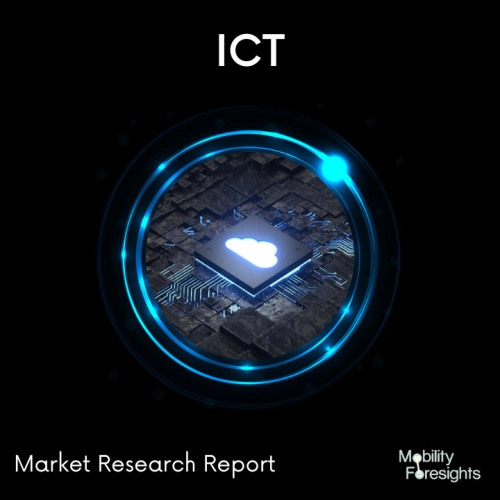
- Get in Touch with Us
Last Updated: Apr 25, 2025 | Study Period: 2022-2030
Due to the tiny size of the fibres, which makes them difficult to see, plus the complexity and continuous nature of the manufacturing process, inline hand inspection is usually not practicable. This results in an inefficient and inaccurate procedure.
Small carbon fibres are used. Managers at Fraunhofer IGCV engaged in the experiment, estimate that a single filament has a diameter of 7â12 micrometres, or roughly 0.0003 of an inch.
The Global carbon fiber automated inspection system market accounted for $XX Billion in 2021 and is anticipated to reach $XX Billion by 2030, registering a CAGR of XX% from 2022 to 2030.
Aerospace-grade carbon fibre is still largely rated manually, and this procedure is frequently fraught with mistakes made by humans. To consistently assure high-quality standards during production, automated monitoring solutions are required.
Fraunhofer IGCV, Europe's largest application-oriented research organisation, collaborated with SGL Carbon GmbH and Chromasens GmbH to develop the next-generation AirCarbon III automatic inspection system for monitoring carbon fibre production and related processes. This system builds on the success of the AirCarbon II automatic inspection system introduced earlier.
For smooth and continuous surface monitoring, the AirCarbon III system utilises a Chromasens allPIXA wave line scan camera and a Chromasens Corona II LED line scan light.
In order to identify the many kinds of carbon fibre flaws, AirCarbon III looks for projecting filaments, lint, and similar foreign substances.
The AirCarbon III system, in conjunction with data management and a user-centered interface, offers continuous and automatic monitoring of the carbon fibre production processes, from precursor generation through the different intermediate steps to the final sized fibre.
Sl no | Topic |
1 | Market Segmentation |
2 | Scope of the report |
3 | Abbreviations |
4 | Research Methodology |
5 | Executive Summary |
6 | Introduction |
7 | Insights from Industry stakeholders |
8 | Cost breakdown of Product by sub-components and average profit margin |
9 | Disruptive innovation in the Industry |
10 | Technology trends in the Industry |
11 | Consumer trends in the industry |
12 | Recent Production Milestones |
13 | Component Manufacturing in US, EU and China |
14 | COVID-19 impact on overall market |
15 | COVID-19 impact on Production of components |
16 | COVID-19 impact on Point of sale |
17 | Market Segmentation, Dynamics and Forecast by Geography, 2022-2030 |
18 | Market Segmentation, Dynamics and Forecast by Product Type, 2022-2030 |
19 | Market Segmentation, Dynamics and Forecast by Application, 2022-2030 |
20 | Market Segmentation, Dynamics and Forecast by End use, 2022-2030 |
21 | Product installation rate by OEM, 2022 |
22 | Incline/Decline in Average B-2-B selling price in past 5 years |
23 | Competition from substitute products |
24 | Gross margin and average profitability of suppliers |
25 | New product development in past 12 months |
26 | M&A in past 12 months |
27 | Growth strategy of leading players |
28 | Market share of vendors, 2022 |
29 | Company Profiles |
30 | Unmet needs and opportunity for new suppliers |
31 | Conclusion |
32 | Appendix |