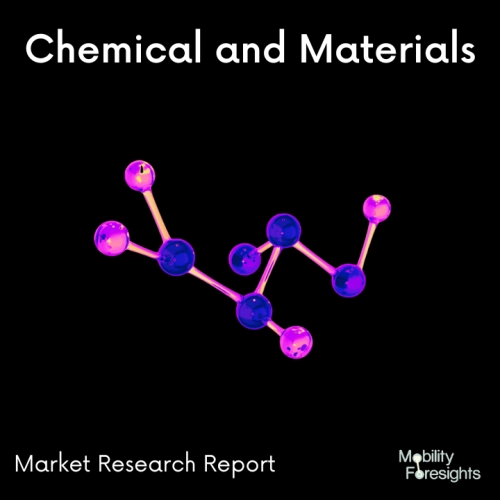
- Get in Touch with Us
Last Updated: Apr 25, 2025 | Study Period: 2024-2030
The production of closures for beverage containers like bottles, cans, and jars uses specialised moulds called beverage closure moulds. Screw caps, snap-on caps, and flip-top caps, which are used to seal the contents of beverage containers, are just a few examples of the closures that these moulds are made to produce in precise and consistent sizes and forms.
To ensure that the moulds fit the exact requirements of the beverage industry, beverage closure moulds are often built of premium materials like stainless steel or aluminium and are subject to stringent quality control standards.
In order to guarantee that the closures produced are of the highest calibre and dependability, these moulds are also made to endure the high heat and pressures involved with the injection moulding process.
Beverage closure moulds are used in the production of closures to increase consistency and efficiency, lower the possibility of faults, and enhance overall product quality.
The manufacture of bottle caps and closures for the beverage industry depends heavily on beverage closure moulds. Manufacturers frequently provide new products to fulfil the needs of their customers as the demand for creative packaging solutions rises.
The beverage closure molds accounted for $XX Billion in 2022 and is anticipated to reach $XX Billion by 2030, registering a CAGR of XX% from 2024 to 2030.
Sensors and monitoring systems are built into Smart Closure Molds to guarantee consistent quality and function throughout the manufacturing process.
Lightweight Closure Molds are created to manufacture lighter, more environmentally friendly bottle caps by using less material and increasing sustainability.
Drink Closure Systems by HyCAP Solutions for fully integrated systems that maximise productivity and user-friendliness. It has full turnkey solutions that have been tailored to boost efficiency.
It can increase part quality and cut down on waste. Cycle times might be up to 25% faster than those of other top injection moulding systems. Up to 20% less energy is being used. It has intelligence built in to guarantee dependable, repeatable performance and simplicity of use.
Sl no | Topic |
1 | Market Segmentation |
2 | Scope of the report |
3 | Abbreviations |
4 | Research Methodology |
5 | Executive Summary |
6 | Introduction |
7 | Insights from Industry stakeholders |
8 | Cost breakdown of Product by sub-components and average profit margin |
9 | Disruptive innovation in the Industry |
10 | Technology trends in the Industry |
11 | Consumer trends in the industry |
12 | Recent Production Milestones |
13 | Component Manufacturing in US, EU and China |
14 | COVID-19 impact on overall market |
15 | COVID-19 impact on Production of components |
16 | COVID-19 impact on Point of sale |
17 | Market Segmentation, Dynamics and Forecast by Geography, 2024-2030 |
18 | Market Segmentation, Dynamics and Forecast by Product Type, 2024-2030 |
19 | Market Segmentation, Dynamics and Forecast by Application, 2024-2030 |
20 | Market Segmentation, Dynamics and Forecast by End use, 2024-2030 |
21 | Product installation rate by OEM, 2023 |
22 | Incline/Decline in Average B-2-B selling price in past 5 years |
23 | Competition from substitute products |
24 | Gross margin and average profitability of suppliers |
25 | New product development in past 12 months |
26 | M&A in past 12 months |
27 | Growth strategy of leading players |
28 | Market share of vendors, 2023 |
29 | Company Profiles |
30 | Unmet needs and opportunity for new suppliers |
31 | Conclusion |
32 | Appendix |