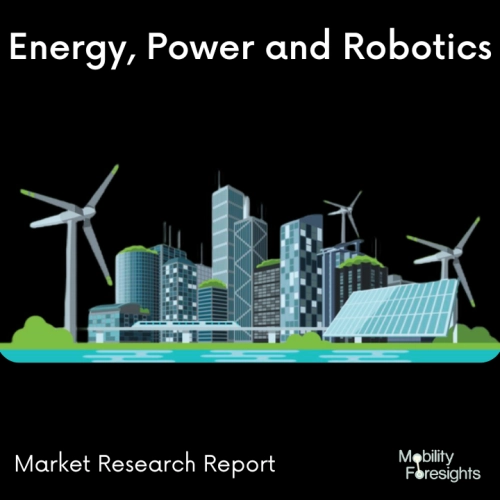
- Get in Touch with Us
Last Updated: Apr 25, 2025 | Study Period: 2023-2030
INTRODUCTION
UGVs used for bomb disposal are often controlled remotely, either wirelessly or over a cable. They might feature caterpillar tracks, and some might have unique wheel arrangements that let them move up and down stairs. For indoor tasks, some robots are portable and light enough to be carried by a single operator and thrown over a wall or through a window.
Bomb-disposal robots often include a manipulator arm that is equipped with wirecutters and/or a grabber as well as other tools to help them move around obstructions.
A camera and a unique waterjet tool that can quickly cut the power wires to an explosive device may also be attached on the arm.
A wheeled platform containing a winder mechanism is part of an explosives disposal robot that is specially designed for usage in hazardous settings.
This mechanism makes sure that the remote control cable won't become tangled up with the robot or its attachments. A turret mechanism that can rotate indefinitely and that is coaxial with the winder mechanism carries a manipulator arm section on it.
This section includes a first arm that can pivot through about 110° and a second arm that can pivot through about 120°. It also carries a bulkhead to which any of a number of end effectors can be connected using a quick connect and disconnect mechanism.
GLOBAL BOMB-DISPOSAL ROBOT MARKET SIZE AND FORECAST
The Global Bomb-Disposal Robot market accountedfor $XX Billion in 2022 and is anticipated to reach $XX Billion by 2030, registering a CAGR of XX% from 2023 to 2030.
Diverse professionals from around the world have worked together to create a robot that can dispose of bombs in order to create a cost-effective, secure tool for emergency rescue assistance.
For the benefit of bomb disposal teams, a 6 DOF articulated robotic arm installed on a mobile platform has been designed. The robot's whole operation can be handled remotely from a computer.
The actuator for the arm is a DC servo motor, and the servo is managed by a PWM signal produced by the microcontroller. The mathematical modelling of a 6 DOF robotic arm and the development process for the full prototype are the subjects of this study.
Sl no | Topic |
1 | Market Segmentation |
2 | Scope of the report |
3 | Abbreviations |
4 | Research Methodology |
5 | Executive Summary |
6 | Introduction |
7 | Insights from Industry stakeholders |
8 | Cost breakdown of Product by sub-components and average profit margin |
9 | Disruptive innovation in the Industry |
10 | Technology trends in the Industry |
11 | Consumer trends in the industry |
12 | Recent Production Milestones |
13 | Component Manufacturing in US, EU and China |
14 | COVID-19 impact on overall market |
15 | COVID-19 impact on Production of components |
16 | COVID-19 impact on Point of sale |
17 | Market Segmentation, Dynamics and Forecast by Geography, 2023-2030 |
18 | Market Segmentation, Dynamics and Forecast by Product Type, 2023-2030 |
19 | Market Segmentation, Dynamics and Forecast by Application, 2023-2030 |
20 | Market Segmentation, Dynamics and Forecast by End use, 2023-2030 |
21 | Product installation rate by OEM, 2023 |
22 | Incline/Decline in Average B-2-B selling price in past 5 years |
23 | Competition from substitute products |
24 | Gross margin and average profitability of suppliers |
25 | New product development in past 12 months |
26 | M&A in past 12 months |
27 | Growth strategy of leading players |
28 | Market share of vendors, 2023 |
29 | Company Profiles |
30 | Unmet needs and opportunity for new suppliers |
31 | Conclusion |
32 | Appendix |