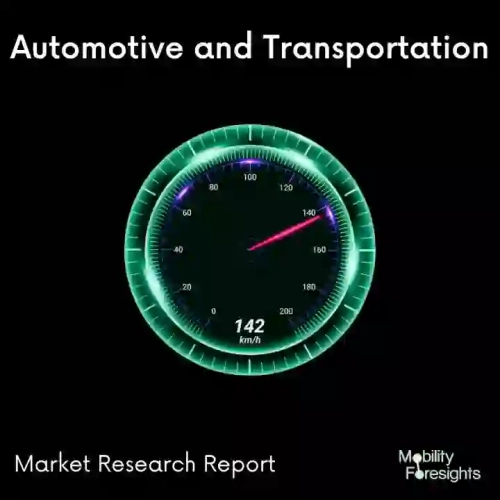
- Get in Touch with Us
Last Updated: Apr 25, 2025 | Study Period: 2024-2030
The drive shaft usually known as the propeller shaft or prop shaft is indeed an element of a car's powertrain that transfers torque first from gearbox towards the differential, which further sends this torque towards the axles to accelerate the automobile.
Because various components would have to be at multiple locations in the automobile, the drive shaft is mostly utilised to coursing between elements that are separated by a distance. Because the rear axle and transmission are on different sides of the car, a front-engine rear-wheel drive vehicle should have a lengthy drive shaft connecting them.
A carbon fiber driveshaft was designed, allowing for a 1000 RPM boost in usable rotational speeds and allowing the powerplant to breathe easier. Whenever torque is applied, all drive shafts rotate to a certain extent.
Torsional spring rate is a resistance of a material towards this rotation. Carbon fiber composite drive shafts have a somewhat lower transverse spring constant than aluminium and roughly half those of the steel.
A reduced spring rate results in much less driveline disturbance as well as less load on other drivetrain components, as well as greater traction.
Carbon fiber drive axles are primarily designed for robustness and torque transmission; however they can be damaged with a powerful side hit. The constant twist caused by torque ultimately leads all metal shafts to twist very little.
The shaft ends get persistently outside from sync by a few degrees throughout duration, and vibration begins to wear out elements. Carbon fiber drive shafts, on the other hand, have virtually flawless elasticity flexibility, which means they could perhaps fracture.
Weight reduction has become a key priority for inventors and manufacturers in the automobile sector. Because of the benefits that hollow shafts offer over solid drive shafts, the preponderance of passenger automobiles employ them as a drive shaft.
A hollow drive shaft of the same mass as a solid drive shaft functions in the same way as a solid drive shaft without failing. As a result, this is causing growth. Electric car sales have been increasing in recent years, and it is expected that this trend will continue in the next few years.
Furthermore, several electric car manufacturers intend to introduce new electric vehicle models in the next few years. Furthermore, major automakers are moving their attention towards concerns about the ecosystem and rising energy prices.
Steel, aluminium, and carbon fiber are used to make automobile propeller shafts. Carbon fiber is used because it is lightweight and strong, allowing the drive shafts to be harmonized. As a result, the rotational speed increases while the overall weight of the vehicle decreases.
Carbon Fiber driving shafts lower the total performance of the car and cause it to use less gasoline. As a result, these overall qualities of drive shafts are expected to fuel market expansion.
The continent's consumption for automotive is expanding rapidly, mainly to the region's large emerging nations, such as China and India, where demand for both passenger cars and commercial vehicles is increasing year after year.
Developments such as rising all-wheel-drive auto sales, rising SUV sales, and rising need for lightweight materials are projected to boost the automotive driveshaft market in the future years.
The Global Carbon Fiber Driveshaft Market can be segmented into following categories for further analysis.
A connecting shaft, an inner constant velocity joint, and an outside immovable joint comprise the driving shaft of a front-wheel output. Other components include torsional dampers and anti-lock system rings. The vehicle is equipped with flexible bearings or mountings that link the transmission unit and engine. The hydraulic springs, on the other hand, are used to link the wheels, differential, and rear axle. Several functional considerations interplay in the design of driveshafts.
