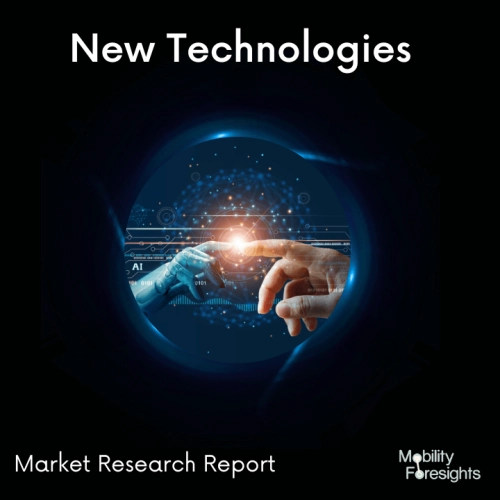
- Get in Touch with Us
Last Updated: Apr 25, 2025 | Study Period: 2024-2030
Poly(vinyl chloride), polyethylene, chlorinated polyethylene, and chlorosulfonated polyethylene/neoprene are the materials most typically used to make cable jackets. For analogue or digital transmission requiring a large bandwidth, coaxial and twinaxial (two coaxial cables in a single jacket) cables are employed.
A coaxial cable has superior insulation in between an outer conductor and an inner conductor that are entirely encircled by one another. A safeguarding sheath surrounds the outside conductor. Coaxial cables and twisted pairs can be combined to create a larger cable with a very high overall bandwidth, much like with twisted pairs.
Today's market offers a wide variety of cables with various jacket options and other unique features. It should come as no surprise that selecting the ideal cable jacket while balancing cost and lead times can be challenging and occasionally perplexing. PVC (polyvinyl chloride), PUR (polyurethane), PE (polyethylene), and TPE are the four major types of sensor cable jackets (thermoplastic elastomer).
Every style of jacket offers a different set of advantages, such as washdown, abrasion resistance, or high flexing uses. Choosing the right jacket type for application can increase the cable's lifespan and reduce machine downtime.
The Global cable jacket material market accounted for $XX Billion in 2023 and is anticipated to reach $XX Billion by 2030, registering a CAGR of XX% from 2024 to 2030.
High-Density Polyethylene (HDPE) cable jackets are a product offered by Hydro Group for uses needing high levels of abrasion resistance. In addition, both the inner and outer sheaths of armoured cables are frequently made from this sort of jacket. Hydro Group has also developed a custom PE moulding technology to enable connection termination for PE jacketed cables.
Hydro Group can now provide customers with a full cable solution that transitions from subsea to the topside thanks to the addition of new materials, one of which is a low-smoke, zero-halogen, flame retardant SHF material to IEC60092 suited for use in shipboard & topside applications.
Sl no | Topic |
1 | Market Segmentation |
2 | Scope of the report |
3 | Abbreviations |
4 | Research Methodology |
5 | Executive Summary |
6 | Introduction |
7 | Insights from Industry stakeholders |
8 | Cost breakdown of Product by sub-components and average profit margin |
9 | Disruptive innovation in the Industry |
10 | Technology trends in the Industry |
11 | Consumer trends in the industry |
12 | Recent Production Milestones |
13 | Component Manufacturing in US, EU and China |
14 | COVID-19 impact on overall market |
15 | COVID-19 impact on Production of components |
16 | COVID-19 impact on Point of sale |
17 | Market Segmentation, Dynamics and Forecast by Geography, 2024-2030 |
18 | Market Segmentation, Dynamics and Forecast by Product Type, 2024-2030 |
19 | Market Segmentation, Dynamics and Forecast by Application, 2024-2030 |
20 | Market Segmentation, Dynamics and Forecast by End use, 2024-2030 |
21 | Product installation rate by OEM, 2023 |
22 | Incline/Decline in Average B-2-B selling price in past 5 years |
23 | Competition from substitute products |
24 | Gross margin and average profitability of suppliers |
25 | New product development in past 12 months |
26 | M&A in past 12 months |
27 | Growth strategy of leading players |
28 | Market share of vendors, 2023 |
29 | Company Profiles |
30 | Unmet needs and opportunity for new suppliers |
31 | Conclusion |
32 | Appendix |