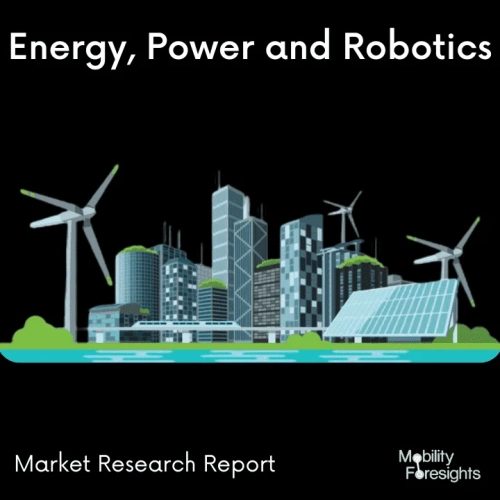
- Get in Touch with Us
Last Updated: Jul 14, 2025 | Study Period: 2025-2031
Basic petrochemicals are the foundational building blocks of the chemical industry, derived mainly from crude oil and natural gas through processes like steam cracking and catalytic reforming.
Key products include ethylene, propylene, benzene, toluene, xylene, methanol, and butadiene—used to manufacture plastics, synthetic fibers, solvents, and resins.
Global demand is strongly linked to economic growth and urbanization, particularly in sectors like automotive, packaging, construction, and electronics.
The market is shifting geographically, with Asia-Pacific—especially China and India—emerging as production and consumption hubs.
Advancements in shale gas processing and NGL (Natural Gas Liquids) extraction are significantly altering feedstock economics, particularly in North America.
Environmental scrutiny and decarbonization targets are pushing the industry to explore bio-based alternatives, carbon capture, and circular petrochemical models.
Integration with refineries and chemical parks offers economies of scale, while digital technologies are optimizing plant operations and predictive maintenance.
Key producers include SABIC, ExxonMobil, Shell, Dow, LyondellBasell, and INEOS.
Regulatory developments in Europe and increasing sustainability pressure in Asia are reshaping long-term investment plans.
Global capacity additions are expected from mega-complexes being built in the Middle East, Southeast Asia, and the U.S. Gulf Coast.
The basic petrochemical market serves as the cornerstone of the modern industrial economy, supplying the essential chemicals that are further processed into thousands of downstream products. These petrochemicals are primarily derived from naphtha, natural gas, and light hydrocarbons, and are used to produce polymers, synthetic rubbers, agrochemicals, and performance materials.
Ethylene and propylene alone account for the majority of global demand, owing to their use in polyethylene and polypropylene production. Benzene, toluene, and xylene are vital for making aromatics and intermediates for dyes, resins, and detergents. Methanol and butadiene support a broad array of applications in energy, adhesives, and automotive elastomers.
While mature markets are undergoing restructuring due to sustainability pressures, developing economies are experiencing strong demand growth, particularly in packaging, construction materials, and consumer durables. The market is capital-intensive and cyclical, with margins influenced heavily by feedstock prices and global economic conditions.
The global basic petrochemical market was valued at USD 630.4 billion in 2024 and is projected to reach USD 910.7 billion by 2031, growing at a CAGR of 5.4% during the forecast period.
This growth is underpinned by rising demand for synthetic polymers, resins, elastomers, and industrial solvents in fast-growing economies. In particular, ethylene and propylene are witnessing strong uptake across packaging, automotive, and infrastructure sectors. Additionally, the resurgence of downstream manufacturing post-pandemic has led to capacity expansions and increased throughput.
Feedstock dynamics continue to play a central role. The North American market benefits from low-cost ethane derived from shale gas, while Asia-Pacific is largely naphtha-dependent, prompting feedstock diversification and energy efficiency upgrades. Global players are also actively investing in circular economy initiatives such as plastic recycling and bio-petrochemicals to mitigate environmental impact.
