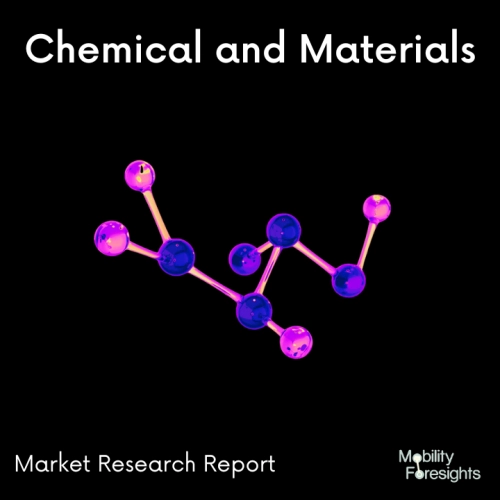
- Get in Touch with Us
Last Updated: Apr 25, 2025 | Study Period: 2024-2030
Battery grade transparent coating is a type of coating used on lithium ion batteries to improve their performance and extend their life. The coating is designed to provide an extra layer of protection against moisture, dust, oxidation and other damaging elements. It also helps to reduce the amount of energy lost through heat dissipation.
Battery grade transparent coating is usually applied to the exterior layer of the battery, as this allows it to be applied in a thin, uniform layer. This helps to ensure that the coating provides maximum protection without adding excessive weight or volume. Additionally, the coating is transparent, allowing for easy visual inspection of the battery's condition.
The primary benefit of applying this type of coating to lithium ion batteries is that it helps to extend the life of the battery. In particular, it can help to prevent premature aging caused by oxidation and other environmental factors.
Additionally, the coating helps to reduce the amount of energy lost through heat dissipation. This can help to improve the overall efficiency of the battery and increase its lifespan.
Overall, battery grade transparent coating is an effective way to protect lithium ion batteries and extend their life. By protecting the battery from the damaging effects of oxidation and heat dissipation, it can help to ensure that the battery remains in good condition and performs reliably for an extended period of time. Additionally, the transparent nature of the coating allows for easy visual inspection of the battery's condition.
The Global Battery Grade Transparent Coating market accounted for $XX Billion in 2022 and is anticipated to reach $XX Billion by 2030, registering a CAGR of XX% from 2024 to 2030.
In order to showcase its patented alumina coating process for battery materials, Altech has enlisted the German engineering company Kuttner GmbH & Co. to build the pilot facility in Germany.
The anode grade coated battery material produced by the pilot plant can reach a maximum annual production capacity of 36,680 kg (120 kg/day). The pilot plant design is meant to be installed in the Dock3 building, which is next to Altech's assigned location at Schwarze Pumpe Industrial Park.
In the Dock3, where the prototype plant will be situated, Altech has obtained about 300 square metres of floor space. Additionally, the pilot facility will have an analytical laboratory on site.
The lab will provide speedy evaluation of the purity of the product from the pilot plant and physical parameter monitoring, allowing for quick adjustments to processing parameters and operational setpoints when needed.
Office space for the project and operations team is included in the Dock3 facility, which is already connected to all necessary utilities.The two main processing areas of the pilot plant design are the coating and calcination of battery material and the manufacturing of precursors.
The apparatus used for precursor manufacture must be run in batch mode, yielding about 10 kg per batch. The output is enough to provide the downstream anode material coating stage for about thirty hours of nonstop operation.
With two European providers of anode materials suitable for lithium-ion batteries, Altech has signed two Memorandums of Understandings (MoUs). Altech and SGL Carbon GmbH (SGL), one of the top producers of graphite in Europe, have signed a memorandum of understanding (MoU) to that effect.
In order to meet the needs of the lithium-ion (Li-ion) battery industry, SGL Carbon is helping Altech create high purity alumina coated graphite products. Furthermore described in the Memorandum of Understanding is the prospective future cooperation in which SGL would provide AIG's battery materials plant in Saxony with uncoated synthetic graphite anode material. The PFS financial model shall incorporate the non-binding, indicative volumes and pricing specified in the Memorandum of Understanding
Sl no | Topic |
1 | Market Segmentation |
2 | Scope of the report |
3 | Abbreviations |
4 | Research Methodology |
5 | Executive Summary |
6 | Introduction |
7 | Insights from Industry stakeholders |
8 | Cost breakdown of Product by sub-components and average profit margin |
9 | Disruptive innovation in the Industry |
10 | Technology trends in the Industry |
11 | Consumer trends in the industry |
12 | Recent Production Milestones |
13 | Component Manufacturing in US, EU and China |
14 | COVID-19 impact on overall market |
15 | COVID-19 impact on Production of components |
16 | COVID-19 impact on Point of sale |
17 | Market Segmentation, Dynamics and Forecast by Geography, 2024-2030 |
18 | Market Segmentation, Dynamics and Forecast by Product Type, 2024-2030 |
19 | Market Segmentation, Dynamics and Forecast by Application, 2024-2030 |
20 | Market Segmentation, Dynamics and Forecast by End use, 2024-2030 |
21 | Product installation rate by OEM, 2023 |
22 | Incline/Decline in Average B-2-B selling price in past 5 years |
23 | Competition from substitute products |
24 | Gross margin and average profitability of suppliers |
25 | New product development in past 12 months |
26 | M&A in past 12 months |
27 | Growth strategy of leading players |
28 | Market share of vendors, 2023 |
29 | Company Profiles |
30 | Unmet needs and opportunity for new suppliers |
31 | Conclusion |
32 | Appendix |