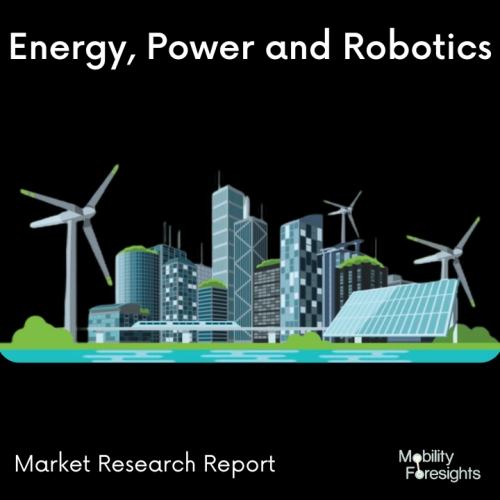
- Get in Touch with Us
Last Updated: Apr 25, 2025 | Study Period: 2024-2030
Aluminum is a relatively expensive material, and there are a number of alternative materials available for heat exchangers, such as copper and stainless steel. These alternative materials may be more cost-effective or offer better performance for certain applications.
Brazed Aluminum Heat Exchangers are an efficient solution for transferring heat between two fluids. The high thermal conductivity of aluminum combined with a brazed joint make these heat exchangers an ideal choice for applications that require a high performance, lightweight, and cost-effective solution.
Brazed Aluminum Heat Exchangers are constructed by joining metal plates together using a brazing process. This process involves melting a filler metal, typically silver or copper, between the two plates to form a strong joint. The metal plates are typically made of aluminum, but can also be made from other materials such as stainless steel or titanium.
The filler metal is chosen based on its corrosion resistance and temperature resistance characteristics. As a result, Brazed Aluminum Heat Exchangers are often used in applications where corrosive fluids are present or temperatures exceed capabilities of traditional materials.
Brazed Aluminum Heat Exchangers are more efficient, lighter, and less expensive than traditional heat exchangers, making them an ideal choice for many applications. The brazed joints are also highly reliable and have a low risk of leakage. In addition, the aluminum material is highly resistant to corrosion and is easy to fabricate.
Overall, Brazed Aluminum Heat Exchangers provide an efficient, cost-effective solution for many applications. The lightweight material, strong joints, and corrosion resistance make them an ideal choice for transferring heat between two fluids.
The Global Brazed Aluminum Heat Exchanger Market accounted for $XX Billion in 2023 and is anticipated to reach $XX Billion by 2030, registering a CAGR of XX% from 2024 to 2030.
Manufacturers are developing microchannel BAHXs with improved heat transfer efficiency and compact designs. This technology holds potential for various applications, including electronics cooling and aerospace.
Research is applying nanocoatings to BAHXs to enhance their performance and durability. This can lead to improved corrosion resistance and extended lifespan for BAHXs.
Manufacturers are increasingly using recycled aluminum and other sustainable materials in BAHX production to reduce environmental impact. BAHXs are being used to recover waste heat from industrial processes, contributing to overall energy efficiency and reducing greenhouse gas emissions.
BAHXs offer superior heat transfer efficiency compared to other types of heat exchangers, making them a key component in various energy-efficient technologies. This is driving significant market growth.
BAHXs are finding applications in diverse industries like HVAC, automotive, aerospace, refrigeration, and petrochemical. This widespread adoption is fueling the market growth.
Continuous advancements in BAHX design and materials are leading to improved performance, reliability, and cost-effectiveness. This is making them a more attractive option for various applications.
BAHXs are becoming increasingly used to recover waste heat from industrial processes, contributing to energy efficiency and reducing greenhouse gas emissions. This trend is gaining traction due to its economic and environmental benefits.
BAHXs are being integrated with renewable energy sources like solar and wind power to create more sustainable and efficient energy systems. This trend is expected to accelerate as the world transitions towards renewable energy sources.
Alfa Laval specifically targets the rapidly growing fuel cell industry. The compact design allows for easy integration into fuel cell systems, while the high efficiency and low pressure drop contribute to improved overall system performance. Additionally, the robust construction ensures long-term reliability and durability in demanding operating conditions.
Linde Engineering's new product line offers advancements in heat transfer efficiency, particularly beneficial for industrial gas production, petrochemical processing, and natural gas processing. This increased efficiency translates to improved production yields and reduced energy consumption.
Designed for cryogenic applications like air separation and LNG production, this series from Five Cryo emphasizes increased efficiency and reduced weight. The improved efficiency leads to lower energy consumption and operational costs, while the reduced weight makes the heat exchangers easier to handle and install.
Catering to a diverse range of applications, including automotive, HVAC, and industrial sectors, the SPP-X series focuses on lightweight design, high thermal conductivity, and excellent corrosion resistance. The lightweight design improves fuel efficiency in vehicles and reduces energy consumption in industrial applications. The high thermal conductivity ensures rapid heat transfer, contributing to improved system performance.
Sl no | Topic |
1 | Market Segmentation |
2 | Scope of the report |
3 | Research Methodology |
4 | Executive Summary |
5 | Average B2b Price, By Region |
6 | Potential Opportunities For Client |
7 | Introduction |
8 | Latest & Upcoming Brazed Aluminum Heat Exchanger to the Market |
9 | Technology trends in the Industry |
10 | Aluminum and aluminum alloys are the primary materials for BAHX |
11 | Brazed aluminum heat exchangers find applications across diverse industries |
12 | BAHX operates on the principle of transferring heat between two fluids, typically a hot fluid and a cooler fluid. |
13 | New product development in past 12 months |
14 | Market Size, Dynamics and Forecast by Type, 2024-2030 |
15 | Market Size, Dynamics and Forecast by ApplicationType, 2024-2030 |
16 | Market Size, Dynamics and Forecast by Material Type, 2024-2030 |
17 | Market Size, Dynamics and Forecast by Geography Type, 2024-2030 |
18 | Competitive Landscape |
19 | Gross margin and average profitability of suppliers |
20 | M&A in past 12 months |
21 | Growth strategy of leading players |
22 | Market share of vendors, 2023 |
23 | Company Profiles |
24 | Unmet needs and opportunity for new suppliers |
25 | Conclusion |