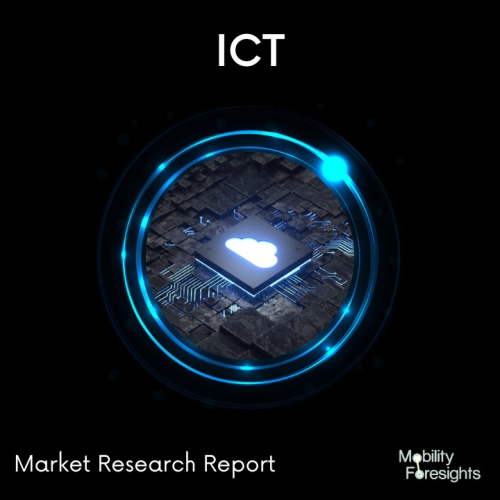
- Get in Touch with Us
Last Updated: Apr 25, 2025 | Study Period:
Ever-smaller camera module components can be precisely assembled and solidly bonded using special adhesives. The adhesives used are appropriate for manufacturing camera modules on a large scale and cure quickly at low temperatures.
Adhesives are used to attach the lenses and tiny modules of smartphone cameras. A product called the camera module is used to take pictures and films with mobile devices like smartphones, cars, and smart home appliances.
High technology is required in all fields, requiring high resolution, miniaturization, slimming, low-power, and high stiffness. Electronics like mobile phones and tablet computers frequently use compact camera modules. The optical design will often include numerous highly aspheric surfaces to decrease both the size and number of elements needed.
Adhesives are utilised a lot in the electronics industry, especially for camera modules for cell phones and smartphones.
Assembling camera modules into the device housing, fixing the camera chip to the circuit board (die attach), using the adhesive as chip underfill, adhering low-pass filters, and bonding individual parts such as the lens into the lens mount or the lens mount onto the camera sensor are all examples of this.
The global Camera Module Assembly adhesive market accounted for $XX Billion in 2022 and is anticipated to reach $XX Billion by 2030, registering a CAGR of XX% from 2023 to 2030.
Manufacturers are constantly developing new and innovative camera module assembly adhesives that are more efficient, durable, and cost-effective.
For example, manufacturers are developing adhesives that can be cured at lower temperatures, which can reduce energy costs and improve the production process. Manufacturers are also developing adhesives that are more resistant to environmental factors, such as moisture and temperature changes.
Camera modules are becoming increasingly miniaturized to fit into smaller and sleeker electronic devices. This is driving the demand for camera module assembly adhesives that are strong, durable, and have a low profile.
AR and VR applications are becoming increasingly popular, and this is driving the demand for camera module assembly adhesives that can withstand the harsh environments in which these devices are used.
DIC Corporation, a Japanese chemicals company, has developed a new adhesive for flexible camera modules. The new adhesive, called DICORAX ES-9300, is a UV-curable adhesive that is designed to bond flexible materials, such as polyimide (PI) and polyethylene terephthalate (PET), to camera modules.
3M, a leading global manufacturer of adhesives, sealants, and tapes, has launched a new adhesive for automotive camera modules. The new adhesive, called 3M Scotch-Weld Structural Adhesive Film AF 800, is a UV-curable adhesive that is designed to meet the demanding requirements of automotive camera modules, such as high strength, durability, and resistance to environmental factors.
The development of camera technologies to take advantage of the expansion of this market has put a lot of attention on the camera module business as camera functionalities are increasingly being added to mobile devices and, more recently, automotive products.
A different technique known as âActive Alignmentâ is used as camera modules get more sophisticated, especially as the number of pixels and lenses increases. This technique requires dual-cure adhesives with UV and thermal cure capabilities to connect the lens holder to the substrate.
Henkel offers extensive knowledge and a wide range of products available to meet the needs of both present and future camera module demands. Henkel is the global leader in semiconductor packaging and materials for electronics assembly. Furthermore, Henkel is unrivalled in terms of camera module success thanks to its unrivalled worldwide production footprint and local assistance.
Sl no | Topic |
1 | Market Segmentation |
2 | Scope of the report |
3 | Research Methodology |
4 | Executive Summary |
5 | Average B2B Price, By Region |
6 | Potential Opportunities |
7 | Introduction |
8 | Insights from Industry stakeholders |
9 | Cost breakdown of Product by sub-components and average profit margin |
10 | Disruptive innovation in the Industry |
11 | Technology trends in the Industry |
12 | Consumer trends in the industry |
13 | Recent Production Milestones |
14 | Component Manufacturing in US, EU and China |
15 | Key Drivers of Global Camera Module Assembly Adhesive Market |
16 | New product development in past 12 months |
17 | Market Segmentation, Dynamics and Forecast by Geography, 2023-2030 |
18 | Market Segmentation, Dynamics and Forecast by Type, 2023-2030 |
19 | Market Segmentation, Dynamics and Forecast by Application, 2023-2030 |
20 | Market Segmentation, Dynamics and Forecast by End use, 2023-2030 |
21 | Competitive Landscape |
22 | M&A in past 12 months |
23 | Growth strategy of leading players |
24 | Market share of vendors, 2023 |
25 | Company Profiles |
26 | Unmet needs and opportunity for new suppliers |
27 | Conclusion |