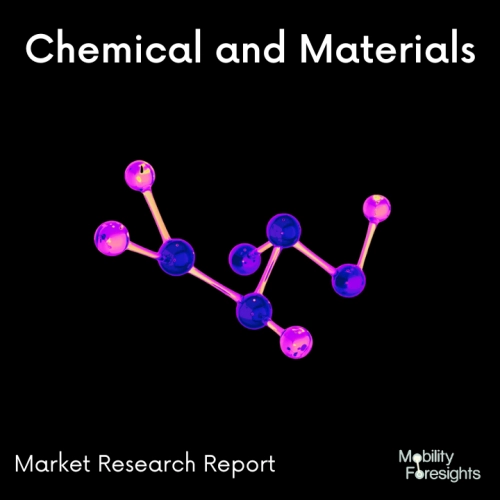
- Get in Touch with Us
Last Updated: Apr 25, 2025 | Study Period: 2024-2030
Synthetic fibers of the bicomponent nonwoven variety are used to make nonwoven fabrics. Nonwoven fabrics are manufactured by tying or gluing threads together rather than weaving or knitting them as is done in traditional textiles, creating sheet-like materials.
Two distinct polymer components, often with different melting temperatures or solubilities, are combined to form bicomponent fibers. These elements come together to form a single filament or fiber, which results in a structure with unique characteristics. The two halves can be positioned in many ways, such as side-by-side or in a core-sheath configuration.
For bicomponent fibers, the core-sheath configuration is a typical design. One polymer component serves as the fiber's core in this structure, and another polymer component serves as its sheath. Materials for the sheath and core may differ in terms of surface qualities, chemical resistance, or melting points.
Bicomponent fibers can be treated using methods like melt spinning or solution spinning when creating nonwoven fabrics. The sheath portion of bicomponent fibers can melt or dissolve when heated or exposed to solvents, enabling the fibers to join together and create a nonwoven fabric. The fabric's structural integrity is provided by the core component, which is unaltered.
Bicomponent nonwoven fibers have a number of benefits for making fabrics. They can give the final nonwoven fabric improved strength, toughness, and dimensional stability. The bicomponent fibers' combination of ingredients also enables the insertion of particular capabilities like moisture control, antibacterial qualities, or improved softness.
Numerous industries use these fibers, including the automotive, filtration, personal care, and geotextile sectors. They are utilized in a variety of goods, including disposable filters, wipes, surgical gowns, and diapers.
Bicomponent nonwoven fibers, which have a variety of uses in various industries, enhance the performance and adaptability of nonwoven fabrics overall.
The Global Bicomponent Nonwoven Fibers Market accounted for $XX Billion in 2022 and is anticipated to reach $XX Billion by 2030, registering a CAGR of XX% from 2024 to 2030.
Short-cut bicomponent fiber for air-laid processes is introduced by FIBERPARTNER. Airbonder, a newly developed line of bicomponent fibers for air-laid applications, was introduced today by FIBERPARTNER, a global provider of raw materials for the textile industry with headquarters in Denmark.
After several years of extensive testing and research, FIBERPARTNER, one of the top providers of staple fibers for nonwovens, has launched the commercialization of its new line of bicomponent fibers for air-laid. In order to create nonwovens, air-laid technology uses dry forming technology followed by a bonding procedure, such as thermal bonding.
The sheath material of the fiber melts after compaction and heat activation, allowing the bicomponent fibers to bind to the other fibers.