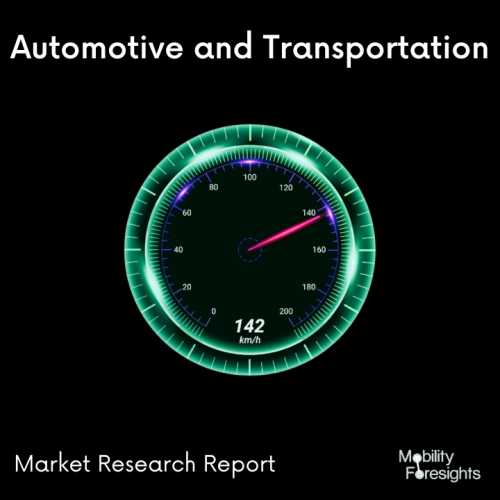
- Get in Touch with Us
Last Updated: Apr 25, 2025 | Study Period: 2023-2030
When all of a car body's sections have been welded together, with the exception of moving parts trims or chassis subassemblies, the body's sheet is referred to as being "body-in-white" (BiW).
Typically, a car's BiW makes up roughly of its curb weight and continues to be the dominant factor in how the car will behave. BiW can be constructed into two different types of structures:
the more popular monocoque structure, in which the chassis is built into the BiW and is merged with the body members, and the body-on-frame structure, in which the frame serves as the primary load-bearing part. BiW is anticipated to have a number of important characteristics. In addition to having high bending, torsional, static, and dynamic stiffness, it must also have strong tensile strength.
Additionally, it must meet the Federal Motor Vehicle Safety Standard and offer high-quality protection against all types of crashes, including rollovers, for both the car's body and its occupants.
By absorbing or lowering these circumstances, it should also be able to shield occupants from noise, vibration, and/or harshness (NVH). It should also be simple to form, easy to weld, highly paintable, and simple to design.
It should offer an excellent, smooth surface finish and should be corrosion resistant. Since BiW makes up a sizable portion of the weight of an automobile, improving fuel economy also involves using lightweight materials; in addition, given contemporary environmental concerns, it is also required to be recyclable.
A significant change has taken place in the shape of the complete body-in-white (BiW) of BMW's i3 model, a fully electric automobile, which is composed entirely of carbon-fibre-reinforced plastics (CFRPs), amid the heated dispute over whether aluminium is suitable as a substitute for steel in BiW.
BMW made the decision to construct a car with a main body entirely built of CFRP, resulting in the manufacture of the BMW i3 at approximately one-third of the market cost, in order to explore the viability of CFRP as a material in producing various car parts as well as its potential in lightweighting cars. Compared to steel and aluminium, CFRP has a lower density and greater specific strength, making it the material of choice.
The Global Body In White structural adhesives market accountedfor $XX Billion in 2021 and is anticipated to reach $XX Billion by 2030, registering a CAGR of XX% from 2022 to 2030.
Expandable, highly toughened structural adhesives offer strength and rigidity to body-in-white structures, chassis, and closures while securely joining gaps. In comparison to other options, these hybrid epoxy adhesives improve the structural performance of the vehicle when employed in the building of the vehicle body between sheet metal cavities.
With better adhesion in locations where it is challenging to connect with their non-expanding counterparts, these materials help deliver excellent joint quality. Body shops have successfully used the technology to strengthen body, panoramic, and roof structures to increase crashworthiness.
Before painting or adding the motor, chassis sub-assemblies, or trim (glass, door locks/handles, seats, upholstery, electronics, etc.), a car body's frame is linked together during the body in white (BIW) stage of the production process. A variety of methods are used during assembly, including laser brazing, riveting, clinching, bonding, spot welding (MIG/MAG), and riveting.
The phrase is a throwback to earlier production processes before steel unibody monocoques, when car bodywork were built by independent companies on a separate chassis with an attached engine, suspension, and bumpers. To attach onto the frame, the makers created or bought hardwood bodies with thin, non-structural metal sheets on the outside. Before the final hue, the bodies were painted with a white coat.
Sl no | Topic |
1 | Market Segmentation |
2 | Scope of the report |
3 | Abbreviations |
4 | Research Methodology |
5 | Executive Summary |
6 | Introduction |
7 | Insights from Industry stakeholders |
8 | Cost breakdown of Product by sub-components and average profit margin |
9 | Disruptive innovation in the Industry |
10 | Technology trends in the Industry |
11 | Consumer trends in the industry |
12 | Recent Production Milestones |
13 | Component Manufacturing in US, EU and China |
14 | COVID-19 impact on overall market |
15 | COVID-19 impact on Production of components |
16 | COVID-19 impact on Point of sale |
17 | Market Segmentation, Dynamics and Forecast by Geography, 2023-2030 |
18 | Market Segmentation, Dynamics and Forecast by Product Type, 2023-2030 |
19 | Market Segmentation, Dynamics and Forecast by Application, 2023-2030 |
20 | Market Segmentation, Dynamics and Forecast by End use, 2023-2030 |
21 | Product installation rate by OEM, 2023 |
22 | Incline/Decline in Average B-2-B selling price in past 5 years |
23 | Competition from substitute products |
24 | Gross margin and average profitability of suppliers |
25 | New product development in past 12 months |
26 | M&A in past 12 months |
27 | Growth strategy of leading players |
28 | Market share of vendors, 2023 |
29 | Company Profiles |
30 | Unmet needs and opportunity for new suppliers |
31 | Conclusion |
32 | Appendix |