Loctite TLB 9300 APSi is evidence of Henkel's ongoing efforts to develop novel e-mobility solutions that address current battery manufacturing issues and facilitate tomorrow's next-generation designs. The fact that a significant battery manufacturer adopted it right away shows how closely we work with important e-mobility industry players to drive change.
Henkel's extensive knowledge and experience in the crucial field of thermal interface materials for EV battery systems, which are essential to the development of safer and more efficient EVs, is further demonstrated by Loctite TLB 9300 APSi. The novel injectable thermally conductive adhesive boasts a simplified manufacturing process because of its precise application, increased design flexibility, and improved bond strength.
Sl no | Topic |
1 | Market Segmentation |
2 | Scope of the report |
3 | Abbreviations |
4 | Research Methodology |
5 | Executive Summary |
6 | Introduction |
7 | Insights from Industry stakeholders |
8 | Cost breakdown of Product by sub-components and average profit margin |
9 | Disruptive innovation in the Industry |
10 | Technology trends in the Industry |
11 | Consumer trends in the industry |
12 | Recent Production Milestones |
13 | Component Manufacturing in US, EU and China |
14 | COVID-19 impact on overall market |
15 | COVID-19 impact on Production of components |
16 | COVID-19 impact on Point of sale |
17 | Market Segmentation, Dynamics and Forecast by Geography, 2024-2030 |
18 | Market Segmentation, Dynamics and Forecast by Product Type, 2024-2030 |
19 | Market Segmentation, Dynamics and Forecast by Application, 2024-2030 |
20 | Market Segmentation, Dynamics and Forecast by End use, 2024-2030 |
21 | Product installation rate by OEM, 2024 |
22 | Incline/Decline in Average B-2-B selling price in past 5 years |
23 | Competition from substitute products |
24 | Gross margin and average profitability of suppliers |
25 | New product development in past 12 months |
26 | M&A in past 12 months |
27 | Growth strategy of leading players |
28 | Market share of vendors, 2024 |
29 | Company Profiles |
30 | Unmet needs and opportunity for new suppliers |
31 | Conclusion |
32 | Appendix |