The future of the basic petrochemical market is expected to be shaped by a dual imperative: meeting growing material demand while significantly reducing environmental impact. As a result, companies are investing in carbon capture and utilization (CCU), electrification of steam crackers, and chemical recycling of plastics.
Asia-Pacific will continue to dominate global production and consumption, but regional players must navigate challenges related to overcapacity and sustainability mandates. In the Middle East and the U.S., integrated refinery-petrochemical complexes are being expanded to improve downstream economics and supply chain resilience.
Technologies such as digital twins, predictive analytics, and process optimization will become central to competitiveness. Moreover, bio-feedstocks, hydrogen-based synthesis routes, and regulatory-backed circular initiatives will play an increasingly important role over the next decade.
The market will also see a gradual transformation in product mix, with greater emphasis on specialty chemicals, low-carbon intermediates, and green polyolefins.
Feedstock Diversification and Shale Gas Influence:
The emergence of shale gas as a low-cost feedstock in North America has significantly reshaped global competitiveness in ethylene and methanol production. As more countries seek to reduce reliance on naphtha, new technologies and sourcing strategies for feedstock flexibility are gaining traction. This trend is enabling operators to optimize cost structures and expand profit margins.
Circular Economy and Plastic Recycling Integration:
The industry is increasingly embracing closed-loop systems by investing in mechanical and chemical recycling processes. Circular petrochemicals derived from post-consumer plastic waste are gaining policy and investor support, especially in Europe. Leading companies are launching pilot projects for pyrolysis oil and depolymerization to reintroduce materials into existing cracker systems.
Sustainability-Driven Innovations:
Environmental regulations and net-zero commitments are driving R&D into carbon capture-integrated crackers, renewable methanol synthesis, and bio-aromatics. Companies like BASF and Dow are testing electrically heated steam crackers to drastically cut emissions. Sustainability is no longer optional but a competitive necessity in long-term strategy.
Digitalization and Smart Operations:
The deployment of advanced analytics, remote sensing, and AI-driven process control is transforming operational reliability and throughput. Predictive maintenance, real-time emissions monitoring, and digital twins are being implemented across facilities to reduce unplanned downtime and improve energy efficiency.
Growing Demand from Plastics and Packaging Sectors:
Polyethylene, polypropylene, and PET demand is rising due to increased consumption of flexible packaging, e-commerce logistics, and consumer durables. Basic petrochemicals are core to these polymers, making them indispensable in everyday products ranging from containers to textiles.
Infrastructure and Automotive Sector Expansion:
Construction booms in developing economies and the recovery of the automotive sector post-COVID are fueling demand for resins, elastomers, and adhesives derived from base chemicals. Urbanization and smart city initiatives are further driving volume consumption of synthetic materials and intermediates.
Integration with Refinery and Chemical Complexes:
Vertical integration between refining and petrochemical operations offers economies of scale and enhances product value chains. Mega-complexes in the Middle East, India, and China are optimizing shared utilities, reducing logistical costs, and increasing production flexibility for multiple chemical streams.
Low-Cost Feedstock Access and Strategic Investments:
The availability of low-cost natural gas and condensates in regions like North America and the Middle East is incentivizing large-scale investments. Companies are expanding ethane crackers, methanol-to-olefins plants, and propane dehydrogenation units to capitalize on regional feedstock advantages.
Environmental Regulations and Emissions Pressure:
Stringent emissions norms, plastic bans, and ESG expectations are increasing the compliance burden. Many petrochemical plants face rising costs to upgrade infrastructure, adopt low-carbon technologies, and manage lifecycle impacts of their products.
Feedstock Price Volatility and Supply Chain Disruptions:
Fluctuating crude oil and natural gas prices introduce unpredictability in input costs, affecting downstream margins. Geopolitical instability, OPEC decisions, and logistical disruptions like port congestion can destabilize global supply chains and project economics.
