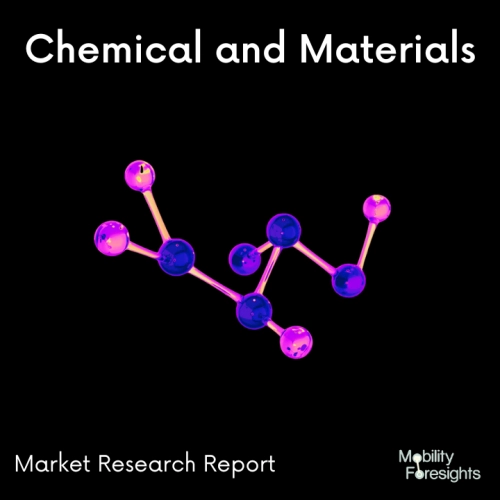
- Get in Touch with Us
Last Updated: Apr 25, 2025 | Study Period: 2024-2030
When compared to metallic materials, a well-constructed carbon frame significantly saves weight while preserving the strength and stiffness required by high performance bicycles and the riders that ride them.
Nearly two decades ago, carbon fibre practically took over the world of competitive cycling, but the bike industry has since produced ever-lighter, stronger, and more remarkable designs that were not conceivable to produce in metal.
On a small scale, carbon fibre is actually just as simple to work with as metal tubes. Smaller American businesses and even lone builders can use carbon instead of only the finished tubes that are sold by businesses.
Every bicycle manufacturer liberally sprinkles terms like "high-modulus" or even "ultra high-modulus" throughout its documentation on frame design. However, the bike business does not have the right to use those phrases.
Carbon fibre is measured for stiffness using tensile modulus, which measures how much a material will flex under tension. These ratings for carbon fibre, together with the stiffness range each one covers, are established.
Global carbon fiber bicycle market accounted for $XX Billion in 2023 and is anticipated to reach $XX Billion by 2030, registering a CAGR of XX% from 2024 to 2030.
After launching its UK-made carbon fibre Vekta aero-road bike through sister company REAP Bikes, Kamm Projects Ltd, a business that specialises in the production of composite, polyurethane, and fiber-reinforced materials for a variety of industries, reports that it is looking to the future.
The bike is made for racers, triathletes, and road riders who demand more stiffness, speed, comfort, efficiency, precision, and response from their equipment. It is said to offer next-generation frame performance.
The Gibbs Humdinga amphibious vehicle, for example, used carbon fibre prepreg with an infusion process for the vehicle's structural components. Kamm Projects has also worked on a variety of high-end manufacturers, including Bentley Motors, who used structural reaction injection moulding for the interiors of their vehicles.
The founder and managing director of REAP, believed that the cycling market had room for a variety of precisely constructed, highly effective bikes made with uncompromising materials and processes that big companies deem too expensive for mass production. Meir is a former professional triathlete with decades of experience who is still active in amateur competition.
Sl no | Topic |
1 | Market Segmentation |
2 | Scope of the report |
3 | Abbreviations |
4 | Research Methodology |
5 | Executive Summary |
6 | Introduction |
7 | Insights from Industry stakeholders |
8 | Cost breakdown of Product by sub-components and average profit margin |
9 | Disruptive innovation in the Industry |
10 | Technology trends in the Industry |
11 | Consumer trends in the industry |
12 | Recent Production Milestones |
13 | Component Manufacturing in US, EU and China |
14 | COVID-19 impact on overall market |
15 | COVID-19 impact on Production of components |
16 | COVID-19 impact on Point of sale |
17 | Market Segmentation, Dynamics and Forecast by Geography, 2024-2030 |
18 | Market Segmentation, Dynamics and Forecast by Product Type, 2024-2030 |
19 | Market Segmentation, Dynamics and Forecast by Application, 2024-2030 |
20 | Market Segmentation, Dynamics and Forecast by End use, 2024-2030 |
21 | Product installation rate by OEM, 2023 |
22 | Incline/Decline in Average B-2-B selling price in past 5 years |
23 | Competition from substitute products |
24 | Gross margin and average profitability of suppliers |
25 | New product development in past 12 months |
26 | M&A in past 12 months |
27 | Growth strategy of leading players |
28 | Market share of vendors, 2023 |
29 | Company Profiles |
30 | Unmet needs and opportunity for new suppliers |
31 | Conclusion |
32 | Appendix |