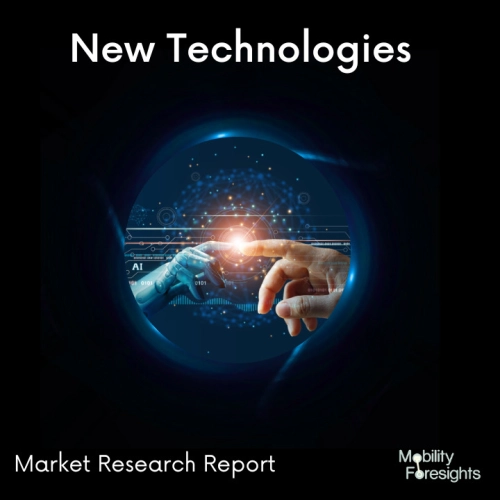
- Get in Touch with Us
Last Updated: Apr 25, 2025 | Study Period: 2023-2030
Flexible tubing specifically created and authorized for use in the food and beverage sector is referred to as "food and beverage flexible tubing." It is utilized in food processing, packaging, and dispensing systems to move liquids, gases, and other ingredients.
To guarantee the integrity and safety of the items being handled, flexible tubing used in the food and beverage industry must adhere to particular standards.
Food and beverage flexible tubing has a number of important features and considerations, includingFood-Grade Substance: Typically, food-grade materials that adhere to rules and standards established by agencies like the Food and Drug Administration (FDA) in the United States or equivalent regulatory bodies in other nations are used to make the tubing.
Plastics of all kinds, including PVC (polyvinyl chloride), silicone, polyethylene, and polyurethane, are frequently used materials.
Safety and sanitation: The tubing is made to be tasteless, odorless, and non-toxic so that it won't taint or degrade the quality of the food or drink being delivered. To maintain good hygiene, it should also be bacterial growth-resistant and simple to clean.
Chemical Compatibility: Food and beverage tubing needs to be resistant to substances used in cleaning, preparing foods, and producing beverages, such as acids, alkalis, and acids. This guarantees that the tubing won't deteriorate or leak dangerous substances into the goods.
Temperature Resistance: The tubing must be able to endure the wide temperature variations needed for the many food and beverage processing steps, such as hot liquids, refrigeration, and freezing.
Flexibility and toughness: Flexible tubing enables simple routing and installation inside processing equipment. It should be made so that it can be bent, twisted, and compressed repeatedly without breaking, kinking, or collapsing.
Color-Coding or Transparency: Transparent tubing enables visual examination of the contents and any potential obstructions. Color-coded tubing may occasionally be used to distinguish between various fluid kinds or to adhere to industry standards.
Flexible tubing for the food and beverage sector is utilised in a variety of activities, including ingredient and additive delivery, beverage pumping, connecting dispensing equipment, moving liquids between tanks, and filling and packing operations.
When choosing food and beverage flexible tubing, it's crucial to take the application's specific needs, legal requirements, compatibility with the fluids it will be exposed to, and environmental factors into account.
Such tubing's producers and suppliers frequently offer comprehensive requirements and certifications to guarantee that it is acceptable for usage in the food and beverage sector.
The Canada Food And Beverage Flexible Tubing Market accounted for $XX Billion in 2022 and is anticipated to reach $XX Billion by 2030, registering a CAGR of XX% from 2023 to 2030.
VersilonTM XFR, a super-flexible, lightweight suction and discharge hose created for food and beverage transfer applications, is introduced by Saint-Gobain. Version XFR hose is a single food and beverage transfer solution that combines ergonomic handling and simple cleaning.
Because of its high flexibility and reduced weight than conventional suction and discharge hoses, XFR makes it easier to attach pumps and storage tanks. Numerous food product categories, including dairy, beer, wine, and spirits, are compatible with the hose.
The inner bromobutyl rubber tube of the XFR lowers the chance of flavor contamination and complies with FDA regulations.
The smooth, wavy blue hose cover complies with FDA regulations and is resistant to abrasion, ozone, aging, oil, and chemicals.When dragged across the floor, its wide corrugated low friction material leaves no stains and is simple to clean.
Sl no | Topic |
1 | Market Segmentation |
2 | Scope of the report |
3 | Abbreviations |
4 | Research Methodology |
5 | Executive Summary |
6 | Introduction |
7 | Insights from Industry stakeholders |
8 | Cost breakdown of Product by sub-components and average profit margin |
9 | Disruptive innovation in the Industry |
10 | Technology trends in the Industry |
11 | Consumer trends in the industry |
12 | Recent Production Milestones |
13 | Component Manufacturing in US, EU and China |
14 | COVID-19 impact on overall market |
15 | COVID-19 impact on Production of components |
16 | COVID-19 impact on Point of sale |
17 | Market Segmentation, Dynamics and Forecast by Geography, 2023-2030 |
18 | Market Segmentation, Dynamics and Forecast by Product Type, 2023-2030 |
19 | Market Segmentation, Dynamics and Forecast by Application, 2023-2030 |
20 | Market Segmentation, Dynamics and Forecast by End use, 2023-2030 |
21 | Product installation rate by OEM, 2023 |
22 | Incline/Decline in Average B-2-B selling price in past 5 years |
23 | Competition from substitute products |
24 | Gross margin and average profitability of suppliers |
25 | New product development in past 12 months |
26 | M&A in past 12 months |
27 | Growth strategy of leading players |
28 | Market share of vendors, 2023 |
29 | Company Profiles |
30 | Unmet needs and opportunity for new suppliers |
31 | Conclusion |
32 | Appendix |