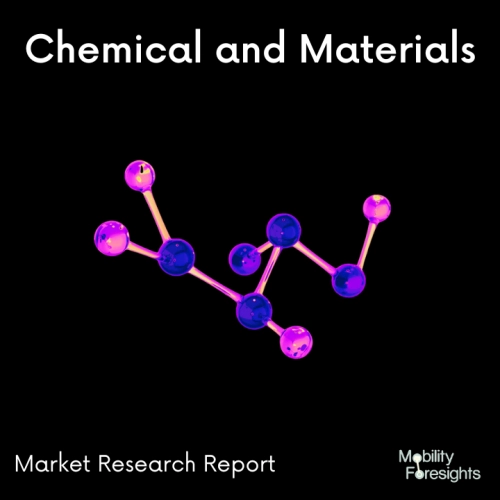
- Get in Touch with Us
Last Updated: Apr 25, 2025 | Study Period: 2024-2030
Genomatica designed microbes to ferment plant sugars to generate caprolactam, and consequently nylon, in a 100% renewable manner using a synthetic biology technique.
The newly created bio-based nylon from producer NILIT is strong yet sustainable, and it is intended to reduce dependence on non-renewable resources as well as greenhouse gas emissions.
Eco-friendly nylon Biodegradable nylon is another more environmentally friendly substitute for nylon. The fundamental advantage of biodegradable nylon is that it organically breaks down in particular environmental circumstances, unlike recovered nylon. Thus, it doesn't persist in nature for a long timeâperhaps hundreds of years.
Bio-based polymers are substances created using regenerative resources. There is a significant distinction between the two types of polymers, despite the fact that the terms "bio-based polymers" and "biodegradable polymers" are frequently used in the literature.
Bio-based raw materials come from living things including various kinds of plants, wood, and algae. The term "renewable" is used to describe both raw materials and energy. Renewable sources include the sun, wind, and water, but they can also include any bio-based raw resource.
To create entirely biobased nylons, monomer precursors (dicarboxylic acids and diamines) are created through fermentation, isolated, purified, and then polymerized.
Bionylons can biodegrade after being discarded. According to the creators, the material is created entirely from plant-based feedstocks like sugar cane and industrial corn, which Geno transforms into nylon-6 polymer. It shares the same chemical composition as its equivalent obtained from fossil fuels.
The Global Bio-based nylon market accounted for $XX Billion in 2022 and is anticipated to reach $XX Billion by 2030, registering a CAGR of XX% from 2024 to 2030.
A new, more environmentally friendly nylon has been created by Toray Industries, Inc., marking a significant advancement in the business's sustainability mission.
The company's integrated Eco dear brand for biomass-based polymer materials and goods now includes nylon as the newest product.
Sebacic acid generated from castor beans is the basis of Toray's new Eco dear nylon, which is 60% bio-based. The resulting fibred may be spun using the same method as traditional nylon, and it is first offered in forms with 10, 20, and 50 denier.
By extending its business of biomass-based polymer materials and goods under the ecodear brand in a variety of industries, including fibred, resin, and film, Toray aims to further its ambition to offer answers to environmental problems.
The creation of Eco dear nylon serves as evidence of the advantages of Toray's vertical integration structure. Toray is able to maintain quality control over its products from the development of polymers through the production of completed yarns because it is both a chemical factory and a textile business.
Dermizax and Entrant, two well-known Toray brand innovations, can be produced with ecodear nylon in bio-based variants.
Sl no | Topic |
1 | Market Segmentation |
2 | Scope of the report |
3 | Abbreviations |
4 | Research Methodology |
5 | Executive Summary |
6 | Introduction |
7 | Insights from Industry stakeholders |
8 | Cost breakdown of Product by sub-components and average profit margin |
9 | Disruptive innovation in the Industry |
10 | Technology trends in the Industry |
11 | Consumer trends in the industry |
12 | Recent Production Milestones |
13 | Component Manufacturing in US, EU and China |
14 | COVID-19 impact on overall market |
15 | COVID-19 impact on Production of components |
16 | COVID-19 impact on Point of sale |
17 | Market Segmentation, Dynamics and Forecast by Geography, 2024-2030 |
18 | Market Segmentation, Dynamics and Forecast by Product Type, 2024-2030 |
19 | Market Segmentation, Dynamics and Forecast by Application, 2024-2030 |
20 | Market Segmentation, Dynamics and Forecast by End use, 2024-2030 |
21 | Product installation rate by OEM, 2023 |
22 | Incline/Decline in Average B-2-B selling price in past 5 years |
23 | Competition from substitute products |
24 | Gross margin and average profitability of suppliers |
25 | New product development in past 12 months |
26 | M&A in past 12 months |
27 | Growth strategy of leading players |
28 | Market share of vendors, 2023 |
29 | Company Profiles |
30 | Unmet needs and opportunity for new suppliers |
31 | Conclusion |
32 | Appendix |