Overcapacity Risks in Asia-Pacific:
The rapid buildup of petrochemical capacity in China and Southeast Asia has raised concerns about oversupply and margin compression. Several large complexes have come online simultaneously, creating regional price pressure and increasing reliance on exports for profitability.
Technological Obsolescence and Transition Costs:
The shift toward green and digital technologies requires significant CAPEX and organizational change. Legacy plants with inefficient setups are at risk of becoming stranded assets unless modernized or repurposed for low-carbon operations.
Ethylene
Propylene
Benzene
Toluene
Xylenes
Methanol
Butadiene
Naphtha
Natural Gas Liquids (NGLs)
Ethane
Propane
Bio-based Feedstocks
Plastics and Polymers
Solvents and Intermediates
Synthetic Fibers and Elastomers
Adhesives and Coatings
Agrochemicals
Detergents
Packaging
Automotive
Construction
Textiles
Pharmaceuticals
Electronics
North America
Europe
Asia-Pacific
Latin America
Middle East & Africa
SABIC
ExxonMobil Chemical
LyondellBasell Industries
Shell Chemicals
Dow Inc.
INEOS Group
BASF SE
Reliance Industries
Sinopec
Formosa Plastics Corporation
SABIC partnered with BASF and Linde to test a fully electrified steam cracker pilot in Germany, aimed at reducing emissions from ethylene production.
Reliance Industries signed a joint venture with ADNOC to develop an integrated petrochemical facility in Ruwais, UAE.
INEOS expanded its agreement with Sinopec to include investments in high-value propylene and polyethylene production lines in China.
Dow launched a circular feedstock partnership with Mura Technology to scale advanced recycling in the U.S. and Europe.
Shell signed a multi-year agreement with Air Liquide for CO₂ capture from its petrochemical operations in Canada.
How many Basic Petrochemicals are manufactured per annum globally? Who are the sub-component suppliers in different regions?
Cost Breakdown of a Global Basic Petrochemical and Key Vendor Selection Criteria
Where is the Basic Petrochemical manufactured? What is the average margin per unit?
Market share of Global Basic Petrochemical market manufacturers and their upcoming products
Cost advantage for OEMs who manufacture Global Basic Petrochemical in-house
Key predictions for next 5 years in the Global Basic Petrochemical market
Average B2B Basic Petrochemical market price in all segments
Latest trends in the Basic Petrochemical market, by every market segment
The market size (both volume and value) of the Basic Petrochemical market in 2025–2031 and every year in between
Production breakup of the Basic Petrochemical market, by suppliers and their OEM relationship
Sl no | Topic |
1 | Market Segmentation |
2 | Scope of the report |
3 | Research Methodology |
4 | Executive summary |
5 | Key Predictions of Basic Petrochemical Market |
6 | Avg B2B price of Basic Petrochemical Market |
7 | Major Drivers For Basic Petrochemical Market |
8 | Global Basic Petrochemical Market Production Footprint - 2024 |
9 | Technology Developments In Basic Petrochemical Market |
10 | New Product Development In Basic Petrochemical Market |
11 | Research focus areas on new Basic Petrochemical |
12 | Key Trends in the Basic Petrochemical Market |
13 | Major changes expected in Basic Petrochemical Market |
14 | Incentives by the government for Basic Petrochemical Market |
15 | Private investements and their impact on Basic Petrochemical Market |
16 | Market Size, Dynamics And Forecast, By Type, 2025-2031 |
17 | Market Size, Dynamics And Forecast, By Output, 2025-2031 |
18 | Market Size, Dynamics And Forecast, By End User, 2025-2031 |
19 | Competitive Landscape Of Basic Petrochemical Market |
20 | Mergers and Acquisitions |
21 | Competitive Landscape |
22 | Growth strategy of leading players |
23 | Market share of vendors, 2024 |
24 | Company Profiles |
25 | Unmet needs and opportunities for new suppliers |
26 | Conclusion |