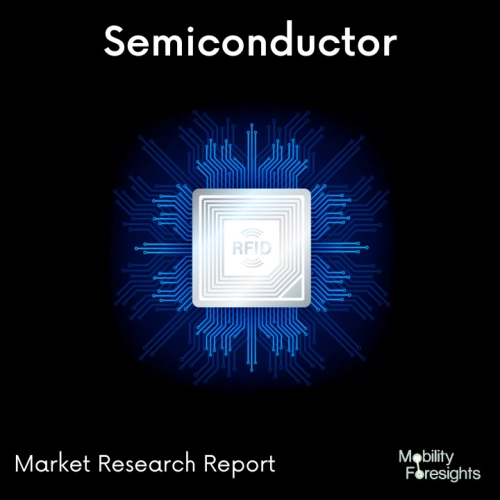
- Get in Touch with Us
Last Updated: Apr 25, 2025 | Study Period: 2023-2030
INTRODUCTION
The inner or outside dimensions of an object are often measured using caliper sensors, which are tools for measuring the distance between two points. It consists of two adjustable jaws or arms that can be used to measure an object. A calibrated scale or digital readout that shows the separation between the jaws is attached to them.
Vernier calipers, dial calipers, and digital calipers are a few examples of the several types of calipers sensors. Vernier calipers measure the space between the jaws using a sliding scale, whereas dial calipers display the measurement on a dial.
Digital calipers are often more accurate and simpler to read than other types of calipers since they show the measurement on an electronic display.
Caliper sensors are used in a variety of industries, such as engineering, manufacturing, and machining, to precisely measure the dimensions of parts and components.
The diameter of rotors and drums as well as the thickness of brake pads are measured using them in the automotive sector. Caliper sensors are used in the medical industry to gauge body fat levels by measuring the thickness of skin folds.
Stainless steel, aluminum, and plastic are just a few of the materials that can be used to make caliper sensors, depending on the intended function and amount of precision needed.
They are made to be strong and resilient, and some models have water and dust resistance for usage in challenging locations. Caliper sensors are normally operated by hand and require just sporadic cleaning and calibration in terms of maintenance.
GLOBAL CALIPER SENSOR MARKET SIZE AND FORECAST
The Global Caliper Sensor Market accounted for $XX Billion in 2022 and is anticipated to reach $XX Billion by 2030, registering a CAGR of XX% from 2023 to 2030.
NEW PRODUCT LAUNCH
In order to optimize the production of lithium-ion batteries (LIBs), Honeywell introduced an optical caliper measurement sensor in HOUSTON.
The novel sensor offers a practical means of determining the actual electrode material thickness both during coating and at the pressing station during LIB production. An important need for optimum battery performance is accurate thickness measuring.
The coating and pressing processes on the battery production line have stringent criteria for LIB producers. It is crucial to create electrode sheets that have a consistent covering on both the top and bottom of the material.
In order to regulate the coating in the cross direction (CD), machine direction (MD), and later the calendaring process, an exact thickness measurement of the coating can be used.
COMPANY PROFILE
THIS REPORT WILL ANSWER THE FOLLOWING QUESTIONS
Sl no | Topic |
1 | Market Segmentation |
2 | Scope of the report |
3 | Abbreviations |
4 | Research Methodology |
5 | Executive Summary |
6 | Introduction |
7 | Insights from Industry stakeholders |
8 | Cost breakdown of Product by sub-components and average profit margin |
9 | Disruptive innovation in the Industry |
10 | Technology trends in the Industry |
11 | Consumer trends in the industry |
12 | Recent Production Milestones |
13 | Component Manufacturing in US, EU and China |
14 | COVID-19 impact on overall market |
15 | COVID-19 impact on Production of components |
16 | COVID-19 impact on Point of sale |
17 | Market Segmentation, Dynamics and Forecast by Geography, 2023-2030 |
18 | Market Segmentation, Dynamics and Forecast by Product Type, 2023-2030 |
19 | Market Segmentation, Dynamics and Forecast by Application, 2023-2030 |
20 | Market Segmentation, Dynamics and Forecast by End use, 2023-2030 |
21 | Product installation rate by OEM, 2023 |
22 | Incline/Decline in Average B-2-B selling price in past 5 years |
23 | Competition from substitute products |
24 | Gross margin and average profitability of suppliers |
25 | New product development in past 12 months |
26 | M&A in past 12 months |
27 | Growth strategy of leading players |
28 | Market share of vendors, 2023 |
29 | Company Profiles |
30 | Unmet needs and opportunity for new suppliers |
31 | Conclusion |
32 | Appendix |