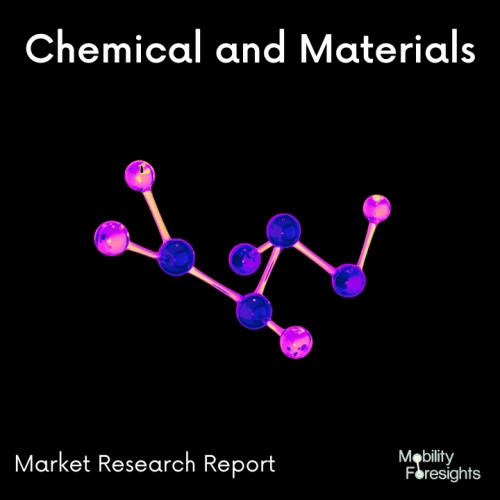
- Get in Touch with Us
Last Updated: Apr 25, 2025 | Study Period: 2023-2030
Carbon fiber hospital beds are widely used in modern medical equipment due to their low absorption rate, light weight, high strength, high modulus, fatigue resistance, ease of X-ray penetration, and fatigue resistance.
such as a computer tomography (CT) or radiation therapy (RT) machine, among others Most medical CT bed boards use insulated electric panels, which have poor mechanical properties, low ray transmittance, and poor imaging clarity.
Carbon fiber composite materials have a much lower absorption rate and scattering rate than carbon fiber composite materials. During diagnosis, the X-ray dose can be reduced, the X-ray machine's power can be decreased, the instrument's service life can be extended, and electric energy can be saved.
More importantly, carbon fiber composite material has excellent X-ray transmission properties, allowing rays to irradiate the bed at any angle without refraction and requiring only a small dose to produce a clear image, lowering patient risk. and the dangers posed by medical personnel.
Carbon fiber prepreg is used to laminate the Carbon Fiber Hospital Bed. Artifacts can be prevented by fully impregnating the resin and base material and uniformizing the structure of the bed board. Because carbon fiber is very permeable to X-rays, it can make it easier for X-rays to get into the human body accurately and without error.
A high-definition pattern appears on the screen after numerous conversions. Carbon fiber composite panels have a flat, smooth, light weight, and compressive surface, and their X-ray perspective is less than 1.0 mmAL. With obvious advantages, it takes the place of aluminum alloy panels and becomes the new option for a new generation of digital X-ray imaging technology.
The Global Carbon Fiber Hospital Bed market accounted for $XX Billion in 2022 and is anticipated to reach $XX Billion by 2030, registering a CAGR of XX% from 2023 to 2030.
The latest addition to Braskem's Carbon Fiber Hospital Bed is a novel carbon fiber reinforced polypropylene filament for 3D printing (CF-PP) (FL900PP-CF) with superior mechanical and thermal properties and low warpage. Braskem is the largest producer of biopolymers and polyolefins in the Americas.
The CF-PP filament from Braskem enables users to 3D print parts that are extremely rigid and lightweight for high-end applications like automotive, aerospace, nautical, sporting goods, and many more. The best part is that the FL00PP-CF is made entirely of recycled carbon fiber and performs similarly to products made of virgin carbon fiber.
We are proud to introduce our new polypropylene filament for 3D printing as the market leader in the United States for polypropylene. This new production capability provides our industrial clients and the general public with unparalleled new production capabilities for high strength and light weight additive manufacturing.
Whether you're a start-up, a university, a manufacturer of equipment, a converter, a compounder, or the owner of a brand, Braskem's carbon fiber reinforced polypropylene filament is redefining the possibilities for 3D printing design and engineering.
This most recent launch of a 3D printing product demonstrates Braskem's ongoing dedication to bringing innovative new solutions to the 3D printing industry, all of which make use of our dedicated additive manufacturing lab in our North American Innovation & Technology (I&T) Center in Pittsburgh, Pennsylvania.
THIS REPORT WILL ANSWER FOLLOWING QUESTIONS
Sl no | Topic |
1 | Market Segmentation |
2 | Scope of the report |
3 | Abbreviations |
4 | Research Methodology |
5 | Executive Summary |
6 | Introduction |
7 | Insights from Industry stakeholders |
8 | Cost breakdown of Product by sub-components and average profit margin |
9 | Disruptive innovation in the Industry |
10 | Technology trends in the Industry |
11 | Consumer trends in the industry |
12 | Recent Production Milestones |
13 | Component Manufacturing in US, EU and China |
14 | COVID-19 impact on overall market |
15 | COVID-19 impact on Production of components |
16 | COVID-19 impact on Point of sale |
17 | Market Segmentation, Dynamics and Forecast by Geography, 2023-2030 |
18 | Market Segmentation, Dynamics and Forecast by Product Type, 2023-2030 |
19 | Market Segmentation, Dynamics and Forecast by Application, 2023-2030 |
20 | Market Segmentation, Dynamics and Forecast by End use, 2023-2030 |
21 | Product installation rate by OEM, 2023 |
22 | Incline/Decline in Average B-2-B selling price in past 5 years |
23 | Competition from substitute products |
24 | Gross margin and average profitability of suppliers |
25 | New product development in past 12 months |
26 | M&A in past 12 months |
27 | Growth strategy of leading players |
28 | Market share of vendors, 2023 |
29 | Company Profiles |
30 | Unmet needs and opportunity for new suppliers |
31 | Conclusion |
32 | Appendix |