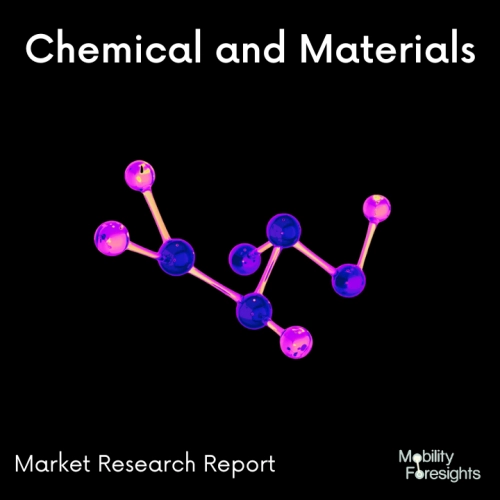
- Get in Touch with Us
Last Updated: Apr 25, 2025 | Study Period: 2024-2030
Beryllium Copper, commonly referred to as Beryllium Bronze or Spring Copper, is an alloy of copper containing 0.5â3% Beryllium as well as additional elements on occasion. The alloy has a high strength as well as non-magnetic and anti-sparking properties.
Applications including oilfield tools, aerospace landing gears, robotic welding, and mould building use beryllium copper and its diversity of alloys in extremely particular and frequently custom ways. For down-hole wire line tools, it is ideal due to additional non-magnetic qualities.
Pure copper is heated to a small amount of beryllium metal or oxide (BeO) powder in order to create a beryllium copper alloy. The mixture is then heated until it melts and creates an ingot that may then be further processed into various shapes and sizes as required by the application.
A high-strength alloy with non-magnetic and non-sparking characteristics, beryllium copper (BeCu) is an alloy that has undergone age-hardening. The highest strength of all copper-based alloys is achieved by adding 0.5% to 3% beryllium to copper.A copper alloy called beryllium copper contains beryllium, cobalt, nickel, iron, and lead in addition to copper.
These metals are added to copper to give beryllium copper (BeCu) many of its distinctive characteristics. There are no worldwide bans, restrictions, or other limitations on the use of copper beryllium or products containing beryllium.
The Global beryllium copper alloy market accounted for $XX Billion in 2023 and is anticipated to reach $XX Billion by 2030, registering a CAGR of XX% from 2024 to 2030.
In its newly built, vertically integrated, and expanded Indiana facility, IBC Advanced Alloys begins operations for copper alloy casting. A prominent manufacturer of beryllium and copper advanced alloys has begun copper alloy casting at its new and expanded copper alloy foundry facility in Franklin, Indiana.
The first successful pour of a two-ton beryllium-copper billet started the production of a range of copper alloy products in Indiana. With the beginning of production at the new plant, a two-year consolidation of three production sites into one vertically integrated manufacturing operation that is solely focused on producing copper and copper alloy products has effectively come to an end.
For the Copper Alloys Division, the consolidation is anticipated to result in considerable efficiencies and production cost savings that will allow the division to increase production and exposure.The first billet of the beryllium-copper alloy that was cast at the Franklin factory last week is on display by the IBC Copper Alloy Division team.
Now, this billet will be refined and created into specialized goods for IBC clients. At the newly expanded Franklin factory, the IBC team successfully produced multiple two-ton billets of beryllium-copper alloy material last week, including the first billet of beryllium-copper alloy shown to the right.
For customers in sectors like electronics, oil & gas, automotive, defense, aerospace, injection moulding, and others, IBC then processes these billets through cutting, forging, heat treating, and machining into a wide range of specialized alloy products.
It is a major milestone for IBC, and I am extremely proud of the entire Copper Alloys team for working so hard to successfully complete this strategic consolidation and expansion of their Franklin plant. They are overjoyed to witness the successful start-up of this expansion. It is the result of extensive planning and arduous work by the project manager.
"With this consolidation, a new era for Copper Alloys has begun, and the Board and they look forward to seeing the facility continue to ramp up to full-scale production as soon as possible."
IBC is a well-known manufacturer of innovative beryllium and copper alloys that are used in many different sectors, including aerospace, automotive, telecommunications, and precision manufacturing. Beryllium copper, chrome copper, and aluminium bronze are just a few of the copper alloys that IBC's Copper Division produces and distributes in the form of castings and forgings.
The Beralcast family of alloys, which may be precision cast and are utilized in an expanding variety of defence, aerospace, and other systems, including the F-35 Joint Strike Fighter, are produced by IBC's Engineered Materials Division. IBC Innovative Alloys Corp. is a well-known manufacturer of innovative beryllium and copper alloys that caters to numerous sectors.
They offer mission-critical alloys that support the mission-critical applications of our clients. Their mission is to deliver customer solutions employing cutting-edge metal alloys in order to alter the planet.
Their goal is to become the leader in the specialized alloys market by offering precise, cost- and purpose-conscious material solutions that are suited to the needs of their clients while also fostering an enjoyable workplace for their staff and adding value for their shareholders.
They offer a selection of copper alloys, such as beryllium copper, chrome copper, and aluminium bronze, as castings and forgings. The exclusive Beralcast material from Beryllium-Aluminium Castings IBC combines the high rigidity and light weight of beryllium with excellent manufacturing properties and low cost of aluminium.
Its high elastic modulus makes stable three-dimensional precision casting possible. It addresses the drawbacks of conventional powder metal beryllium aluminium products and pure beryllium products.
Sl no | Topic |
1 | Market Segmentation |
2 | Scope of the report |
3 | Abbreviations |
4 | Research Methodology |
5 | Executive Summary |
6 | Introduction |
7 | Insights from Industry stakeholders |
8 | Cost breakdown of Product by sub-components and average profit margin |
9 | Disruptive innovation in the Industry |
10 | Technology trends in the Industry |
11 | Consumer trends in the industry |
12 | Recent Production Milestones |
13 | Component Manufacturing in US, EU and China |
14 | COVID-19 impact on overall market |
15 | COVID-19 impact on Production of components |
16 | COVID-19 impact on Point of sale |
17 | Market Segmentation, Dynamics and Forecast by Geography, 2024-2030 |
18 | Market Segmentation, Dynamics and Forecast by Product Type, 2024-2030 |
19 | Market Segmentation, Dynamics and Forecast by Application, 2024-2030 |
20 | Market Segmentation, Dynamics and Forecast by End use, 2024-2030 |
21 | Product installation rate by OEM, 2023 |
22 | Incline/Decline in Average B-2-B selling price in past 5 years |
23 | Competition from substitute products |
24 | Gross margin and average profitability of suppliers |
25 | New product development in past 12 months |
26 | M&A in past 12 months |
27 | Growth strategy of leading players |
28 | Market share of vendors, 2023 |
29 | Company Profiles |
30 | Unmet needs and opportunity for new suppliers |
31 | Conclusion |
32 | Appendix |