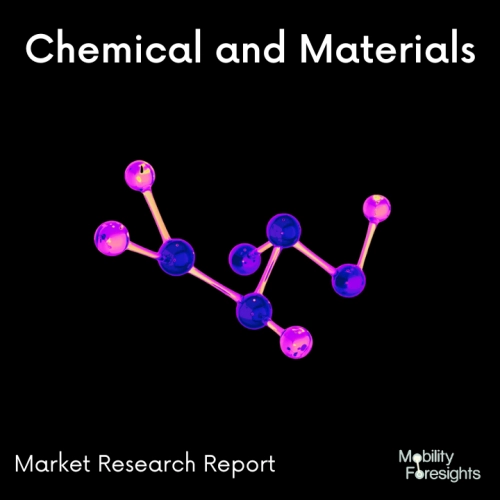
- Get in Touch with Us
Last Updated: Apr 25, 2025 | Study Period: 2024-2030
Stretched PET is converted into a polyester film called BoPET (biaxially-oriented polyethylene terephthalate), which is valued for its high tensile strength, chemical and dimensional stability, transparency, reflectivity, and ability to block gas and odours.
The method of biaxial orienting involves stretching a plastic film or sheet so that the polymeric chains are parallel to the plane of the film.
Film is created by extruding molten polyethylene terephthalate (PET) polymer onto a chill roll drum. The film is then stretched twice, once in the machine direction (MD) and once in the transverse direction, to create a biaxial orientation (TD).
Orientated polyethylene terephthalate is used to create the polyester film known as BOPET (Biaxially Oriented Polyethylene Terephthalate) (PET).
Its strong tensile strength, chemical and dimensional stability, transparency, reflectivity, gas and scent barrier qualities, and electrical insulation make BOPET a popular material.
The global biaxially oriented film PET resin market accounted for $XX Billion in 2023 and is anticipated to reach $XX Billion by 2030, registering a CAGR of XX% from 2024 to 2030.
A new polyester film called FLEXPET F-PGB-12 has been developed by the Indian flexible packaging business Uflex.
It minimises oxygen transmission while also displaying optical qualities and transparency. The novel 12 m bi-axially oriented polyethylene terephthalate (BOPET) film has an oxygen transmission-reducing surface modification on one side.
Depending on the converter's needs, the other side of the film can either be corona-treated or left untreated.
"This film offers a clear cost advantage to the converters over other PVDC / EVOH-coated / co-extruded films and is widely used in the packaging for pet foods; roasted coffee and other oxygen and barrier-sensitive food products," said assistant general manager of Uflex Technical Service and New Product Development (Films).
This low-cost specialty BOPET film is in great demand, and they are receiving a lot of business inquiries. At 23°C and 0% relative humidity, FLEXPET F-PGB-12 has an oxygen transmission rate (OTR) of less than 6 cm 3/m2/day (RH).
Comparing this film to comparable PVDC/EVOH-coated/co-extruded films, the converters can clearly see the economic advantage it provides.
According to the head of Uflex Technical and New Product Development (Films), newest film can function as a better oxygen barrier in a standard two-ply laminate while the sealant layer can be a fantastic moisture barrier.
This is the most straightforward cross section that one can imagine to keep the cost of converting to a minimum without sacrificing the performance of the laminate.
Sl no | Topic |
1 | Market Segmentation |
2 | Scope of the report |
3 | Abbreviations |
4 | Research Methodology |
5 | Executive Summary |
6 | Introduction |
7 | Insights from Industry stakeholders |
8 | Cost breakdown of Product by sub-components and average profit margin |
9 | Disruptive innovation in the Industry |
10 | Technology trends in the Industry |
11 | Consumer trends in the industry |
12 | Recent Production Milestones |
13 | Component Manufacturing in US, EU and China |
14 | COVID-19 impact on overall market |
15 | COVID-19 impact on Production of components |
16 | COVID-19 impact on Point of sale |
17 | Market Segmentation, Dynamics and Forecast by Geography, 2024-2030 |
18 | Market Segmentation, Dynamics and Forecast by Product Type, 2024-2030 |
19 | Market Segmentation, Dynamics and Forecast by Application, 2024-2030 |
20 | Market Segmentation, Dynamics and Forecast by End use, 2024-2030 |
21 | Product installation rate by OEM, 2023 |
22 | Incline/Decline in Average B-2-B selling price in past 5 years |
23 | Competition from substitute products |
24 | Gross margin and average profitability of suppliers |
25 | New product development in past 12 months |
26 | M&A in past 12 months |
27 | Growth strategy of leading players |
28 | Market share of vendors, 2023 |
29 | Company Profiles |
30 | Unmet needs and opportunity for new suppliers |
31 | Conclusion |
32 | Appendix |