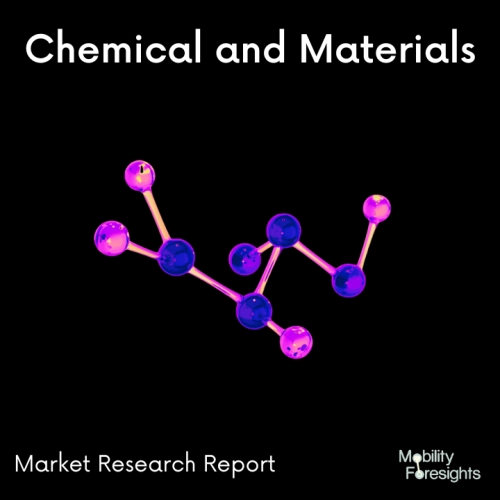
- Get in Touch with Us
Last Updated: Apr 25, 2025 | Study Period: 2024-2030
A group of additive manufacturing technologies is called binder jetting. A binder is selectively sprayed onto a powder bed during binder jetting, attaching these regions to one another to create a solid object one layer at a time. Metals, sand, and granular ceramics are the materials most frequently utilised in binder jetting.
In addition to producing full-colour prototypes (like figurines), massive sand casting cores and moulds, and inexpensive 3D printed metal parts, binder jetting is also utilised for other purposes.
In the additive manufacturing method known as "binder jetting," a liquid binding agent is selectively deposited by an industrial printer onto a thin layer of powder particles made of foundry sand, ceramics, metal, or composites in order to create high-end, one-of-a-kind parts and tools.
With such a wide range of uses, it is crucial for a designer to comprehend the fundamental physics of the procedure and how these relate to its main advantages and limitations if they wish to utilise Binder Jetting's capabilities to the maximum. The fact that bonding happens at normal temperature makes Binder Jetting superior to other 3D printing techniques.
This indicates that heat influences can cause dimensional distortions. The entire build volume can be used for binder jetting; the build platform is not required. Binder jetting is therefore appropriate for small- to medium-sized batch production. Binder Jetting's full potential requires careful consideration on how to fill the machine's whole build volume efficiently (bin packing).
The Global Binder jet additive manufacturing system market accountedfor $XX Billion in 2022 and is anticipated to reach $XX Billion by 2030, registering a CAGR of XX% from 2024to 2030.
The commercial introduction of its Series 3 binder jet platform has been announced by GE Additive, the commercial 3D printing arm of US energy giant GE.
Using the same technology as its alpha and beta predecessors, the Series 3 is able to quickly deposit a proprietary binder into components with wall thicknesses of less than 500 m and a maximum weight of 25 kg.
According to Josh Mook, an Innovation Leader at GE Additive, it is feasible to produce metal parts like castings on an industrial scale using the machines, which can be integrated into automated production lines.
There are many different 3D printing techniques available today, and the benefits and drawbacks of these options are frequently unclear. In the world of additive manufacturing, binder jetting is recognised for its high volumetric output.
It is also the additive manufacturing technology that most closely resembles conventional paper printing in terms of simplicity and speed. As it flows through the layers of powder, which are created like sheets of paper, the binder acts like ink.
In contrast, many other types of 3D printing construct components using a single point, frequently a laser or nozzle that melts, extrudes, or joins materials. Drawing out each part using a single point, layer by layer, calls for far more effort and material.
Foundries can avoid the lengthy lead times and expensive prices of conventional patterns and core boxes made from wood or metal by 3D printing directly from CAD files.
The design freedom of additive manufacturing also allows designers to reinvent the parts manufactured with the reliable casting method - creating complicated, condensed geometries that enable lightweighting and enhanced part performance not feasible with traditional processes.
Binder jetting stands out among 3D printing techniques because of its high speeds and material versatility as a technology that could revolutionise conventional large-volume manufacturing and make 3D printing's benefits in terms of design, affordability, and sustainability accessible to everyone.
Sl no | Topic |
1 | Market Segmentation |
2 | Scope of the report |
3 | Abbreviations |
4 | Research Methodology |
5 | Executive Summary |
6 | Introduction |
7 | Insights from Industry stakeholders |
8 | Cost breakdown of Product by sub-components and average profit margin |
9 | Disruptive innovation in the Industry |
10 | Technology trends in the Industry |
11 | Consumer trends in the industry |
12 | Recent Production Milestones |
13 | Component Manufacturing in US, EU and China |
14 | COVID-19 impact on overall market |
15 | COVID-19 impact on Production of components |
16 | COVID-19 impact on Point of sale |
17 | Market Segmentation, Dynamics and Forecast by Geography, 2024-2030 |
18 | Market Segmentation, Dynamics and Forecast by Product Type, 2024-2030 |
19 | Market Segmentation, Dynamics and Forecast by Application, 2024-2030 |
20 | Market Segmentation, Dynamics and Forecast by End use, 2024-2030 |
21 | Product installation rate by OEM, 2023 |
22 | Incline/Decline in Average B-2-B selling price in past 5 years |
23 | Competition from substitute products |
24 | Gross margin and average profitability of suppliers |
25 | New product development in past 12 months |
26 | M&A in past 12 months |
27 | Growth strategy of leading players |
28 | Market share of vendors, 2023 |
29 | Company Profiles |
30 | Unmet needs and opportunity for new suppliers |
31 | Conclusion |
32 | Appendix |