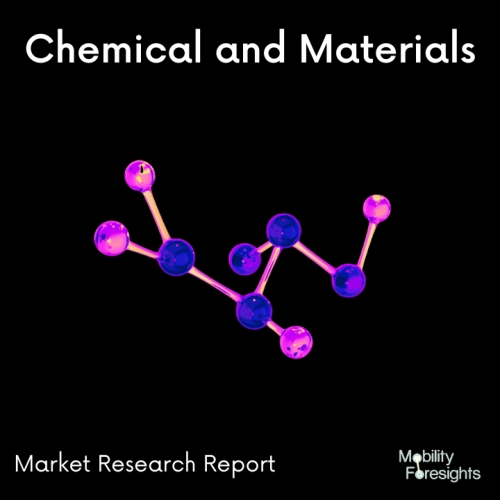
- Get in Touch with Us
Last Updated: Apr 25, 2025 | Study Period: 2024-2030
A resin that gets part or all of its constituent monomers from biological sources is referred to as a bio-resin. The sources of today are plant-based, mostly by-products of the refinement of bio-diesel fuel made from corn or soybeans.
Other contenders include potatoes, lignocellulose, whey, algae, sugar beets, cane sugar, and sugar beets. The main reason why maize and soybeans are desirable is their abundance.
Bio-resins are quite appealing. They lessen reliance on petrochemicals, and firms who utilize them can market greener products due to their price volatility.
They also have a better lifespan profile than materials made from petrochemicals. Until now, the challenge has been to efficiently transform corn and soybean products into the monomers needed to create a resin.
The Global bio-based resin market accounted for $XX Billion in 2023 and is anticipated to reach $XX Billion by 2030, registering a CAGR of XX% from 2024 to 2030.
Biters Ltd., a top producer of specialty chemicals and polymers in Europe, is launching a new line of bio-based thermosetting resins for the composites sector that are consistent with regulations.
The brand-new group of bio-based resins, which also includes PFA (Poly furfuryl Alcohol) and bio-Epoxy systems, is REACH (registration, assessment, authorization and restriction of chemicals) compliant and intended specifically for composite applications.
PFA is a thermosetting bio-resin made from biomass agricultural waste that shares many characteristics with phenolic resin but emits fewer volatile organic compounds.
PFA possesses fire retardant qualities comparable to Phenolic, great temperature and chemical resistance, and environmental credentials.
Bisphenol A and epichlorohydrin are needed for epoxy resins. Bitzer provides epoxy products based on renewable replacement feedstock through the use of innovative chemistry, which when combined with our eco-friendly epoxy curing agents results in formulated systems with a high bio-content.
Avent Corporation announced the introduction of an addition to its portfolio of Gravy-Tech Density Modified Formulations to provide more environmentally friendly grades made from recycled and bio-based resin and/or filler, without compromising performance.
First-generation Gravy-Tech Density Modified Formulations were created utilizing carefully chosen metallic fillers and thermoplastic resin to imitate the opulent weight, feel, and appearance of die-cast or machined metals.
These serve as an affordable substitute for metal in applications for luxury packaging and consumer goods, such as caps and closures for cosmetics, bottle caps and boxes for alcoholic beverages, and decorative knobs and grips for furniture, appliances, and automobiles.
Avent is expanding its Gravy-Tech Density Modified Formulations product line with two more eco-friendly options as OEMs and customers look for more environmentally friendly materials in the packaging sector.
The first, Gravy-Tech REC Recycled Formulations, is built on recycled resin and/or filler from sources that have been post-industrial recycled (PIR) and/or post-consumer recycled (PCR).
The second, Gravy-Tech BIO Bio-based Formulations, includes resin made from renewable plant sources.
Both are designed to provide performance that is equivalent to that of standard density-modified solutions while using less virgin thermoplastics, promoting the circular economy and lowering their carbon footprint in comparison to alternatives made from fossil feedstock resin.
In order to create a useful substitute for lead and other conventional metals, Gravy-Tech Density Modified Formulations were first created.
They have densities similar to traditional metals while offering flexibility in design and processing since they are made using designed thermoplastic resins and specific metallic fillers.
The new formulations made from recycled and bio-based materials provide the same performance advantages in response to market and consumer demand for more environmentally friendly products.
They also support the circular economy and aid customers in achieving their sustainability objectives.
These novel materials can be extruded, molded, calendared, or thermoformed into complicated shapes without costly tooling, just like prime density modified grades can.
Depending on the needs of the application, performance parameters can be altered, including density, corrosion and chemical resistance, and mechanical performance.
Current production of Gravy-Tech REC Recycled Formulations and Gravy-Tech BIO Bio-based Formulations is done in Europe, and both products are presently offered for sale on a global scale.
A major producer in bio-based chemicals, Groupe Berkey, recently launched a line of 100% bio-based alkyd resins for the construction paints market.
Plant extraction and formulation are Grouped Berker's two historical areas of specialization. These are where they use their industrial know-how and innovation.
Alkyd resins, also known as glycophytic resins, are produced and marketed by Lysol, a Groupe Berkey subsidiary since its acquisition, for the paints & coatings, wood preservation, and formed ink sectors.
With the goal of converting current products (bio-based oils, raw materials produced by organic chemistry, and petroleum solvents) into bio-based solutions, Groupe Berker has invested in the development of its portfolio.
A resin that can substitute raw materials with a petrochemical origin has been perfected by Luxel's Research & Development department from bio-based and renewable raw materials.
The use of a 100% bio-based solvent is one of the innovative and distinctive features of this resin. In light of this, the bio-based resin they created offers an immediate response to the demands of the construction industry, which has come under fire for its effects on the environment.
They are thrilled to be able to provide this market with a resin that has never been seen before yet possesses technical qualities that are exactly the same as those of conventional goods, promoting the responsible and sustainable evolution of this industry.
Sl no | Topic |
1 | Market Segmentation |
2 | Scope of the report |
3 | Abbreviations |
4 | Research Methodology |
5 | Executive Summary |
6 | Introduction |
7 | Insights from Industry stakeholders |
8 | Cost breakdown of Product by sub-components and average profit margin |
9 | Disruptive innovation in the Industry |
10 | Technology trends in the Industry |
11 | Consumer trends in the industry |
12 | Recent Production Milestones |
13 | Component Manufacturing in US, EU and China |
14 | COVID-19 impact on overall market |
15 | COVID-19 impact on Production of components |
16 | COVID-19 impact on Point of sale |
17 | Market Segmentation, Dynamics and Forecast by Geography, 2024-2030 |
18 | Market Segmentation, Dynamics and Forecast by Product Type, 2024-2030 |
19 | Market Segmentation, Dynamics and Forecast by Application, 2024-2030 |
20 | Market Segmentation, Dynamics and Forecast by End use, 2024-2030 |
21 | Product installation rate by OEM, 2023 |
22 | Incline/Decline in Average B-2-B selling price in past 5 years |
23 | Competition from substitute products |
24 | Gross margin and average profitability of suppliers |
25 | New product development in past 12 months |
26 | M&A in past 12 months |
27 | Growth strategy of leading players |
28 | Market share of vendors, 2023 |
29 | Company Profiles |
30 | Unmet needs and opportunity for new suppliers |
31 | Conclusion |
32 | Appendix |