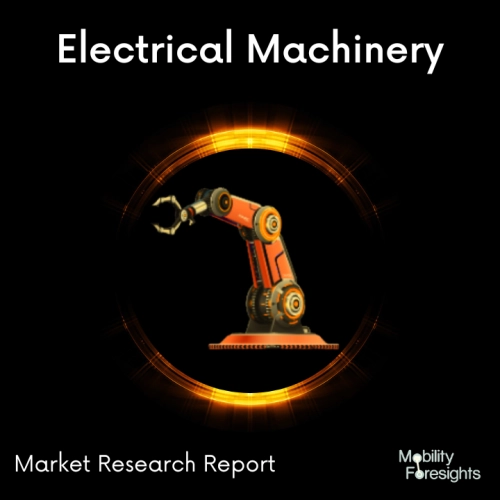
- Get in Touch with Us
Last Updated: Apr 25, 2025 | Study Period: 2024-2030
The Blister Inspection System is an automated machine that is used to detect defects in the packaging of pharmaceutical products.
The system is designed to inspect blister packaging for any defects, such as missing pills, wrong pills, or wrong dosing. It can also detect any cracks, tears, or other physical defects on the packaging.
The system utilizes advanced optical scanning technology to detect these defects with a high degree of accuracy. The system can also detect any foreign objects or contaminants in the packaging.
The Blister Inspection System is designed to be an efficient, cost-effective solution for quality assurance and safety in the pharmaceutical industry.
The system is easy to use and requires minimal maintenance. It can be integrated into existing production lines and can detect defects in a matter of seconds.
The system can also be customized to meet specific needs and requirements. The Blister Inspection System is an ideal solution for companies that need to ensure the quality and safety of their products. It is a reliable and cost-effective way to ensure that only the highest quality products are shipped to customers.
The Global Blister Inspection System market accounted for $XX Billion in 2023 and is anticipated to reach $XX Billion by 2030, registering a CAGR of XX% from 2024 to 2030.
BLISTER INSPECTION SYSTEM MARKETNEW PRODUCT LAUNCH
At the ProMach stand at Pack Expo Las Vegas, Pharmaworks and Serpa, two ProMach product brands, unveil the brand-new, completely integrated BTS blister transport system. The BTS effortlessly transfers blisters from a Pharmaworks blister machine and collates them to feed a Serpa carton.
It is ideal for pharmaceutical, biotech, nutraceutical, medical device, and other product applications. The fully servo-driven BTS handles various blister formats and collates up to ten blisters per bucket, achieving high speeds of up to hundreds of blisters while providing exceptional flexibility and quick, repeatable tool-less changeovers.
The transfer points are one of the most difficult parts of any packaging process. Product manufacturers and contract packers increasingly resort to one-stop equipment suppliers that can provide turnkey lines at lower rates and with shorter delivery times to avoid the time, money, and hassle spent buying different systems and integrating them in-house.
Although ProMach Pharma has long provided standalone blister transport systems, this is the only one that fully integrates the extensive knowledge of both the Pharmaworks and Serpa brands.
BLISTER INSPECTION SYSTEM MARKETRECENT DEVELOPMENT
PTI Inspection Systems unveils a brand-new, cutting-edge technology platform for testing blister packaging for leaks. A deterministic non-destructive method called OptiPac uses volumetric imaging in a vacuum to find leaks.
The OptiPac was developed and manufactured using One-Touch Technology to create a quick test cycle that requires no sample preparation or changeover and detects flaws as small as 5 microns. Operators will receive a volumetric measurement reading and a clear pass/fail outcome.
The innovative technology behind OptiPac provides several sophisticated features that make this system a very user-friendly and intuitive way to test blister packets. Additionally, the position of the damaged cavity is determined. With our PTI ETHOS 21 CFR Part 11 software integrated into the system, OptiPac also provides total data integrity compliance.
BLISTER INSPECTION SYSTEM MARKETRECENT PARTNERSHIP
A brand-new solution for primary pack serialization and aggregation is being introduced to the market by SEA Vision and Marchesini Group. It consists of a whole spectrum of technologies to print, examine, and pack serialized blisters as well as perform aggregation with cartons, all of which are integrated into a 4.0 environment. The two businesses decided to invest in this difficult initiative to improve product identification, which is essential in the healthcare sector.
In the case of cartons and pallets, this need is now upheld, however, it does not apply to main packaging, such as blisters. This means that despite all the investments made by pharmaceutical corporations to ensure that secondary packaging is traceable, there is still a concealed gap that could cause catastrophic harm. It also indicates that there is still a risk of counterfeiting when it comes to the primary packaging for pharmaceuticals.
Sl no | Topic |
1 | Market Segmentation |
2 | Scope of the report |
3 | Abbreviations |
4 | Research Methodology |
5 | Executive Summary |
6 | Introduction |
7 | Insights from Industry stakeholders |
8 | Cost breakdown of Product by sub-components and average profit margin |
9 | Disruptive innovation in the Industry |
10 | Technology trends in the Industry |
11 | Consumer trends in the industry |
12 | Recent Production Milestones |
13 | Component Manufacturing in US, EU and China |
14 | COVID-19 impact on overall market |
15 | COVID-19 impact on Production of components |
16 | COVID-19 impact on Point of sale |
17 | Market Segmentation, Dynamics and Forecast by Geography, 2024-2030 |
18 | Market Segmentation, Dynamics and Forecast by Product Type, 2024-2030 |
19 | Market Segmentation, Dynamics and Forecast by Application, 2023-2030 |
20 | Market Segmentation, Dynamics and Forecast by End use, 2024-2030 |
21 | Product installation rate by OEM, 2024 |
22 | Incline/Decline in Average B-2-B selling price in past 5 years |
23 | Competition from substitute products |
24 | Gross margin and average profitability of suppliers |
25 | New product development in past 12 months |
26 | M&A in past 12 months |
27 | Growth strategy of leading players |
28 | Market share of vendors, 2024 |
29 | Company Profiles |
30 | Unmet needs and opportunity for new suppliers |
31 | Conclusion |
32 | Appendix |