A driveshaft, which would be essentially a thin-walled hollow tube, must be rigid enough to withstand collapsing at a specific engine torque output, such as 2,500 lb-ft in a high-end, 500-cubic-inch racing engine running at 8,000 rpm.Despite the fact that the universal joint connections at either end of the driveshaft alleviate a significant amount of stress in the shifting angles in the drivetrain, the shaft must work effectively because the rear axle is continually moving in respect to the engine.
Carbon fiber drive shafts provide the most weight reduction. Although aluminium driveshafts are incredibly light, carbon fiber adds a few kilograms. However, this is not the most significant benefit of carbon fiber. Carbon fiber, unlike steel or aluminium, does not shear when broken. The composite shaft has an inherent vibration dampening feature due to the epoxy matrix of the carbon fiber.
With the exception of steel or aluminium, which can be welded, carbon fiberâs structural strength is irreversibly compromised if a single strand is destroyed. This would be challenging if carbon fiber drive shafts have been marketed comparably to steel and aluminium competitors, but carbon fiber is a specialty material that is difficult to manufacture, therefore they are also significantly more expensive.
Due to the obvious fierce rivalry in the global automotive industry, market participants are increasingly focused on developing energy-efficient automobiles that conform to the criteria established in order to expand their market share in the present market scenario. Because of the increased emphasis on energy economy and environmental preservation over the last decade, car manufacturers are investigating the possibility of employing vehicle drive shafts made of materials other than steel to achieve these goals.
Another big element that is anticipated to affect overall growth is the considerable increase in utility vehicle sales across the world.
PST Technologies is part of the developing scale of operations in the carbon fiber driveshaft markets. They have been developing new technologies focused on better weight reduction methodologies and technologies.
The 3.75-inch Carbon fiber Drag Race driveshaft is required when developing or rebuilding a racing automobile. The difference during 60-foot launches with torsional springs rates that provide seamless and fluid sliding. This reduces driveline stress and increases element lifespan.
This drag racing shaft is offered in the 1350 or 1480 series, with different thicknesses that correspond to performance needs. This element is designed to withstand the rigours of 3,000 HP. This is also a shaft that works well in extended applications like trucks and early-model OEM-chassis vehicles. This shaft has been independently tested to bear torque of 2,800 ft/lbs. This reduces driveline stress and increases element longevity.
BAC Technologies is also a global scale developer of the carbon fiber technology shafts in the market. The joint design is a one-of-a-kind/proprietary blend of geometrical, equipment specifications, and design and manufacturing approaches. This has resulted in a construction with zero failure rates across a wide range of shaft varieties and decades of manufacturing. In all of these designed driveshaft designs, we employ the strongest, highest costly carbon fiber strands accessible.
The material we utilise is 33% stronger than standard, regularly used carbon fiber. In addition, the yoke ends are made of the greatest quality, most costly aluminium alloy. We do not manufacture our yoke ends from the lower strength alloy 6061-T6.
Sl no | Topic |
1 | Market Segmentation |
2 | Scope of the report |
3 | Abbreviations |
4 | Research Methodology |
5 | Executive Summary |
6 | Introduction |
7 | Insights from Industry stakeholders |
8 | Cost breakdown of Product by sub-components and average profit margin |
9 | Disruptive innovation in theIndustry |
10 | Technology trends in the Industry |
11 | Consumer trends in the industry |
12 | Recent Production Milestones |
13 | Component Manufacturing in US, EU and China |
14 | COVID-19 impact on overall market |
15 | COVID-19 impact on Production of components |
16 | COVID-19 impact on Point of sale |
17 | Market Segmentation, Dynamics and Forecast by Geography, 2022-2027 |
18 | Market Segmentation, Dynamics and Forecast by Product Type, 2022-2027 |
19 | Market Segmentation, Dynamics and Forecast by Application, 2022-2027 |
20 | Market Segmentation, Dynamics and Forecast by End use, 2022-2027 |
21 | Product installation rate by OEM, 2022 |
22 | Incline/Decline in Average B-2-B selling price in past 5 years |
23 | Competition from substitute products |
24 | Gross margin and average profitability of suppliers |
25 | New product development in past 12 months |
26 | M&A in past 12 months |
27 | Growth strategy of leading players |
28 | Market share of vendors, 2022 |
29 | Company Profiles |
30 | Unmet needs and opportunity for new suppliers |
31 | Conclusion |
32 | Appendix |