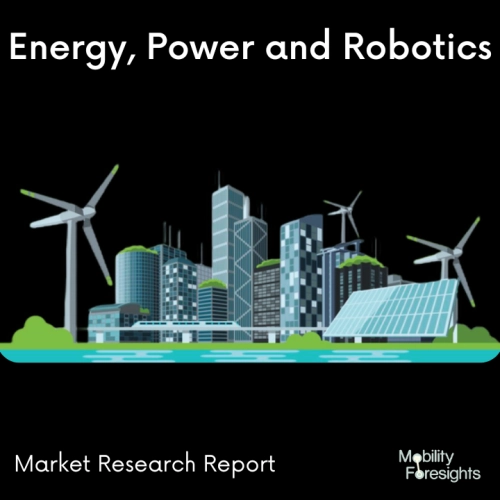
- Get in Touch with Us
Last Updated: Apr 25, 2025 | Study Period: 2023-2030
Defects, pollutants, functional flaws, and other anomalies in manufactured goods are found using a Battery Pack Vision Inspection Machine for inspection. Examples include checking medication tablets for faults, displays to confirm the presence of pixels or icons, or touch screens to gauge the amount of backlight contrast.
Battery Pack Vision Inspection Machine may also examine products for completeness, such as checking bottle safety seals, caps, and rings, and ensuring that the product and package match in the food and pharmaceutical industries.
Inspection-focused Battery Pack Vision Inspection Machines keep an eye on the material under observation's outward appearance. The method automatically locates probable flaws in the material's surface using statistical analysis, and it clusters the flaws depending on how similar they are in contrast, texture, and/or shape.
The Global Battery Pack Vision Inspection Machine market accounted for $XX Billion in 2022 and is anticipated to reach $XX Billion by 2030, registering a CAGR of XX% from 2023 to 2030.
An automated system to check constructed battery packs was required by the customer. In order to make the most of the lengthy process time and minimize any increase in current cycle times Mesh Automation Inc,Battery Pack Vision Inspection Machine was created to be linked with an already-existing robot cell.
An overhead camera system took photographs of the pack and checked to see if components were there and in the right places while the robot was engaged with other activities.
If the packs were in good condition, the robot would approach and finish the process; however, if any parts were missing, an operator would be notified and given the choice of either manually repairing the pack in the cell or releasing it and sending it to a holding area for additional examination. In less than 60 seconds, the vision inspection might identify whether a pack was good or not.
The following is a list of some of the elements the system searched for.Bolts: Present/Not Present,Location and existence of the cable and bracket,Locating the connector,Automation Resources,ABB robot is controlled by Keyence 21MP camera XG-X Vision Controller Allen-Bradley.
Performance of the Vision System,Execution time of the vision: 60 seconds,Size of the pack: 50" long by 32" wide,Expected Utilization: 24 hours/day, 7 days/week,Availability of equipment: > 85%.
Sl no | Topic |
1 | Market Segmentation |
2 | Scope of the report |
3 | Abbreviations |
4 | Research Methodology |
5 | Executive Summary |
6 | Introdauction |
7 | Insights from Industry stakeholders |
8 | Cost breakdown of Product by sub-components and average profit margin |
9 | Disruptive innovation in theIndustry |
10 | Technology trends in the Industry |
11 | Consumer trends in the industry |
12 | Recent Production Milestones |
13 | Component Manufacturing in US, EU and China |
14 | COVID-19 impact on overall market |
15 | COVID-19 impact on Production of components |
16 | COVID-19 impact on Point of sale |
17 | Market Segmentation, Dynamics and Forecast by Geography, 2023-2030 |
18 | Market Segmentation, Dynamics and Forecast by Product Type, 2023-2030 |
19 | Market Segmentation, Dynamics and Forecast by Application, 2023-2030 |
20 | Market Segmentation, Dynamics and Forecast by End use, 2023-2030 |
21 | Product installation rate by OEM, 2023 |
22 | Incline/Decline in Average B-2-B selling price in past 5 years |
23 | Competition from substitute products |
24 | Gross margin and average profitability of suppliers |
25 | New product development in past 12 months |
26 | M&A in past 12 months |
27 | Growth strategy of leading players |
28 | Market share of vendors, 2023 |
29 | Company Profiles |
30 | Unmet needs and opportunity for new suppliers |
31 | Conclusion |
32 | Appendix |