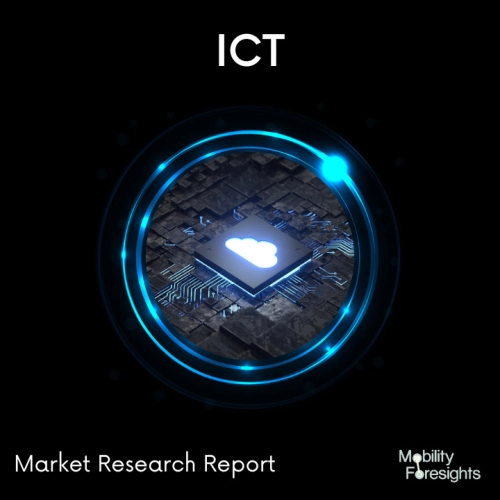
- Get in Touch with Us
Last Updated: Apr 25, 2025 | Study Period: 2024-2030
A live television broadcast chain typically includes the camera control unit (CCU). It can be used to remotely control various camera parameters and is in charge of powering the professional video camera as well as handling signals sent to and from the camera over the camera cable.
For the purposes of the controls outlined in this recommendation, the term "control camera" refers to either a conventional video camera or a stereoscopic camera.
In order to produce a picture that could be used, broadcast cameras used to require extensive racks of control units before they became self-contained units.
These racks were operated by a small group of skilled engineers and occupied an entire section of the OB truck during outside broadcast production. There were two roles for these vision engineers. First, they ensured that the produced image was broadcast-quality by setting up the CCUs at the beginning of a production.
The vision engineer and the camera operator would collaborate during this lengthy alignment process to simultaneously adjust the settings on both the actual camera and the CCU. The vision engineers were in charge of controlling the exposure and color balance as well as operating the CCUs during production.
This position required a dedicated vision engineer for each CCU due to its high skill level and labor-intensive nature. For industrial security and monitoring, camera controllers are used to remotely control vision systems and cameras.
Since camera controllers can handle multiple video or camera sites, a single receptacle source can capture and display data for real-time tracking.
TheGlobal Camera Control Unit marketaccounted for $XX Billion in 2023 and is anticipated to reach $XX Billion by 2030, registering a CAGR of XX% from 2024 to 2030.
Over the course of the past few years, Shotoku cameras have consistently decreased in size and weight, leading one to believe that the requirement for a sturdy, potent pan and tilt head has decreased in line with this trend. But it's not always that easy.
This is especially true when they are used with box cameras, which don't have much counterbalance of their own. Therefore, a studio PT head made for these smaller cameras still requires a significant amount of the strength and power of a head that is typically larger.
Shotoku has long been regarded as a pioneer in the design and production of robotic camera systems that are both efficient and dependable. The TG-47, the most recent member of the PT head family, continues this tradition. It is available fully encoded for AR/VR studio support, like all of our P&T heads.
The first important application is smaller national or regional studios where the production demands the quality and performance of broadcast cameras and lenses. In these studios, a typical 15 to 17-inch teleprompter is required, but no manual pan-bar control or large camera configurations with viewfinders, hand controls, and talent monitors are required.
The head can be used in conjunction with Shotoku's TI-11 elevator to create a powerful and extremely cost-effective PTZF&H package for this application.
It can also be mounted on a manual pedestal or tripod. The second application, which is just as important, is for studios that use Shotoku's Smart Rail ceiling track system.
This system supports a teleprompter of a useful size for the presenter while also supporting ceiling-mounted cameras with track-dolly movement and a long robotic descender column.
Sl no | Topic |
1 | Market Segmentation |
2 | Scope of the report |
3 | Abbreviations |
4 | Research Methodology |
5 | Executive Summary |
6 | Introduction |
7 | Insights from Industry stakeholders |
8 | Cost breakdown of Product by sub-components and average profit margin |
9 | Disruptive innovation in the Industry |
10 | Technology trends in the Industry |
11 | Consumer trends in the industry |
12 | Recent Production Milestones |
13 | Component Manufacturing in US, EU and China |
14 | COVID-19 impact on overall market |
15 | COVID-19 impact on Production of components |
16 | COVID-19 impact on Point of sale |
17 | Market Segmentation, Dynamics and Forecast by Geography, 2024-2030 |
18 | Market Segmentation, Dynamics and Forecast by Product Type, 2024-2030 |
19 | Market Segmentation, Dynamics and Forecast by Application, 2024-2030 |
20 | Market Segmentation, Dynamics and Forecast by End use, 2024-2030 |
21 | Product installation rate by OEM, 2023 |
22 | Incline/Decline in Average B-2-B selling price in past 5 years |
23 | Competition from substitute products |
24 | Gross margin and average profitability of suppliers |
25 | New product development in past 12 months |
26 | M&A in past 12 months |
27 | Growth strategy of leading players |
28 | Market share of vendors, 2023 |
29 | Company Profiles |
30 | Unmet needs and opportunity for new suppliers |
31 | Conclusion |
32 | Appendix |